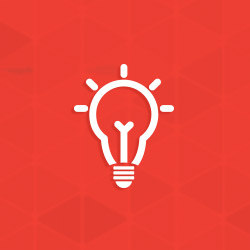
Maximum Coating Thickness
Is it possible to have too much galvanized coating on a steel part?
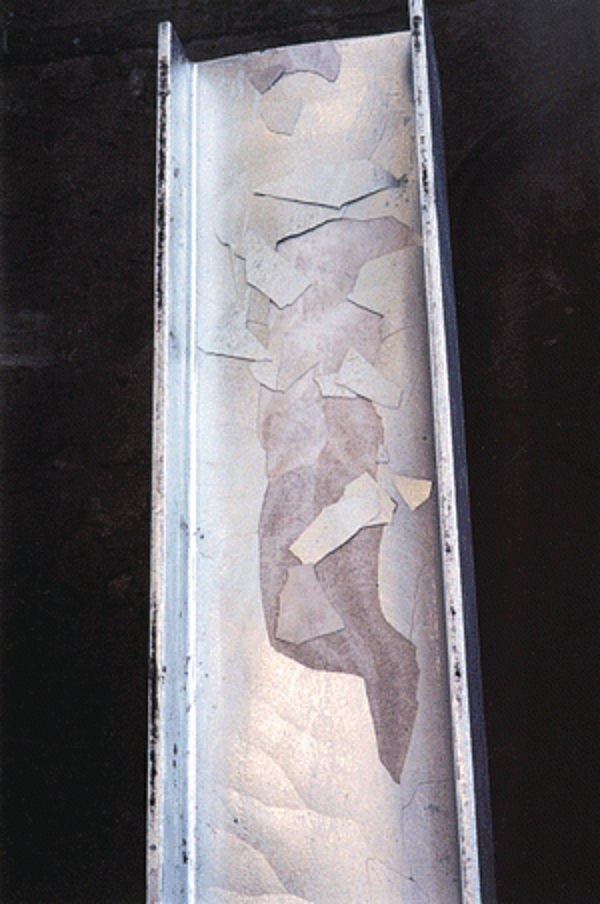
The specifications for hot-dip galvanizing do not set a maximum coating thickness, so there is no limit on the thickness of the hot-dip galvanized coating. However, there is a requirement the coating meets the intended use of the product, so if there are drips and runs in an area that will cause a fit problem in the parts final assembly, then the drips and runs must be ground smooth for the part to be acceptable.
Although the specification does not limit the coating thickness, there are some practical limits on how thick the galvanized coating should be. When the coating exceeds 10 mils or 250 microns, the coating experiences significant stress during the cooldown from galvanizing temperatures. The thermal contraction of steel progresses at a different rate than the thermal contraction of the intermetallic layers of the galvanized coating. This difference in contraction rates induces a stress at the interface between layers of the coating. The stress level induced depends on the thickness of the intermetallic layers. At normal coating thickness levels, the stress is minimal and there is no issue with the coating adherence. However, if the coating is thick then the stress can be significant, and this makes the coating susceptible to flaking as seen in the photo below.
The stress at the interface between layers may not cause immediate flaking of the coating but assembly, shipping or any other type of additional stress on the coating can cause a separation between the intermetallic layers and a flaking of the coating. Any time the coating is above the 10 mil or 250-micron thickness this flaking is a potential. The situation is more serious when the steel part is thick. Sheet metal parts cool very quickly so they dont usually experience this type of flaking but thick beams and poles can be very susceptible to flaking, of this type. All of this means it is very important to know when steel will have a very thick coating by knowing the steel chemistry or have a good idea from past jobs that the particular steel or part will have thick coatings and will be susceptible to potential flaking.
Besides the cost issues with adding 2 to 8 times as much zinc as is needed to the galvanized coating, the issue of flaking can make the part unacceptable to the customer and the added cost of stripping and re-galvanizing can hurt the bottom line. If the flaking does not show up until the part is at a job site, the shipping and other costs can turn this situation into a real nightmare. If the coating looks too thick, then measure the thickness so you know if there is a potential of flaking. If it is very thick, then test for flaking before you send the part to the job site. These steps will help save some of the potential extra costs for a flaking situation.
© 2025 American Galvanizers Association. The material provided herein has been developed to provide accurate and authoritative information about after-fabrication hot-dip galvanized steel. This material provides general information only and is not intended as a substitute for competent professional examination and verification as to suitability and applicability. The information provided herein is not intended as a representation or warranty on the part of the AGA. Anyone making use of this information assumes all liability arising from such use.