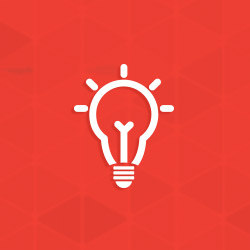
Limiting Coating Growth
I have heard time and time again from my galvanizer that the growth of the galvanized coating is beyond his control and what you get, you get.Surely there is something that can be done to control the coating growth in reactive steels? Why would a galvanizer want to limit the coating growth on reactive steels? Isn't corrosion protection proportional to coating thickness?
While its true that corrosion protection is proportional to coating thickness and, in turn, thicker coatings experience longer service lives there are some very valid reasons for limiting coating growth:
- Excessively-thick intermetallic layers tend to be more brittle and could flake off of the part during assembly and erection.
- Intermetallic crystals that reach the surface often have a different appearance than pure zinc, resulting in dark, gray, mottled, or matte coating finishes or a mixture of bright- and dark-appearing areas.
- The presence of intermetallics near the surface may lead to premature brown staining, causing an appearance change that makes it look like the coating isn't working as corrosion protection.
- Increased coating thickness leads to increased zinc consumption.
Surface Profiling
As shown in a comparison of the micrographs below, the crystals of the zeta layer in reactive steels are very pronounced and exaggerated. Because the growth of intermetallic crystals is perpendicular to the surface of the steel, it is possible to reduce the coating weights of reactive steels by introducing a new surface profile. Since the zeta layer grows in long vertical crystals, creating a jagged surface profile will cause these zeta crystals to grow into each other. This growing together will effectively limit the heights to which these crystals can grow, thus reducing the coating thickness. The surface of reactive steels can be profiled in a number of ways. Mechanical cleaning techniques may be used, such as wheel abrading or sand-blasting. Additionally, if sulphuric acid pickling operations are used, the galvanizer may over-pickle the part to provide a rougher surface profile.
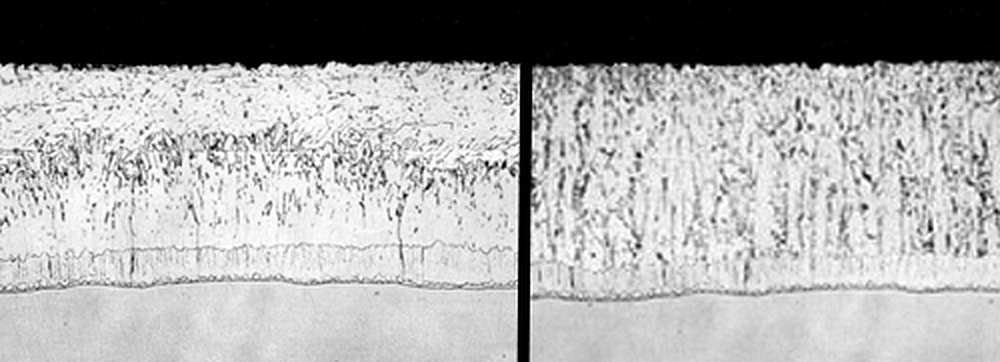
Zinc Bath Chemistry
The addition of nickel to the zinc bath reduces the coating weights in the Sandelin range (0.040.15 % Si ) of reactive steels, as well as any other steel with silicon below 0.15%. It effectively lowers the hump of the coating growth curve. There is a drawback to this solution, in that it may be difficult to reach required minimums on smooth, nonreactive steels with silicon less than 0.15%.
Galvanizing Temperature
Like most reactions, increasing the reaction temperature also increases the rate and extent of reaction. If a galvanizer knows he/she has a large load of steel that is reactive, high-silicon, or Sandelin-range silicon, he may choose to lower kettle temperature for that shift. Lowering below 820° F slows the galvanizing reaction and allows the galvanizer to spot the end of the zinc/iron reaction by the changes in the bath surface. This gives the galvanizer time to remove the part from the zinc bath in time to prevent the growth of a thick coating.
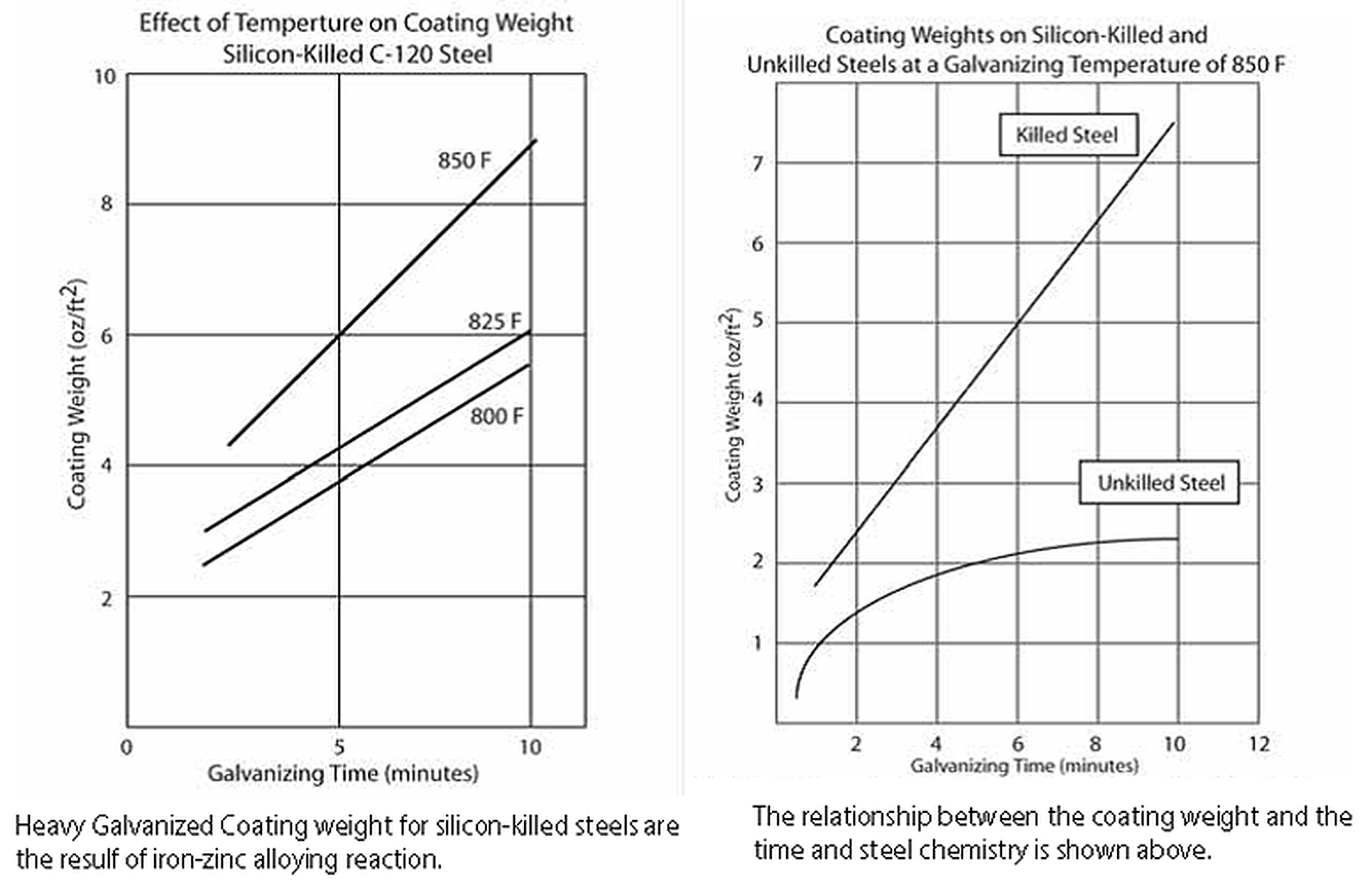
Immersion Time
Silicon acts as a catalyst in the galvanizing reaction. Since high-silicon steels react very quickly in the galvanizing bath, limiting the immersion or dwell time in the kettle can be another effective solution for keeping coating thickness down. The kinetics of the galvanizing reaction is different. Reactive steels experience linear coating growth, where coating growth is proportional to immersion time. Nonreactive steels experience parabolic coating growth, where the thickness is proportional to the square root of the immersion time. There are practical limitations on the minimum temperature and immersion times which can be employed, imposed by the bath size and sectional thickness of the material, danger of freezing the bath, and on the need for sufficient temperature to allow good drainage of the free zinc upon withdrawal from the kettle.
Conclusion
So the galvanizer has some control over the coating thickness on reactive steels when he knows ahead of time that the steel he is going to put into his kettle is reactive steel. For large orders, it is always a good practice to try some sample pieces to find out how the coating quality looks before trying to run large lots.
© 2025 American Galvanizers Association. The material provided herein has been developed to provide accurate and authoritative information about after-fabrication hot-dip galvanized steel. This material provides general information only and is not intended as a substitute for competent professional examination and verification as to suitability and applicability. The information provided herein is not intended as a representation or warranty on the part of the AGA. Anyone making use of this information assumes all liability arising from such use.