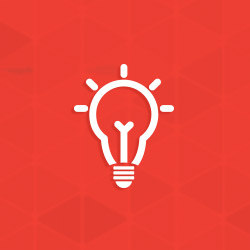
Inclusions on the Galvanized Coating
Can a fabricator or specifier reject finished galvanized product because of zinc skimming deposits or flux inclusions on the surface, or is touch-up acceptable?
Before I answer your question, a brief background about each coating variation will be beneficial. This article will define the terms zinc skimming deposits and flux inclusions, discuss the composition of each, and then discuss what ASTM A123/A123M allows and rejects when these coating variations appear on galvanized steel.
Zinc Skimming
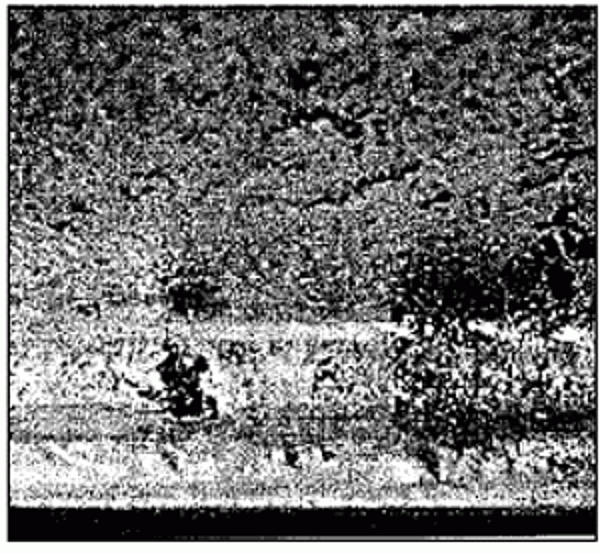
During the normal operation of the galvanizing process, zinc skimmings develop on the exposed zinc bath surface as it reacts with air to form a thin layer of zinc oxide particles. Galvanizing line personnel lightly skim away this thin layer of particles before lowering the steel into the kettle. Some oxides remain on the zinc bath surface. Once the steel is in the kettle, the surface of the zinc begins reacting with the air again, forming another thin layer of zinc oxide particles. Some zinc chloride also accumulates in these particles as flux from the steel evaporates from the steel as it is lowered into the kettle. Before line personnel withdraws the steel from the kettle, they once again clear zinc skimming from the surface.
During the withdrawal of the steel from the molten zinc, it is possible for any remaining surface skimmings or skimmings under the part to attach to the surface or become trapped under the surface of flat sections or inside of galvanized steel tubes. Zinc skimmings appear as black or gray deposits and consist of zinc oxide and zinc chloride mixtures. The micrograph (above) shows zinc skimmings on the galvanized coating. The deposits appear as black voids. The gamma, delta, and zeta layers are intact, and the skimmings deposit on top of the surface of the free-inc (eta) layer. This is important to note because it means a galvanized coating has formed under the zinc skimmings, rather than the skimmings depositing directly onto the steel and preventing galvanizing. Therefore zinc skimmings do not affect the time to first maintenance of the galvanized coating.
Flux Inclusions
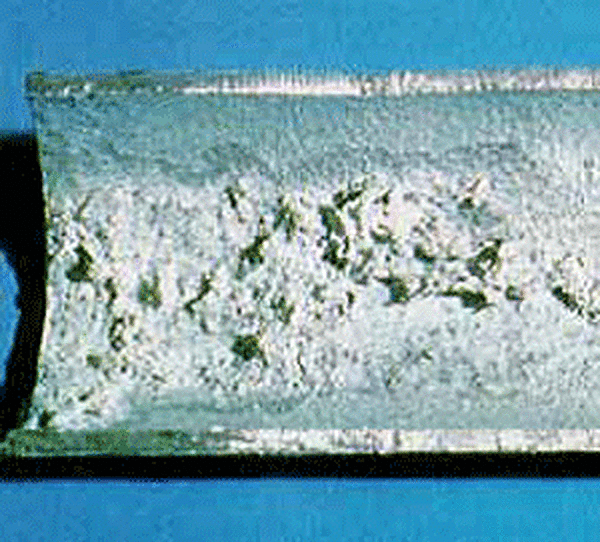
During the cleaning portion of the galvanizing process, the steel is dipped into the flux bath to prevent oxide formation before it reaches the galvanizing kettle. If oxides form on the steel surface they can inhibit the metallurgical reaction from happening and thus there would be uncoated spots on the steel after galvanizing. Flux normally releases from the steel in the molten zinc and allows the metallurgical reaction to occur. If the flux does not release from the steel, that area will not galvanize.
Flux inclusions are composed primarily of zinc chloride from the zinc ammonium chloride mixture in the flux bath and appear black or gray in color. Flux inclusions pose a corrosion problem in two ways. First, there is little or no galvanized coating under the flux inclusion, meaning bare steel can be exposed when the flux is removed from the steel. Second, flux crystals can combine with atmospheric moisture, rain, or dew to form hydrochloric acid, which then attacks the surrounding galvanized coating and the bare steel.
A123 Requirements for Zinc Skimmings and Flux Inclusions
A 123/A 123M states Upon shipment from the galvanizing facility, galvanized articles shall be free from uncoated areas, blisters, flux deposits, and gross dross inclusions. Therefore, zinc skimmings that do not interfere with the intended use of the product are permitted. The steel is fully protected because there is a galvanized coating underneath the skimmings, and any differences in appearance will even out over time as the coating weathers. ASTM A 123/A123M clearly states flux inclusions are not permitted and must be removed from the galvanized coating and repaired in accordance with ASTM A780.
A 123/A 123M states Each area subject to renovation shall be one inch or less in its narrowest dimension. The total area subject to renovation on each article shall be no more than ½ of 1% of the accessible surface area to be coated on that article, or 362 in. per short ton of piece weight, whichever is less. Flux inclusions on the interior of a hollow part that cannot be accessed for repairs, such as on pipe or tube as seen in the bottom right photo below - must be rejected. Parts rejected for flux deposits may be stripped of their zinc coating and then re-galvanized.
Preventing Coating Variation
Deposit of zinc skimmings onto the galvanized surface can be reduced by limiting the amount of splashing when clearing skimmings and brushing away skimmings often. Flux inclusions can be reduced by control of the inspection of the flux bath and monitoring of the aluminum levels in the galvanizing kettle.
© 2025 American Galvanizers Association. The material provided herein has been developed to provide accurate and authoritative information about after-fabrication hot-dip galvanized steel. This material provides general information only and is not intended as a substitute for competent professional examination and verification as to suitability and applicability. The information provided herein is not intended as a representation or warranty on the part of the AGA. Anyone making use of this information assumes all liability arising from such use.