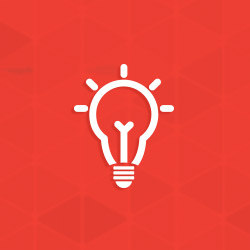
Galvanized Steels Performance in Extreme Temperatures
How does hot-dip galvanized steel perform in environments with extreme temperatures (either hot or cold)?
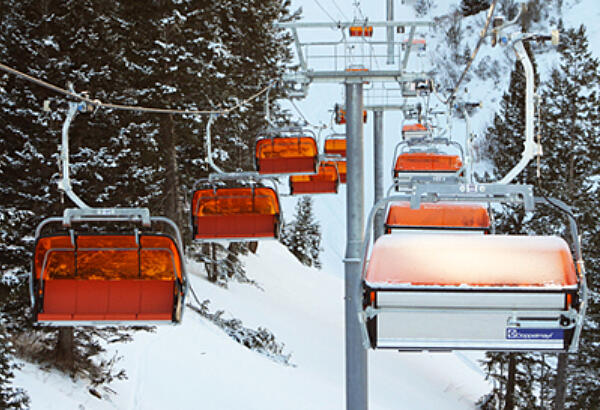
Galvanized Steel in High-Temperature Environments
There are some concerns with using hot-dip galvanized steel in an elevated temperature environment. The industry has recommended the service temperature for conventional coatings to be less than 390 F (200 C). The concerns with operating above this high-temperature limit include peeling, some changes in mechanical properties, and a reduction in corrosion protection.
Peeling
Peeling is caused by metallurgical changes that create a series of closely spaced voids at the free zinc-alloy interface. These voids are produced by a diffusion of zinc from the outer free zinc layer into the inner alloy layer. When these voids expand and form a gap, it causes the outer free zinc layer to split-off from the underlying zinc-iron alloy layers. This process is known as the Kirkendall Effect and is illustrated in Figure 1.
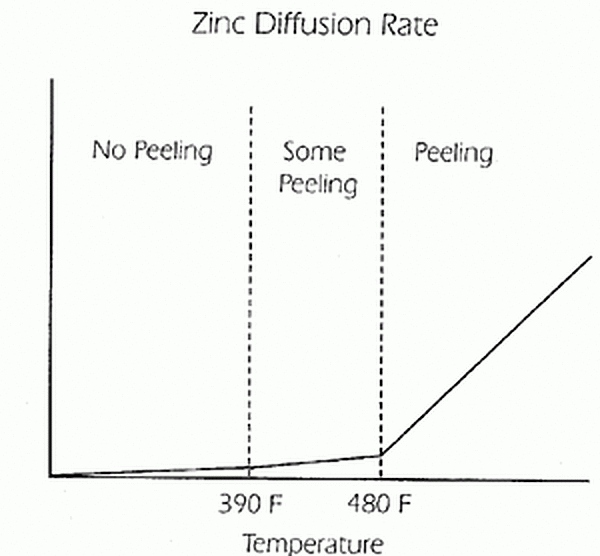
However, the remaining zinc-iron alloy layers will still provide a high level of corrosion protection for many years, exactly how long depends on the coating thickness remaining. At temperatures ranging from 390 F (200 C) to 480 F (250 C), the zinc-iron alloy layers will continue to protect the steel from corrosion.
High temperatures above 480 F (250 C) will accelerate peeling and continued exposure can result in the zinc-iron alloy layers cracking and separating from the steel. Figure 2 shows the peeling of galvanized steel versus the temperature of the environment. This is also related to the zinc diffusion rate.
Apart from the predominant effect of the time/temperature conditions, the rate of the deterioration process is influenced by coating thickness, the relative thickness of outer zinc and iron-zinc alloy, and by the uniformity of the individual layers. By its effect on the length of the zinc diffusion path or the rate of the iron-zinc interdiffusion reaction, any of the coatings factors can affect the speed and degree of coatings deterioration. At or below the industry-recommended limiting service temperature of 390 F, the coating resists zinc layer peeling.
As discussed, peeling does occur at temperatures above 390 F and is dependent on the rise in temperature and the duration exposed. But this does not mean corrosion protection is lost. During peeling, only the outer free zinc layer has become detached, leaving the zinc-iron alloy layers to provide corrosion protection to the steel.
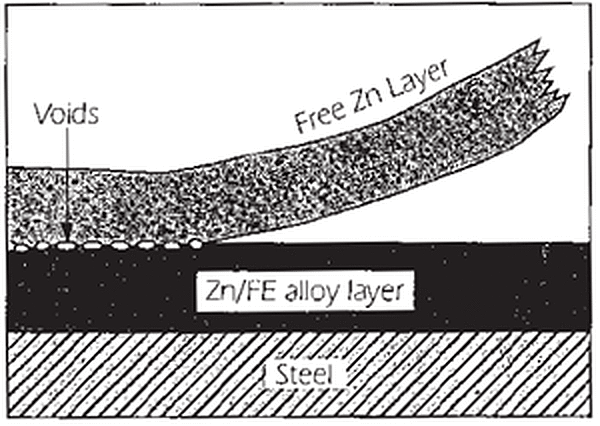
Some investigators have found that the peeling effect was greatly reduced when the zinc coating contained very low levels of lead, less than 0.001 percent Pb. Others parameters that affected the peeling where the coating thickness and the time and temperature of heating. These investigators found that brief temperatures excursion up to 300 C could be handled with no coating problems.
Occasionally the American Galvanizers Association gets the question of whether the galvanized coating is adversely affected by exposure to fire. Temperatures in fires can easily exceed 1,000 F. There is a potential for coating damage but many have found fire damage to minimal on galvanized steel. Often a layer of carbon dust coats the galvanized surface and under this layer the coating is intact.
Changing Mechanical Properties
Another concern is that of changing the mechanical properties of the steel at high temperature. The mechanical properties of samples in the as-received condition and after heating at 750 F are as follows. Exposures from two weeks up to 16 weeks produced relatively minor changes, including a decrease in ultimate tensile strength and an increase in elongation. The yield strength was not significantly altered. These structural changes are insignificant and do not affect the design of steel structures.
Mechanical properties change only slightly at elevated temperatures and are not a significant issue. Galvanized product may be used at high temperatures for a limited time with the knowledge long exposure may generate severe peeling. The recommended service temperature of 390 F has been a good benchmark for coating protection with no free zinc peeling.
Galvanized Steel in Low-Temperature Environments
Studies done on the effect of low-temperature environments on HDG steel indicate a minimal change in the behavior of the galvanized coating. Some polar installations have used HDG steel for corrosion protection and have been in service for over twenty years. As with any steel at very low temperatures, the material becomes brittle with extended use. Low-temperature climates are an appropriate use of hot-dip galvanized steel.
© 2025 American Galvanizers Association. The material provided herein has been developed to provide accurate and authoritative information about after-fabrication hot-dip galvanized steel. This material provides general information only and is not intended as a substitute for competent professional examination and verification as to suitability and applicability. The information provided herein is not intended as a representation or warranty on the part of the AGA. Anyone making use of this information assumes all liability arising from such use.