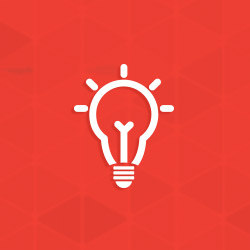
Embrittlement and Welding in Galvanized Stainless Steel
Is it true that welding galvanized stainless steel can cause embrittlement?
When extreme levels of corrosion protection are required, sometimes stainless steel is galvanized. This provides great corrosion protection; however, welding this type of corrosion protection system is a concern. When certain types of metals become molten, they can cause cracking in other types of metals. A few examples of this include mercury causing cracking in copper alloys, cadmium causing cracking in titanium, and zinc, aluminum, or lead causing cracking in austenitic stainless steels. (R.W. Staehle, Stress Corrosion Cracking and Hydrogen Embrittlement of Iron BaseAlloys. Houston, TX: NACE, 1977.)
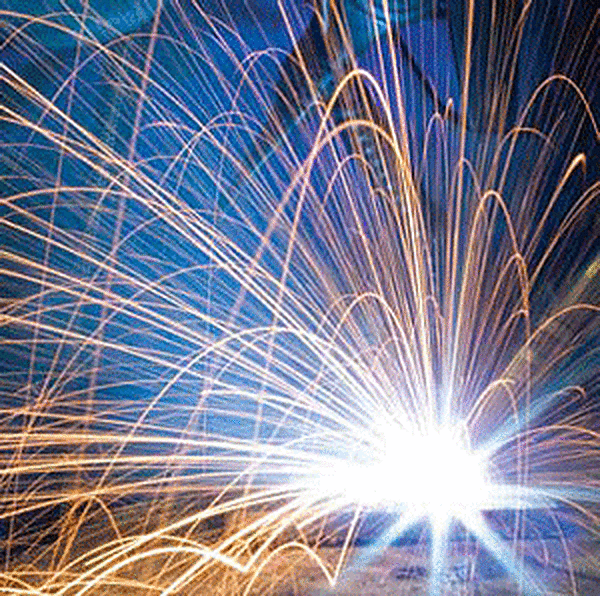
Because the galvanized coating is applied for corrosion protection, it is not expected to ever become molten, yet there are two instances when it can. The first instance is when stainless steel that has been galvanized is welded. This could also mean welding stainless steel to galvanized steel, or vice versa. The second situation is when zinc from a galvanized coating and stainless steel come into contact in temperatures that cause the zinc to become molten. That is not an appropriate environmental condition for galvanized steel and will not be discussed here. Lets discuss the first instance in more detail. When galvanized stainless steel is welded, or when galvanized steel and stainless steel are welded together, the zinc becomes molten and can penetrate the stainless steel intergranularly, which then causes liquid metal cracking (LMC). An example of a situation where LMC happened in exactly this manner is discussed on page 179 in the NACE book, Fundamentals of Designing for Corrosion Control: A Corrosion Aid for the Designer.
The remedy for this situation is to remove the zinc from the area to be welded prior to welding. Fundamentals of Designing for Corrosion Control: A Corrosion Aid for the Designer states the best method to remove the zinc is by applying 20% muriatic acid (or another type of acid) and then thoroughly rinsing and drying the area prior to welding. The more common method of grinding the zinc away from the welded area can leave zinc particles on the welded area, which can then cause LMC. Hot-dip galvanizing is not the only type of zinc coating that may cause LMC on stainless steel. All other types of zinc coatings, including zinc-rich paint, can cause LMC when heated until molten and in contact with stainless steel.
Usually, the galvanizer is several steps removed from the erection process and intended application, but talking with your customer can go a long way to preventing a costly or dangerous situation. If you galvanize stainless steel for your customer, it would be a good idea to alert them to the potential for LMC if the steel is welded later.
© 2025 American Galvanizers Association. The material provided herein has been developed to provide accurate and authoritative information about after-fabrication hot-dip galvanized steel. This material provides general information only and is not intended as a substitute for competent professional examination and verification as to suitability and applicability. The information provided herein is not intended as a representation or warranty on the part of the AGA. Anyone making use of this information assumes all liability arising from such use.