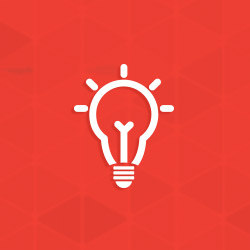
Dull Gray vs. Shiny Finishes
It is my understanding galvanizing process steps are similar for most items. Why is it some galvanized coatings have a dull, gray finish, while others have a bright, shiny finish? Also, which coating provides better corrosion protection?
It is true the galvanizing process is similar for most steel galvanized; however, there are several variables that affect the galvanizing process and determine product quality. These variables are steel chemistry, surface preparation, kettle chemistry, and steel exposure conditions during the galvanizing process.
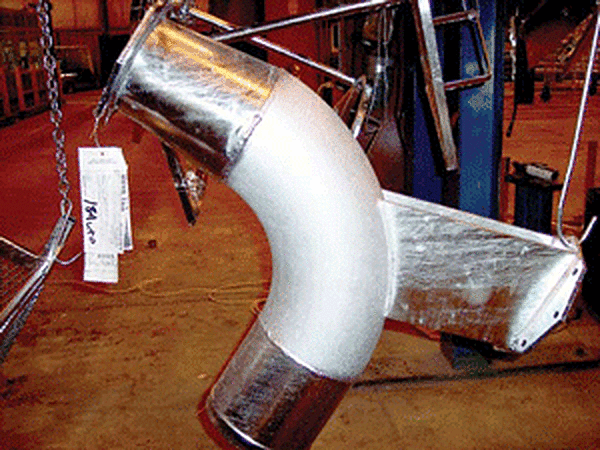
ASTM A123 acknowledges that silicon, phosphorus, and carbon content in steel affect the galvanized coating. ASTM A385 recommends limits and ranges for steel chemistry to ensure a high quality galvanized coating. The galvanized coating of steel with the recommended chemistry - non-reactive steel - will have a coating similar to the magnified coating in Figure 1. This coating has four distinct layers. The gamma, delta, and zeta layers are intermetallic alloy layers, and are harder than the base steel. The alloy layers give galvanized steel its outstanding abrasion resistance. The eta layer is the same composition as the zinc in the galvanizing kettle. The eta layer is responsible for the bright shiny appearance. Steel with chemistry outside the recommended limits and ranges for galvanizing is known as reactive steel.
A micrograph of a galvanized coating on reactive steel is shown in Figure 2. This coating has a very thin eta layer, although some reactive steels have no free zinc layer. Reactive steel has intermetallic alloy layers in the same order as non-reactive steel. However, the zeta layer in reactive steel is overgrown and tends to compose most of the galvanized coating thickness. Intermetallic layers do not have a bright shiny finish, and when exposed, appear dull gray. Galvanized coatings on reactive steels can be much thicker (over 10 mils) than coatings on non-reactive steel. The galvanized coating is created through a metallurgical reaction between iron in the steel and zinc in the galvanizing kettle.
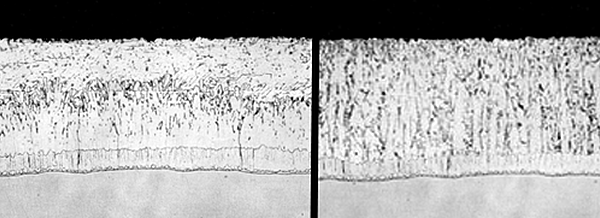
This reaction is a diffusion reaction and increases with increased exposure time or temperature. Silicon and phosphorus in the steel serve as catalysts during this reaction. For non-reactive steel, the metallurgical reaction is complete within six or seven minutes. Increasing exposure time has little effect on the coating thickness for non-reactive steel. For reactive steel, the coating experiences linear growth with respect to increased exposure time in the galvanizing kettle. This means the longer reactive steel is left in the kettle the thicker the coating will be. The coating layer that experiences the most growth from increased exposure time is the zeta layer, which grows in long vertical columns toward the coating surface. Kettle chemistry can affect the quality of the galvanized coating. Galvanizers add small amounts of aluminum to the zinc to increase coating brightness.
Variations in steel chemistry, surface preparation, kettle chemistry, and steel exposure conditions can cause a difference in coating appearance. Nickel can be added to the galvanizing bath to suppress steel reactivity by limiting growth of intermetallic layers. By limiting excessive intermetallic growth, nickel indirectly improves the brightness of the galvanized finish. Withdrawal speed can affect the thickness of the galvanized coating. The faster steel is removed from the galvanizing kettle, the less zinc is able to drain off the steel before solidifying.
This means faster withdrawal rates can create thicker coatings. Non-reactive steel completes its reaction with zinc after a few minutes in the kettle. However, reactive steel continues reacting as long as there is free zinc available and the temperature is high enough (greater than 500F) ? even when outside the galvanizing bath. This happens when reactive steel on thick, heavy parts is cooled slowly. If reactive steel consumes the entire eta layer, the zeta intermetallic layer will grow to the surface and will transform the part from shiny to dull as the part cools. When the steel is dipped into a quench tank immediately after galvanizing, the temperature of the steel drops several hundred degrees quickly; thus stopping the metallurgical reaction. Quench options include water, chromate and phosphate. Service life of the galvanized coating cannot be estimated from the appearance of the galvanized coating; it must be measured with a coating thickness gauge. The corrosion protection a galvanized coating offers is directly proportional to its thickness ? the thicker the coating, the greater the corrosion protection.
This means a dull gray coating that is thicker than a bright shiny coating will offer a longer service life. There are several ways to improve the brightness of galvanized coatings. The most important is to choose steel with chemistry within the recommended limits and ranges for silicon, phosphorus and carbon. If this is not possible, reactive steel can be blasted before galvanizing to roughen the steel surface. Roughening the steel surface creates peaks and valleys. These peaks and valleys interfere with growth of the zeta intermetallic layer because it grows in long columns toward the surface coating. Limiting submersion time in the kettle and using lower kettle temperatures will also help to suppress intermetallic growth on reactive steel. Adding aluminum to the galvanizing kettle directly improves the brightness of galvanized coatings, and nickel indirectly brightens the coating. Decreasing cooling time by quenching will also brighten the galvanized coating by preventing consumption of the eta layer.
© 2025 American Galvanizers Association. The material provided herein has been developed to provide accurate and authoritative information about after-fabrication hot-dip galvanized steel. This material provides general information only and is not intended as a substitute for competent professional examination and verification as to suitability and applicability. The information provided herein is not intended as a representation or warranty on the part of the AGA. Anyone making use of this information assumes all liability arising from such use.