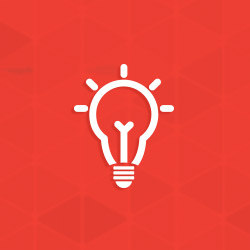
Dross Inclusions
What can I tell my customers about dross inclusions? I know they are acceptable in a finished product sometimes, but not others. Why is this?
Passing inspection under the specification ASTM A123 depends on the type of dross inclusion present on the surface of the finished galvanized product. Before I answer your question, lets address a brief background on dross.
What is dross?
Dross is defined as a byproduct of the galvanizing process that forms by reactions between molten zinc and loose particles of iron in the galvanizing kettle. The basis of hot-dip galvanizing is a metallurgical reaction between iron in steel with molten zinc in the kettle. In addition to the iron content in a customers steel, there are free iron particles in the kettle that also react with the zinc by the same metallurgical reaction. Free iron particles in the galvanizing kettle come from several different sources. Probably the largest source of these iron particles is iron salts resulting from reactions between the steel with acid salts in the pickling tank and flux from the pre-flux or wet flux layer. Another source of free iron particles is the galvanizing kettle itself and the steel being galvanized. These free iron particles remain in the solid state because zinc has a low solubility for iron, and the melting point for iron is much higher than the temperature used in the galvanizing process. In fact, the solubility of iron in zinc at a temperature of 850°F (454°C) is only 0.035% or 35 iron particles per 100,000 zinc particles. Iron concentrations above this percentage will particulate and then metallurgically react with the molten zinc to create dross. Iron solubility in molten zinc is affected by element additions to the bath (nickel and aluminum,) and to a greater degree by temperature changes. Dross production increases linearly by four times if the bath temperature changes from 880°F to 810°F (471°C to 432°C). At common temperatures used for galvanizing, dross is made of a mesh of zinc-iron alloy crystals encapsulated by molten zinc. Most dross drops to the bottom of the kettle because it is heavier than molten zinc. However, lowering and raising steel into the kettle, and convection currents caused by temperature differences in the kettle can help to keep the dross floating throughout the kettle.
Why is dross a problem?
Dross adheres to newly galvanized surfaces as the steel is removed from the galvanizing kettle. The size of these inclusions determines if the galvanized product is acceptable under ASTM A 123. According to ASTM A 123, newly galvanized steel must be free from gross dross inclusions. ASTM A 123 defines gross dross inclusions as the iron-zinc intermetallics present in a galvanized coating in a form other than finely dispersed pimples. Gross dross inclusions are further defined as inclusions that would create an exposed steel spot if they were removed from the coating. the specification says gross dross inclusions are raised surfaces and can be easily knocked off through contact with lifting straps or chains, tools, fixtures, or other galvanized parts. These definitions for gross dross inclusions are what determine if a newly galvanized product is acceptable under ASTM A 123. To pass inspection, gross dross inclusions must be removed from the newly galvanized surface and the underlying steel must be repaired according to ASTM A 780. Galvanized steel with dross pimples is acceptable, because it is surrounded by zinc coating, not easily removed, and does not affect corrosion protection.
How do you treat dross inclusions?
Preventing dross from forming in the kettle is the best way to minimize dross inclusions on the surface of your newly galvanized steel. There are several ways to limit the amount of loose iron present in the kettle. Iron particles can be reduced by fully rinsing steel after cleaning in the pickling tank, limiting the iron content in the preflux, and using the lowest possible effective ammonium chloride concentration in the preflux tank. Regulating element additions, such as nickel and aluminum, daily rather than weekly helps to limit iron precipitation in the molten zinc. Maintaining zinc kettle temperatures, especially near the top of the kettle, along the walls, greatly reduces floating dross. Lastly, frequently drossing the kettle will help to remove dross and thereby prevent the potential of inclusions.
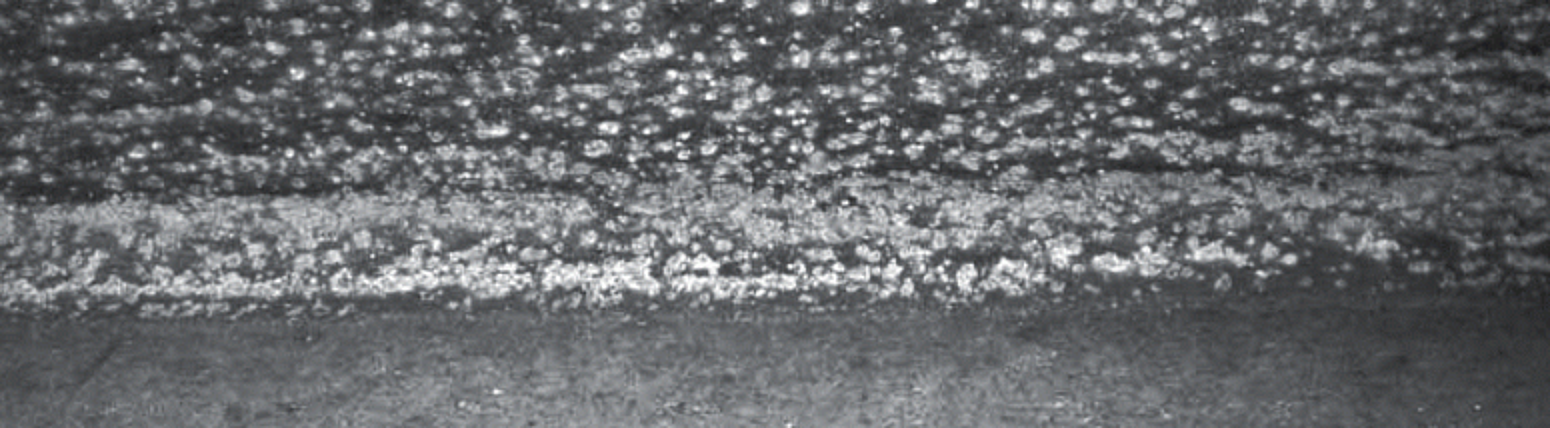
© 2025 American Galvanizers Association. The material provided herein has been developed to provide accurate and authoritative information about after-fabrication hot-dip galvanized steel. This material provides general information only and is not intended as a substitute for competent professional examination and verification as to suitability and applicability. The information provided herein is not intended as a representation or warranty on the part of the AGA. Anyone making use of this information assumes all liability arising from such use.