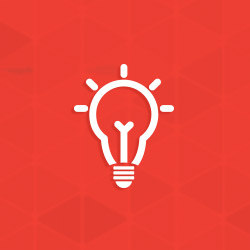
Damaged Galvanized Steel and Storage
I have inadvertently damaged some HDG steel I just received. There appears to be some scratch marks in the coating caused by rough handling and transport. Should I repair the scratches, or does the cathodic action of the zinc coating protect the damaged area?
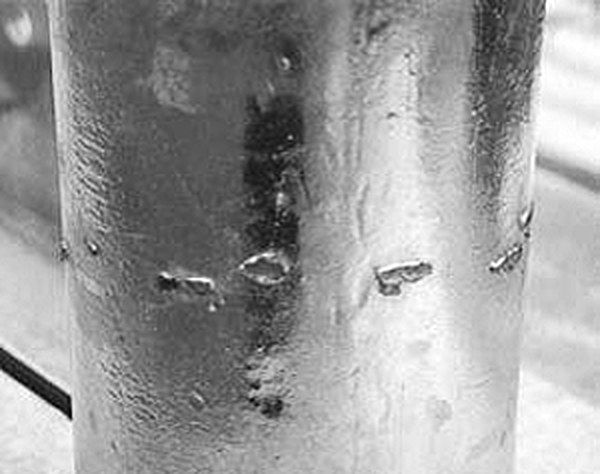
Depending on the extent of damage, repair may or may not be necessary. It is a well-known fact that galvanized coatings provide two forms of corrosion protection: barrier (like paints), and cathodic (electrochemical). The immersion of steel in zinc during galvanizing provides a zinc coating that completely covers the steel and limits corrosion by eliminating contact between corrosive elements and the steel. The other form of protection that galvanizing provides — cathodic — is from the electrochemical nature of zinc and steel. When zinc and steel are in contact, the zinc is the anode and the steel is the cathode. The anode (zinc) protects the cathode (steel) by sacrificing itself when the two are in contact in the presence of an electrolyte.
The cathodic protection of galvanized steel only occurs after the barrier has been broken. As in your case, the damage during shipping and handling has broken the barrier of the HDG coating, which will expose the steel to the environment. The extent of which the exposed steel is protected by the cathodic action of the zinc depends on a number of factors:
- The width of the damaged area;
- Zinc surface activity;
- The electrolyte.
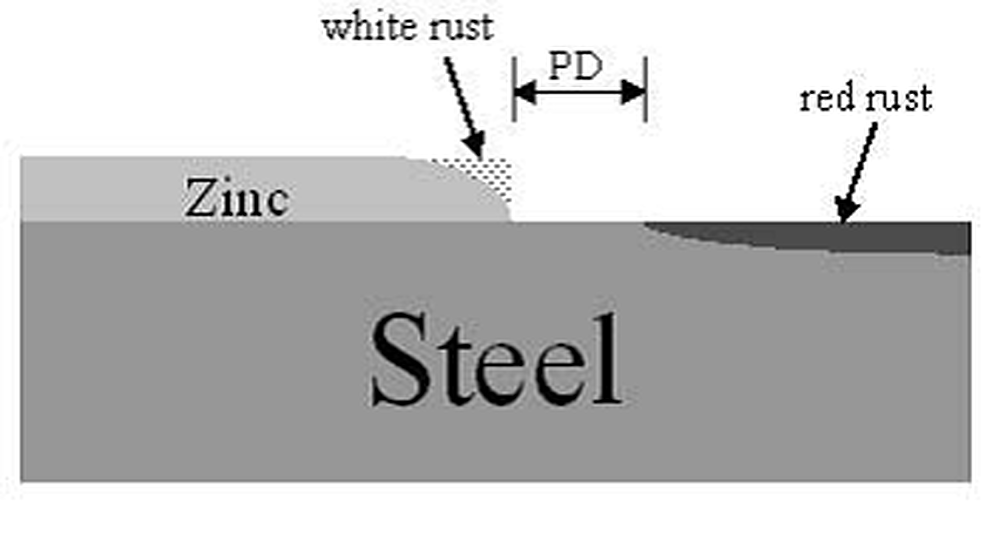
A recent study by Gregory Zhang from Teck Cominco and Anquin Xing from X-Numerical (presented at Galvatech 2004) evaluated the effects of these variables on the cathodic protection distance provided by zinc in a zinc-steel bimetallic couple:
The cathodic protection of zinc is limited by the width of the damaged area. The study conducted by Zhang and Xing showed that a critical distance exists signifying the maximum distance away from the zinc that it will protect the exposed steel (Figure 2, above). The maximum protection distance found (assuming a thin layer electrolyte and moderate zinc surface activity) was slightly greater than 1/4" (7 mm). However, once the width of the exposed steel increased beyond this distance, the protection distance decreases to a minimum of just over 1/8" (4 mm).
The surface activity of the zinc also plays a large role in determining the width of the damaged area that zinc can cathodically protect. The protection distance increases as the surface activity of the zinc increases. On the other hand, when the zinc surface is passive (low activity), the cathodic protection provided by the zinc is essentially zero. Therefore, as zinc passivates while exposed to the environment, the protection distance provided by the cathodic action of zinc will decrease over time. The protection distance will decrease due to the decreased surface activity as well as the loss of zinc from the steel/zinc interface as the zinc sacrifices itself to protect the exposed steel.
Possibly the most dominant factor in the cathodic protection that zinc provides to bare steel is the environment to which the galvanized steel will be exposed. The resistance of the electrolyte, or conductivity, will vary the protection distance provided by the zinc. A rule of thumb being, the protection distance decreases as the electrolyte resistance increases. When galvanized steel is exposed to saltwater environments, the projection distance is greater than when exposed to dry climates. The salt water provides better conductivity and thus a larger area that the zinc can cathodically protect. However, this larger area of protection comes at a price. The zinc cathodically protecting the exposed steel is consumed at a faster rate, thus decreasing the overall lifetime of the coating. Although the cathodic protection distance is greater, the consumption of zinc afforded by this type of protection will ultimately corrode the coating faster than in a rural, dry environment.
Getting back to your question, repairing any damage to galvanized steel will increase the overall life of the steel. However, economically speaking, it might not be necessary. Small scratches (< 1/8"), in mildly corrosive climates, do not necessarily need to be repaired. The cathodic protection of the zinc will prevent extensive corrosion of the steel. In highly corrosive environments, where corrosion protection is of paramount concern, repairs should be made to ensure the longest possible service life for the steel. Large scratches should always be repaired, regardless of environment.
© 2025 American Galvanizers Association. The material provided herein has been developed to provide accurate and authoritative information about after-fabrication hot-dip galvanized steel. This material provides general information only and is not intended as a substitute for competent professional examination and verification as to suitability and applicability. The information provided herein is not intended as a representation or warranty on the part of the AGA. Anyone making use of this information assumes all liability arising from such use.