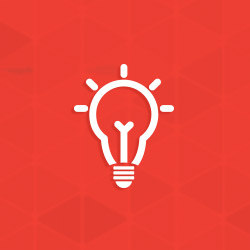
Coating Characteristics of Zinc-Rich Paint
Organic or inorganic zinc-rich paints are applied to a dry film thickness of 2.5 to 3.5 mils (64 to 90 µm). Organic zinc paints consist of epoxies, chlorinated hydrocarbons, and other polymers. Inorganic zinc paints are based largely on organic alkyl silicates. The zinc dust must be at a concentration high enough to provide for electrical conductivity in the dry film for cathodic protection to be possible. However, there is some question as to whether cathodic protection is possible at all due to the encapsulation of the zinc particles in the non-conductive binder.
Adhesion bond strengths of zinc-rich paints are a few hundred pounds per square inch (psi), while galvanized coatings measure in the several thousand psi range. Like metallizing, zinc-rich painting can be applied to large articles in either the shop or field. Limitations include cost, difficulty in applying, lack of coating uniformity (particularly at corners and edges), and the requirement for a clean steel surface. Zinc-rich paints should be top coated in severe environments.
Inorganic zinc-rich paints, which adhere with the substrate by mild chemical reactivity, have good solvent resistance and can withstand temperatures up to about 375 C (700 F). Inorganics do not chalk, peel, or blister readily, are easy to weld, and cleanup is easier than with organics.
Contents of inorganic zinc-rich paints range up to about 0.35 oz/ft2/mil of zinc, about one-half less zinc per mil than hot-dip galvanized coatings.
The properties of organic zinc-rich paints depend on the solvent system. Multiple coats may be applied within 24 hours without cracking. Zinc-rich paints are often used to touch up galvanized steel that has been damaged by welding or severe mechanical impact.
Limited to 200 to 300 F, organic zinc-rich paints do not have the temperature resistance of inorganic zincs. They are also subject to ultraviolet (sunlight) degradation, and are not as effective as inorganics in corrosion protection.
Zinc dust/zinc oxide paints (MZP) are classified under Federal Specification TT-P-641G as either Type I, Type II or Type III, depending on the vehicle. The vehicles used are linseed, alkyd resin, and phenolic resin, respectively. These paints are widely used as either a primer or topcoat and show good adhesion to galvanized steel, making them the logical choices for painting that substrate. Type I is good for outdoor applications, Type II for heat-resistant applications, and Type III for water immersion or severe moisture conditions. MZPs cannot provide sacrificial protection to the base steel because of their lower metallic zinc content. When used as a coating over galvanized steel, the service life of the galvanized coating is extended because of the increased barrier protection of the paint. The service life of the paint is also extended as the galvanized surface is a better substrate than steel. Zinc (galvanized) corrosion products are less voluminous than iron (steel) corrosion products minimizing the incidence of lifting and separation of the paint film. MZPs can be top-coated with a variety of paint types if colors other than gray, green or tan (from pigmented additives) are desired.
See the Zinc Coatings Publication for more information.
© 2025 American Galvanizers Association. The material provided herein has been developed to provide accurate and authoritative information about after-fabrication hot-dip galvanized steel. This material provides general information only and is not intended as a substitute for competent professional examination and verification as to suitability and applicability. The information provided herein is not intended as a representation or warranty on the part of the AGA. Anyone making use of this information assumes all liability arising from such use.