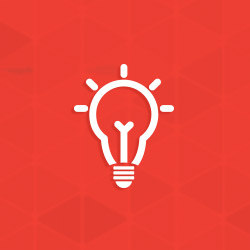
Cleaning Galvanized Steel
How do I clean grease or wet storage stain from galvanized steel without damaging the appearance of the coating?
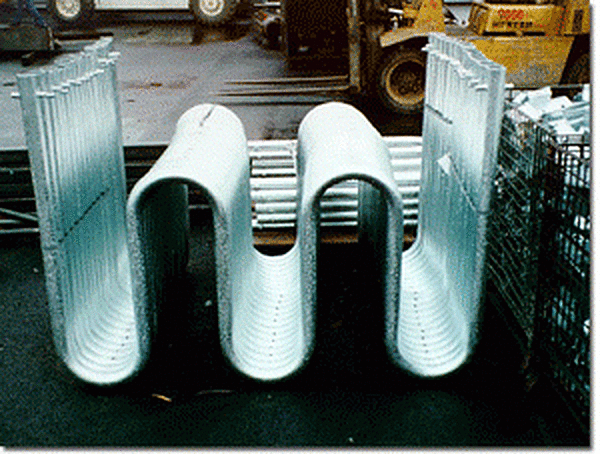
Regardless of how clean any galvanizing operation is, at some point, organic contaminants like grease or oil will find their way onto your newly galvanized steel. Similarly, when it is especially damp or humid outside, moisture can accumulate on stored galvanized steel waiting to be shipped and cause wet storage stain. In the interest of providing your customer with the highest quality service, you like to clean those contaminants or impurities from the surface prior to delivery of the product. However, to keep customer satisfaction intact, you want to use cleaning products that affect the finish of the coating as little as possible. The following will provide you details of a cleaning study conducted by the AGA.
Cleaning Organic Contaminants from Galvanized Surfaces
The AGA recently conducted a study to test which commercially available products are best at removing organic contaminants from galvanized steel. Many products were tested, and most of them worked very well at removing the contaminants without affecting the finish of the coating. Cleaning with these products consisted of applying and removing the product to the galvanized surface in accordance with the manufacturers instructions, rinsing with water and then drying. The following products did not damage the coating:
- Comet®
- Bleach
- Goof Off®
- Simple Green®
- The Must for Rust®
- Stainless Steel Cleaner
Even though these products did not damage the appearance or cause other damage to the coating in the study, you should still test a small area at first to be cautious. There were other products that effectively removed grease and oil, but also affected the appearance of the galvanized coating in some way. These products include:
- Vinegar
- Muriatic acid
- Ammonia
Cleaning Wet Storage Stain from Galvanized Steel
The best way to treat wet storage stain is to prevent it. Preventing wet storage stain is accomplished in two ways:
- Providing adequate air flow to newly galvanized surfaces
- Removing standing water from newly galvanized surfaces.
Properly storing newly galvanized steel does both. However, there are times when the formation of wet storage stain cannot be prevented and must be removed. Wet storage stain can range in severity from light to heavy. Light and medium wet storage stain do not affect the service life of the coating, while heavy wet storage stain can. The first step in treating wet storage stain is to dry the galvanized surface. Light wet storage stain can usually be left untreated as long as the surface will remain dry and will be exposed to adequate air flow. Over time the coating will regain its normal appearance as the zinc patina forms. Medium and heavy wet storage stain must be removed from the surface to prevent continued consumption of the galvanized coating. In cases of very heavy wet storage stain, the part may need to be stripped and re-galvanized. The AGA conducted a study to test various products for removing wet storage stain without damaging the galvanized coating or the appearance. Five products were found that meet these criteria:
- CLR®
- Lime juice
- Naval Jelly® Rust Dissolver
- Picklex 10G
- White vinegar
These products can be applied to the affected areas and then scrubbed with a nylon-bristled brush. After cleaning the wet storage stain, you will need to rinse the surface and dry it.
Additional Resources
The studies to test these various products for removing organic contaminants and wet storage stain from galvanized steel have been summarized into Galvanizing Notes, and are available for download in the members area of the AGA website. Alternatively, you can contact the AGA Technical Department to obtain copies of these publications.
© 2025 American Galvanizers Association. The material provided herein has been developed to provide accurate and authoritative information about after-fabrication hot-dip galvanized steel. This material provides general information only and is not intended as a substitute for competent professional examination and verification as to suitability and applicability. The information provided herein is not intended as a representation or warranty on the part of the AGA. Anyone making use of this information assumes all liability arising from such use.