Airports
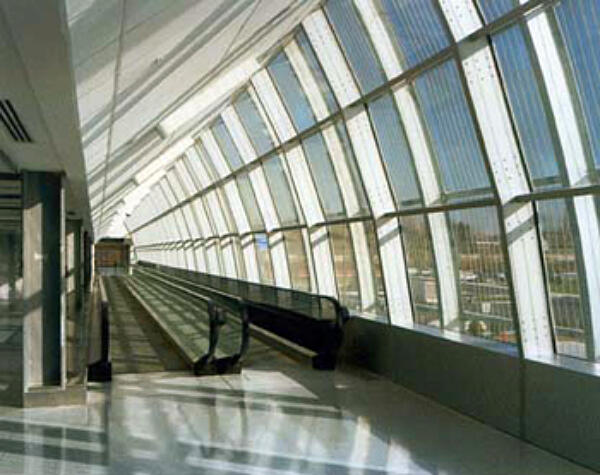
Travelers begin their busy journeys at airport parking garages, terminals, and concourses. These areas serve as a traveler's gateway to their destination, and delays due to maintenance, structural instability, or corrosion are unacceptable in such a time-sensitive transportation hub. Hot-dip galvanized steel can provide durable corrosion protection that will keep terminal services humming at a fast, uninterrupted pace. In the terminals and concourses, hot-dip galvanizing can protect structural steel, stairwells, and railings from the rigors of exposure to the elements, as well as stand up to the daily abuse of fast-moving baggage in conveyors, sorting machinery, destination-coded vehicles, and carts. In parking garages steel can be used to benefit the facility aesthetically as well as protect against damage and corrosive elements presented by constant traffic.
Terminals/Concourse
A hive of activity, airport terminals face some of the roughest abuses of any transportation system, including baggage conveyors and pushers, destination-coded vehicles (DCV's), sorting machinery, and baggage carts. Handled roughly and battered by thousands of bags a day, these systems need the durable protection of galvanized steel to continue functioning properly, unhindered by corrosion or maintenance delays. Above and surrounding all this activity, exposed structural steel elements can allow natural light to enter the facility; soothing travelers and creating a light, airy experience within the walls of the airport. Hot-dip galvanized steel exterior stairwells and railings can face the abuse of rain, snow, and deicing materials, while standing strong against abrasion for decades. Whether located inside or out, each of these sectors can benefit from the durable corrosion and abrasion-resistance of hot-dip galvanized steel.
Baggage Handling
Though every traveler can witness the frenetic hum of activity inside the terminals and courses, some of the most hectic work is carried out behind the scenes. To get your luggage to and from your destination, a complex baggage handling system takes each suitcase from the check-in point to the plane. In the rush to complete this task on time, passengers witness how sturdy, heavy luggage can be roughly handled en route. Imagine tens of thousands of bags a day brutalizing the system of conveyors, pushers, destination-coded vehicles (DCV's), sorting machinery, and baggage carts, roughly thrown, banging about, and generally creating one of the most abrasive environments imaginable.

Hot-dip galvanized steel elements can be utilized in many places throughout this process, including: conveyor supports and tracking, metal plates and carts on DCV's, and in baggage carts used to move baggage to and from planes. Utilizing hot-dip galvanized steel for these elements means they will benefit from the superior barrier and cathodic protection provided by the zinc coating created during the galvanizing process. Also, no moisture from bags that have been rained or snowed upon will be able to penetrate the zinc coverage as the move along the line. Moisture can lead to corrosion, which will slow down the progression, or perhaps even put conveyors of DCV's out of use for maintenance repairs, an unacceptable threat easily remedied with galvanized steel.
Within a few months of galvanizing, the coating also naturally develops an impervious zinc patina that contributes to the unparalleled barrier protection provided by galvanized steel. The barrier protection of the zinc coating will stand strong against the daily onslaught of searing sun, pelting rain, freezing snow, and other natural elements, as well as fend off the damaging effects of chemicals from transportation pollution or de-icing applications. This will greatly benefit baggage carts that move from the plane outdoors to the baggage system inside, openly exposed to the elements and pooling runway de-icing salts.
Baggage systems will not only benefit from the impenetrable barrier protection of the zinc coating; they will also primarily benefit from the inherent cathodic protection of the metallurgically bonded zinc coating. Cathodic protection means if individual areas of underlying steel or iron become exposed by as much as 1/4" in diameter, the surrounding zinc will sacrificially provide these areas with corrosion protection for as long as the coating lasts. This indicates the protected steel will stand strong against inevitable nicks and scratches created by the constant abuse of baggage handlers and thrown luggage. Suitcases can grind against and land heavily on the surface without making the steel vulnerable to spreading corrosion. With galvanized steel, dings and scratches will not compromise the corrosion protection of the piece. A roughly-used baggage system requires the dual support of strong barrier and cathodic protection to keep the line moving and baggage to the travelers in record time.
Exterior Terminal Elements
Exposed terminal elements also take advantage of hot-dip galvanized steel's unparalleled corrosion protection. Fire-escapes, ramps, stairwells, or guardrail erected for traveler use or staff entries/exits benefit from the durable barrier and cathodic protection provided by the tightly adhered zinc coating created during the galvanizing process. With a bond strength of 3,600 psi, the zinc coating will not chip or flake due to abrasion from foot traffic or rolling, bumping baggage. This barrier protection will also prevent exposure to rain, snow, or deicers tracked in on the feet of users from causing deteriorating corrosion.
Structural Steel
To achieve a striking facility capable of drawing higher traffic, structural steel framing can be bent and arched into striking shapes, and galvanized steel can protect these attractive elements from corrosion. The Charlotte Douglas International Airport Parking Garage Terminal features a unique convex exterior façade reminiscent of the curvature of an airplane wing. A steel framed structure also allows the possibility of incorporating skylights and ceiling windows to create an open space and interior filled with natural lighting. These aesthetic advantages can create a facility that will be soothing to anxious travelers and make the airport stand out architecturally. Galvanized steel will protect the exposed portion of these structural elements from deterioration due to rust or corrosion. This will keep the structure safe and attractive for generations of travelers to admire.
Airfield
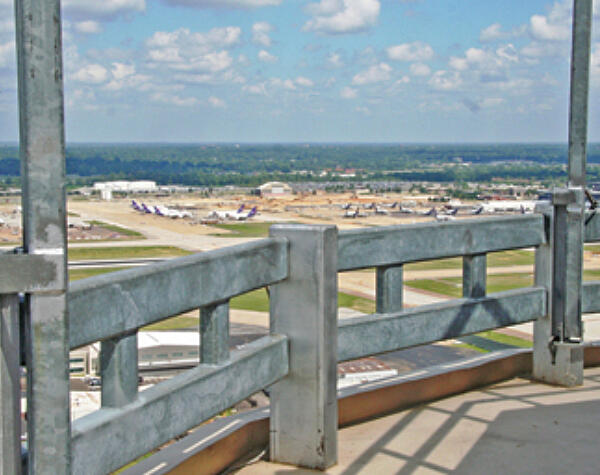
Sitting aboard a plane, high above the tarmac, you may not realize, but steel is all around in the ground below. Within the concrete in the surrounding air ramp, or "apron", taxiways, runways, or air tower controls, reinforcing steel is often used to increase the tensile strength of the concrete. Moving around the apron, the Ground Support Equipment (GSE) includes moveable stairways for ground deplaning; baggage chutes; luggage trolleys, vehicles and pallets; food and beverage catering lifts, and more are critical to maintaining smooth traffic flow at any airport. Finally, jetways connect the airfield to the terminals, and are often a visual indicator of the state of upkeep and maintenance at an airport. Galvanized steel can keep these elements looking attractive and functioning properly, corrosion-free. Exposed structures such as jet bridges, moveable stairways and chutes, and other ground boarding equipment such as ramps or railings are investments that also need protection from deterioration. Utilizing hot-dip galvanized steel for these structures will provide the maintenance-free durability, seismic resistance, and corrosion protection necessary to keep airport operations running smoothly. At a distance, air control towers stand tall, directing traffic to and from the airport. These parapets, often made of concrete, are also supported by reinforcing steel, and can even be made entirely out of structural steel for a more modern, appealing look. Galvanized steel provides several benefits to these structures.
Reinforcing Steel (Rebar) Protection
Sometimes more than 12 inches thick, the concrete aprons, taxiways, and runways must support the heavy weight of plane traffic. A fully loaded 747 can weigh up to 900,000 lbs. and with hundreds of planes traversing the airport ground space daily, this can take a considerable toll on the concrete below. Widely used in a variety of concrete applications, from roads to bridges to buildings, reinforcing steel bar (rebar) is used to enhance the tensile strength of the surrounding concrete in applications such as runways and aprons. However, the addition of these strengthening elements can prove problematic if proper care is not taken to avoid corrosion. Because of the porous nature of concrete, moisture and cold weather treatment chemicals can seep into the concrete, reaching the rebar within. This is especially problematic for aprons and runways, which are open and exposed to rain and snow, and are repeatedly treated with harshly corrosive salts and de-icers to prevent hazardous conditions for the planes.
Exposed to these corrosive elements, the rebar will begin to develop rust corrosion products that are 2-10 times more voluminous than the original steel pieces. As these corrosion products continue to build, stress on the surrounding concrete increases until the surface begins to crack and spall. Spalling can create loose concrete, cracks, bumps, and potholes that can potentially damage airplane taxi gear, as well as pose a hazard to mobile airport equipment such as baggage trolleys, moveable stairwells, or other ground equipment. If a baggage trolley hits a particularly nasty pothole, baggage may even be ejected from the vehicle. Potholes and cracks can be especially hazardous for landing aircraft traveling at high speeds, even a small bump in the landing zone can create dire consequences. A smooth runway makes for a smooth , safe landing.
Ground Support Equipment (GSE)
These elements account for much of the "behind the scenes" magic of an airport, moving passengers and getting baggage to the sorting facility, thus smooth, uninterrupted operation is of paramount importance. However, GSE are exposed to highly abrasive and corrosive conditions, rough handling and constant outdoor exposure to rain, snow, and de-icing chemicals can wear these pieces down, causing maintenance delays or even requiring replacement.
By utilizing hot-dip galvanized steel where applicable, airport operations can continue to hum along thanks to the superior abrasion resistance and barrier protection of the zinc coating. Galvanized steel also allows the unique opportunity to take advantage of a duplex system for corrosion protection, which will allow branded airline equipment to have both the superior protection of galvanized steel and the required aesthetic necessary to promote airline recognition.
Jet Bridges
Jet bridges, also known as jetways, connect travelers from the terminal to the plane itself during the boarding process. Whether fixed or contractible, these structures can take advantage of the durable corrosion protection provided by using hot-dip galvanized steel for the framing system. Similar to ground support equipment, jet bridges are consistently exposed to the outdoor elements. Left unprotected, rust can render these structures immobile, unable to contract, or simply structurally unsafe. To protect against the ravages of corrosion, the impenetrable zinc coating developed during the galvanizing process means no moisture will seep in to cause corrosion. With a bond strength of 3,600 psi, the coating will not flake or chip off under continued exposure to moisture, allowing the jet bridge to stand safe and strong under the effects of nature.
An emphasis on airport aesthetics can also serve to soothe the nervous traveler. As many jet bridges are easily visible from gate windows, a well-kept, rust-free structure can serve to reassure waiting passengers of the safety of both the airport and, indirectly, the coming flight as well. Contrarily, visible deterioration caused by corrosion can leave passengers feeling unsettled and leave a negative impression of the facility and airline.
Airports Case Study
Blast Deflectors, Inc.- JFK International Airport
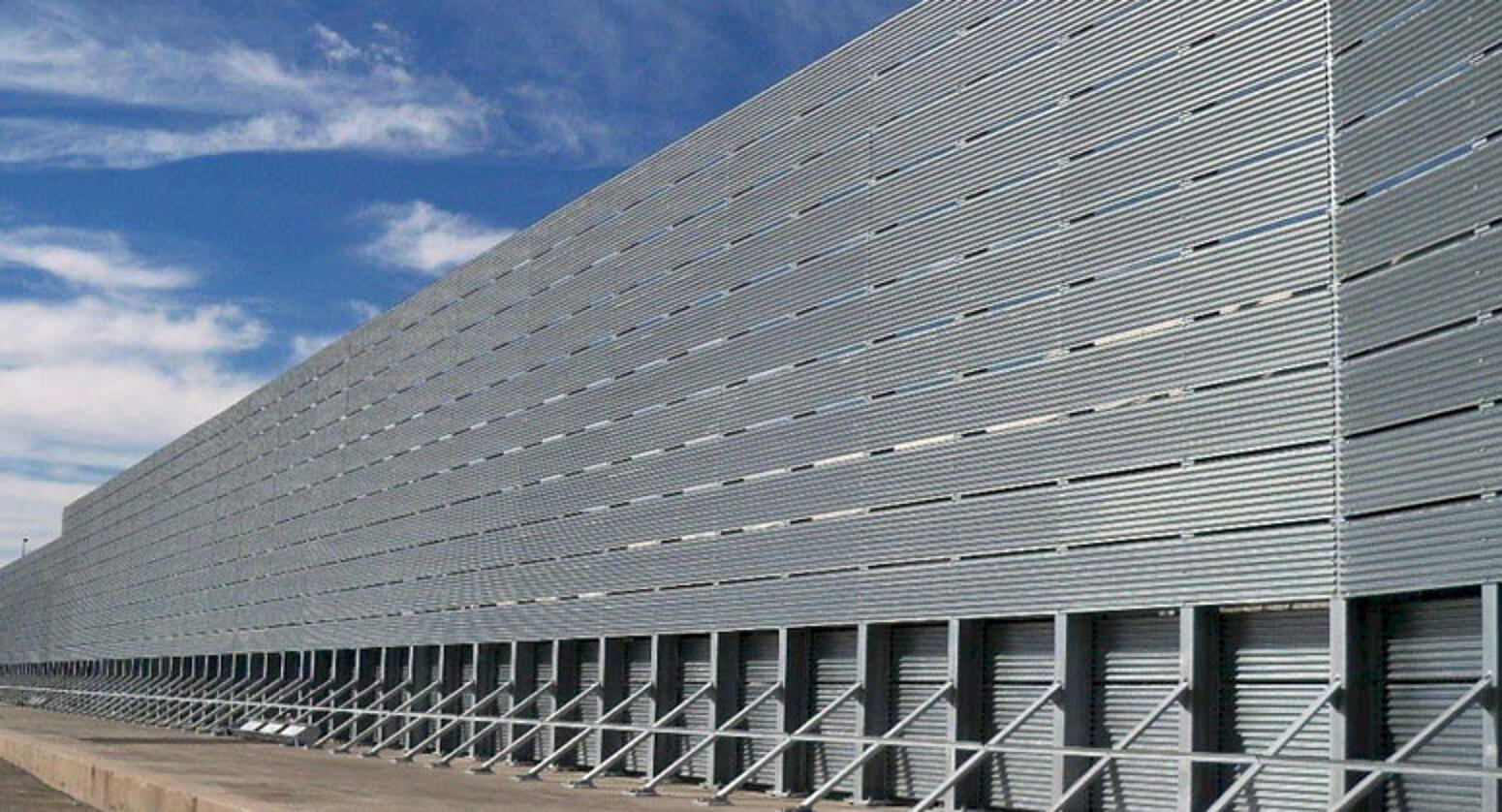
Blast Deflectors, Incorporated (BDI) is one of a few manufacturers of jet blast deflectors in the world. They recently designed and installed their biggest and most durable deflectors to date at John F. Kennedy International Airport in New York City, and hot-dip galvanizing (HDG) was specified as the protective coating. Located just minutes from Manhattan, JFK Airport services nearly 25 million airline passengers annually and is one of the busiest airports in the country. The height of the blast deflector extends above the adjacent parking structure, making it highly visible to travelers and airport personnel. HDG ensures that the deflector's appearance as well as its functionality and structural integrity will be preserved for many years.