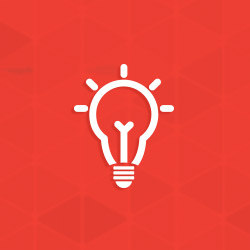
Silicon Content of Steel
I told my customer what the perfect number for the silicon content of the steel should be, and he said he had the perfect steel. When I galvanized his steel, it came out with 6 mils of coating and dull gray, not bright and shiny. What happened and what can I tell my customer?
The silicon content of steel is determined through a mill test report. Silicon is not just one value through the heat of steel but is rather some type of distribution throughout the heat. Just what the distribution actually contains is not known, but lets try to put some numbers together for an estimate. Say the steel has a mill test report with a silicon value of 0.04%. Where is this value within the distribution of silicon values throughout the steel? Is it the maximum, the minimum, the average, the mean or some other function of the distribution? Well, the answer is NO! The silicon value is only one point on the distribution curve of all of the silicon values in the heat. Since you cannot say for certain what this mill test report actually represents you make the deadly assumption the silicon value is somewhere around the middle of the distribution. This is good statistics until your part comes out with a dull gray and thick coating and your customer is not very happy!
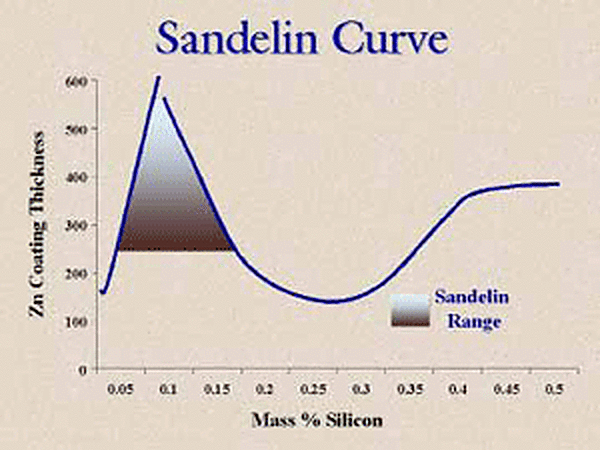
So, what happened to our galvanized coating and why does the part have a thick coating? The answer lies in the Sandelin curve (Figure 1).
Pay particular attention to the slope of the curve around 0.05% silicon content. The slope is very steep, so meaning a small change in the silicon content will result in a large change in the coating thickness. Therefore, if you have a part where the mill test report gives a value of 0.04% silicon and this silicon value is in the center of the steel heat silicon distribution or on the high side of the distribution, the galvanized coating will come out bright and shiny and right on specification coating thickness. On the other hand, if the 0.04% on the mill test report is on the very low side of the distribution, then some parts from this steel heat will have higher silicon values and will yield galvanized coatings that may be much thicker and even dull gray in appearance. The small difference between a silicon value of 0.04% and 0.06% can make a big difference in the galvanized coating thickness and appearance. The two micrographs below (Figures 2 and 3) show the difference in the coating structure with just a little change in the silicon content. The first micrograph has a structure of three intermetallic layers and a free zinc layer as the outer layer. The second micrograph has very small gamma and delta layers and a very large zeta layer with no free zinc layer so it will have a dull gray appearance.
The recommended limits (below 0.04% or between 0.15% and 0.22%) for silicon content are given in ASTM A385. However, there will be times when silicon levels are within these limits yet the coating comes out with a dull gray appearance and a thick galvanized coating. One of the ways to lower the chance of this happening is to use a kettle chemistry that contains nickel.
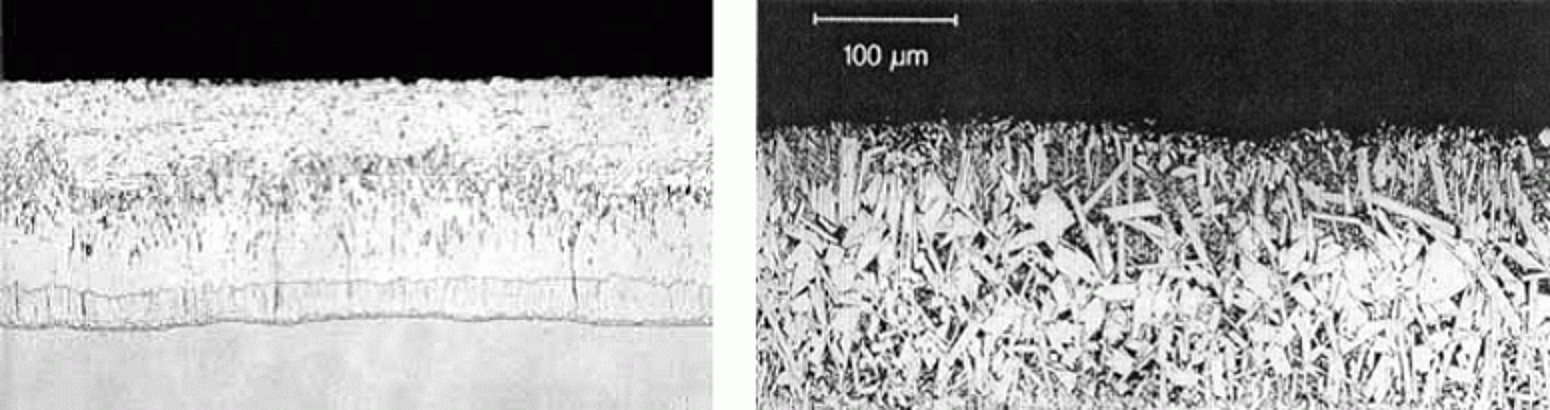
Nickel in the zinc bath reduces the effect of the silicon content for all silicon values below about 0.20% and helps maintain low coating thicknesses and bright and shiny appearances. The negative to using nickel is the coating thickness will be reduced for steels with very low silicon contents, to the point the coating thicknesses for certain products may not meet the minimum values in ASTM A123. This may happen on some tubular products and on very thin plate materials. One remedy to this issue is to blast clean the low silicon steel so the coating will form on a rougher surface which gives a thicker coating that will meet the specifications minimums.
So, if you have to tell your customer the steel he purchased with the ideal silicon content may not be perfect after all, dont forget to follow up with the fact the lifetime of the galvanized coating is directly proportional to the coating thickness, and all galvanized coatings will be dull gray in about a year as the zinc patina is formed on the surface. It may not appease him, but it does provide a silver lining.
© 2025 American Galvanizers Association. The material provided herein has been developed to provide accurate and authoritative information about after-fabrication hot-dip galvanized steel. This material provides general information only and is not intended as a substitute for competent professional examination and verification as to suitability and applicability. The information provided herein is not intended as a representation or warranty on the part of the AGA. Anyone making use of this information assumes all liability arising from such use.