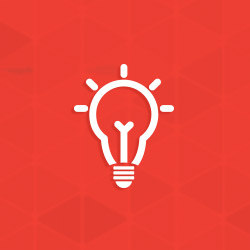
G185 Coating and Pressure-Treated Wood
Note: Have questions about continuous hot-dip galvanizing? Contact the GalvInfo Center
My customers are asking for a G185 equivalent coating on some steel hardware to be used to fasten steel into the treated wood, it has something to do with new chemicals that are being used to pressure-treat wood. Are my coatings thick enough to qualify as a G185 coating and provide long-term protection for this application? And whats up with the switch in chemicals for pressure-treated wood?
Lets begin with a brief discussion on the changes to the preservative-treated wood industry. Recently, the preservative-treated wood industry voluntarily transitioned away from the use of chromated copper arsenate (CCA) for use in pressure treating wood for residential applications. CCA-treated wood will still be used in industrial applications, but new chemicals will replace CCA in residential applications. The new chemicals that are being used to treat wood are alkaline copper quat (ACQ), copper azole (CBA-A & CAB), and sodium borates (SBX).
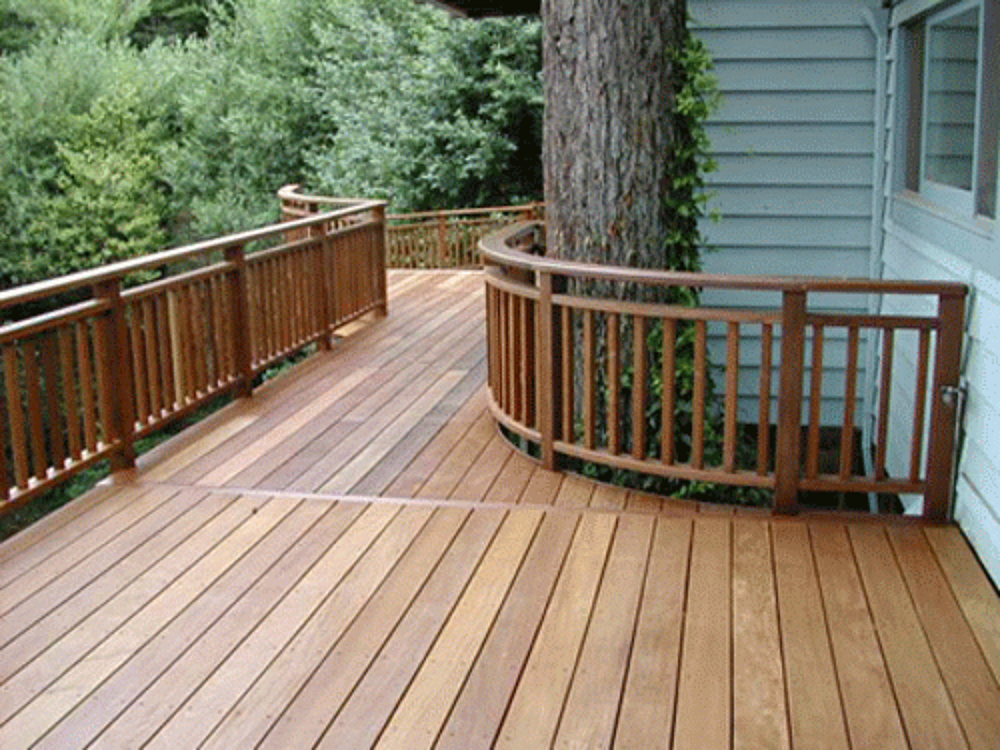
There have been some concerns with the corrosiveness of these new chemicals to steel coatings because treated wood and coated steel are often used in conjunction with one another. One company, Simpson Strong Tie, has completed some initial accelerated orrosion tests on the corrosiveness of these chemicals when in contact with galvanized sheet products.
The chart, below, shows the results of their study (for the full report, visit http://www.strongtie.com/ftp/bulletins.
Corrosion of Galvanized Steel in Contact with Pressure-Treated Lumber
Chemical Name | Abbreviation | Trade Name | Relative Corrosion Rate |
---|---|---|---|
Sodium borates | SBX2 | Advance Guard® | 0.6 |
Chomated Copper Arsenate | CCA | Wolmanized® | 1 |
Alkaline Copper Quat | ACQ | Preserve and NatureWood® | >2.0 |
Copper Azole | CBA-A & CA-B | Wolmanized® Natural Select™ | >2.0 |
Ammoniacal Copper Zinc Arsenate | ACZA | CHEMONITE® | 3.0 |
Notes: 1. CCA-C, ACQ-D (Carbonate), CA-B, SBX (DOT) were used in the study that determined relative rates. 2. SBX treated woods are not suitable for applications where moisture exposure is likely |
As you can see from the chart, three of the new chemicals are at least twice as corrosive as the old wood treatment CCA (although SBX has a lower relative corrosion rate, it has limited applications). Therefore, it has been recommended to end-users that twice as much zinc be used on galvanized parts for increased corrosion protection.
Originally for sheet products, a G90 coating was required for galvanized steel in contact with treated wood. To combat the increased corrosion rate, the recommendation has been changed to a G185 coating. The G185 coating corresponds to a zinc coating weight of 1.85 oz/ft2 In terms of coating thickness this translates to 1.56 mils (40 m) of zinc on each side. According to ASTM A123 and A153, the minimum zinc thickness for hot-dip galvanized steel that would be used in this application exceeds a G185 coating (excluding wire that is less than 1/16" in diameter). Therefore, essentially all after-fabrication hot-dip galvanized steel will meet the new recommendations for zinc coating thickness to overcome the increased corrosiveness of the pressure treated wood chemicals.
The pressure-treated wood industry has recommended the use of hot-dipped galvanized or stainless steel fasteners, anchors, and hardware for use with these new types of wood treatments. If your customers ask about the use of galvanized steel and treated wood, you can tell them that hot-dip galvanized steel is a recommended coating and that after-fabrication hot-dip galvanized steel will give them a long life when used with the new-age treated lumber.
© 2025 American Galvanizers Association. The material provided herein has been developed to provide accurate and authoritative information about after-fabrication hot-dip galvanized steel. This material provides general information only and is not intended as a substitute for competent professional examination and verification as to suitability and applicability. The information provided herein is not intended as a representation or warranty on the part of the AGA. Anyone making use of this information assumes all liability arising from such use.