U-Z
Weeping Weld
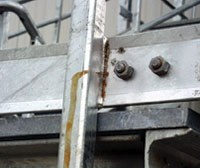
Weeping welds stain the zinc surface at the welded connections on the steel caused by entrapped cleaning solutions that penetrate the incomplete weld. In order to avoid weeping welds for small overlapping surfaces, completely seal weld the edges of the overlapping area. For larger overlapping areas, the area cannot be seal welded since the volume expansion of air in the trapped area can cause explosions in the galvanizing kettle. To avoid weeping welds in large overlapping areas, the best plan is to provide a 3/32 in (2.4 mm) or larger gap between the two pieces when welding them and let the zinc fill the gap between the pieces. This will actually make a stronger joint when the process is complete. Weeping welds (Figure 48) are not the responsibility of the galvanizer and are not cause for rejection.
Welding Blowouts
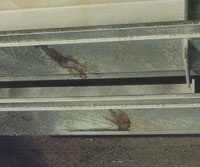
Welding blowout is a bare spot around a weld or overlapping surface hole caused by pre-treatment liquids penetrating the sealed and overlapped areas that boil out during immersion in the liquid zinc. Blowouts cause localized surface contamination and prevent the galvanized coating from forming. To avoid welding blowouts (Figure 49), check weld areas for complete welds to ensure there is no fluid penetration. In addition, products can be preheated prior to immersion into the galvanizing kettle in order to dry out overlap areas as much as possible. Welding blowouts cause bare areas that must be repaired before the part is acceptable.
Welding Spatter
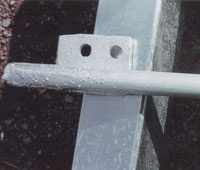
Welding spatter appears as lumps in the galvanized coating adjacent to weld areas. It is created when welding spatter is left on the surface of the part before it is hot-dip galvanized. In order to avoid welding spatter, welding residues should be removed prior to hot-dip galvanizing. Welding spatter (Figure 50) appears to be covered by the zinc coating, but the coating does not adhere well and can be easily removed leaving an uncoated area or bare spot. If this defect occurs, the area must be cleaned and properly repaired, which may require regalvanizing.
Wet Storage Stain
Wet storage stain is a white, powdery surface deposit on freshly galvanized surfaces. It can occur when newly galvanized surfaces are exposed to fresh water, such as rain, dew, or condensation and have no air flow over the surface causing zinc oxide and zinc hydroxide to form. Wet storage stain is found most often on tightly stacked and bundled items, such as galvanized sheets, plates, angles, bars, and pipes. Wet storage stain can have the appearance of light, medium, or heavy white powder on the galvanized steel product (Figure 51).
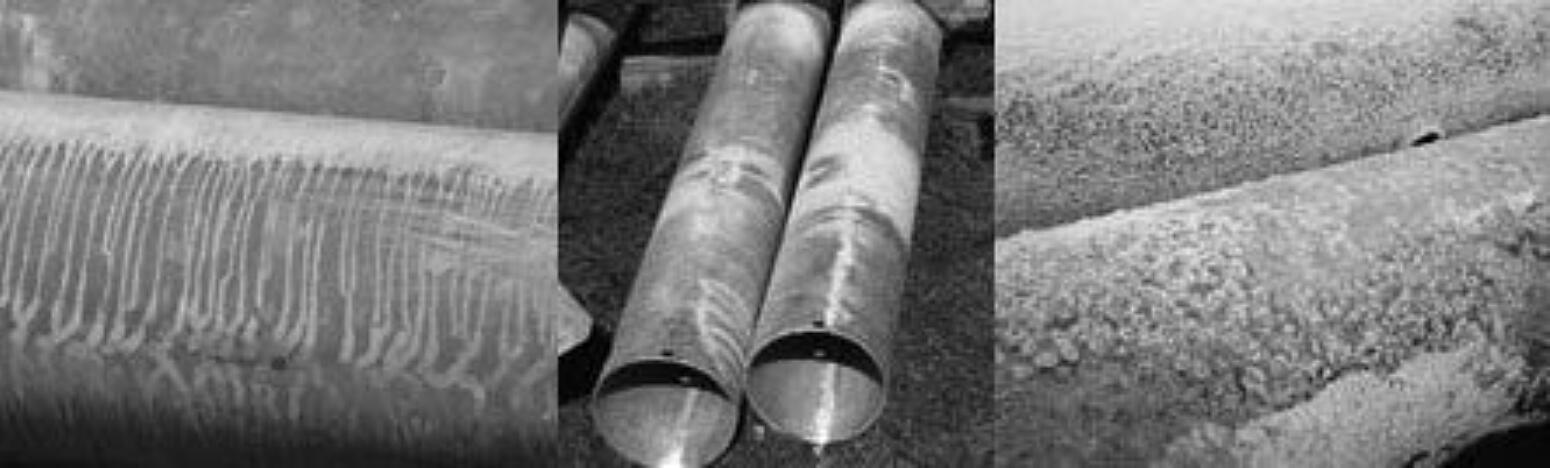
One method to avoid wet storage stains is to passivate the product after galvanizing by using a chromate quench solution. Another precaution is to avoid stacking products in poorly ventilated, damp conditions. Light or medium wet storage stain will weather over time in service and is acceptable. In most cases, wet storage stain does not indicate serious degradation of the zinc coating, nor does it necessarily imply any likely reduction in the expected life of the product. However, heavy wet storage stain should be removed mechanically or with appropriate chemical treatments before the galvanized part is put into service. Heavy storage stain must be removed or the part must be rejected and regalvanized.
The galvanizer is responsible for following best practices for avoiding wet storage stain on parts stored at the galvanizing facility. When those best practices are followed, the galvanizer is not responsible for wet storage stain developed at his facility, during transit, or storage at the job site prior to use. For more information on avoiding and/or removing wet storage stain, please see the AGA's publication Wet Storage Stain.
Zinc Skimmings
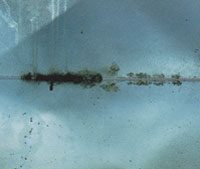
Skimming deposits are usually caused when there is no access to remove zinc skimmings during the withdrawal of the steel from the galvanizing kettle. Zinc skimmings on the molten surface are then trapped on the zinc coating. To remove zinc skimmings without harming the soft zinc coating underneath, lightly brush them off the surface of the galvanized steel during the in-house inspection stage with a nylon-bristle brush. Zinc skimmings (Figure 52) are not grounds for rejection as long as the zinc coating underneath is not harmed during their removal and it meets the necessary specifications.
Zinc Splatter
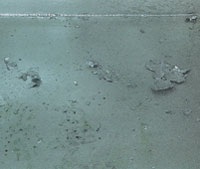
Zinc splatter is defined as splashes and flakes of zinc that loosely adhere to the galvanized coating surface. Zinc splatter is created when moisture on the surface of the galvanizing kettle causes liquid zinc to "pop" and splash droplets onto the product. These splashes create flakes of zinc loosely adherent to the galvanized surface. Zinc splatter (Figure 53) will not affect the corrosion performance of the zinc coating and thus is not cause for rejection. The splatter does not need to be cleaned off the zinc coating surface, but can be if a consistent, smooth coating is required.