Repair
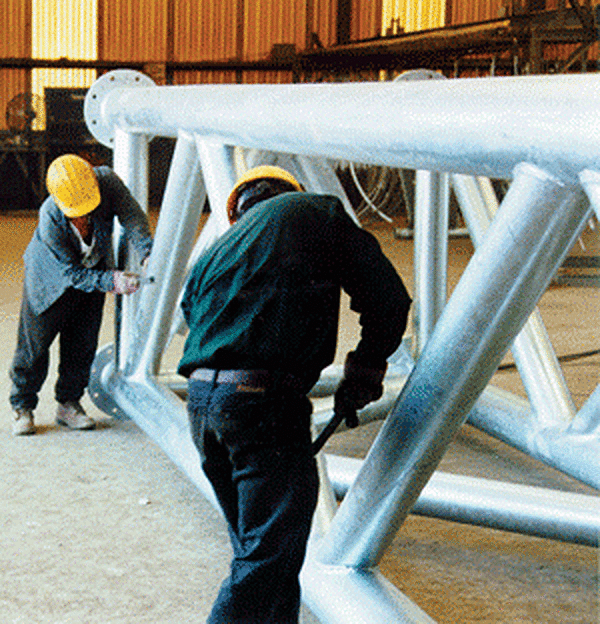
If the galvanized product does not meet all of the requirements of the specification, it must be repaired or rejected along with the lot it represents. When repair of the product is allowed by the specification or bare spots are present, the galvanizer is responsible for the repair unless directed otherwise by the purchaser. The specifications allow for some retesting of products that represent lots or retesting after the lot has been sorted for non-conformance.
The AGA has an online video series for Touch-Up and Repair of Hot-Dip Galvanized Steel. Six short videos detail the many aspects to consider when touching up or repairing HDG steel.
The coating thickness of the repaired area must match the coating thickness of the surrounding area. However, if zinc-rich paint is used for repair, the coating thickness must be 50% higher than the surrounding area, but not greater than 4.0 mils because mud cracking tends to result when the paint coating is too thick. The maximum sizes for allowable areas that can be repaired during in-plant production are defined in the specifications as summarized below.
Maximum Size of Repairable Area at Galvanizing Plant
-
ASTM A 123/A 123M:
- Bare spot(s) shall not exceed 1 inch in the narrowest dimension
- And the total bare spot(s) can be no more than 0.5% of the accessible surface area to be coated or 36 square inches per piece, whichever is less
-
ASTM A 153/A 153M:
- Bare spots shall have an area totaling no more than 1% of the total surface area to be coated, excluding threaded areas of the piece
-
ASTM A 767/A 767M:
- Bare spot(s) shall not exceed 1% of the total surface area in each 1ft [0.3m] length of the bar.
- If the coating fails to meet the requirement for finish and adherence, the bar may be stripped, regalvanized, and resubmitted
- Damage done to the coating due to fabrication or handling shall be repaired with a zinc-rich formulation
- Sheared ends shall be coated with a zinc-rich formulation
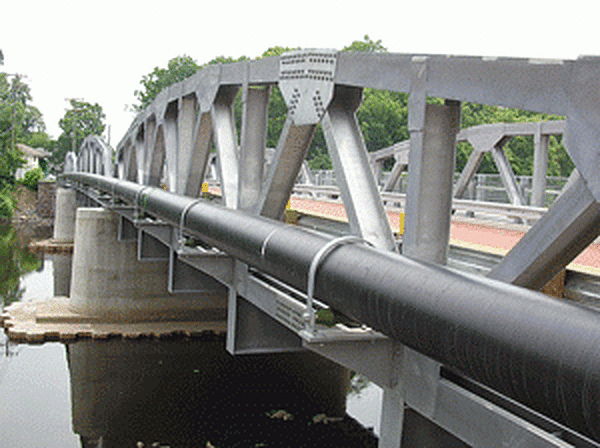
Field Repair
The zinc coating of hot-dip galvanized steel is difficult to damage, and field fabrication that requires removal of the coating should be minimized as much as possible. However, sometimes due to improper handling or abrasion after years in service, small voids are found in the coating. To maintain uniform barrier and cathodic protection and ensure longevity, it is best practice to touch-up and repair the coating. When it comes to touching-up galvanized steel in the field, there is no limitation to the size that can be repaired.
Repair Methods
Any repairs made to galvanized products must follow the requirements of ASTM A780 Practice for Repair of Damaged and Uncoated Areas of Hot-Dip Galvanized Coatings, which defines the acceptable materials and the required procedures. Repairs are normally completed by the galvanizer before the products are delivered, but under certain circumstances, the purchaser may perform the repairs on their own. The touch-up and repair materials are formulated to deliver similar colors to brightly coated, newly galvanized products or matte gray, aged galvanized products. Materials used to repair hot-dip galvanized products include zinc-based solder, zinc-rich paint, and zinc spray metallizing, and are explained in the following sections.