F-O
Fish Boning
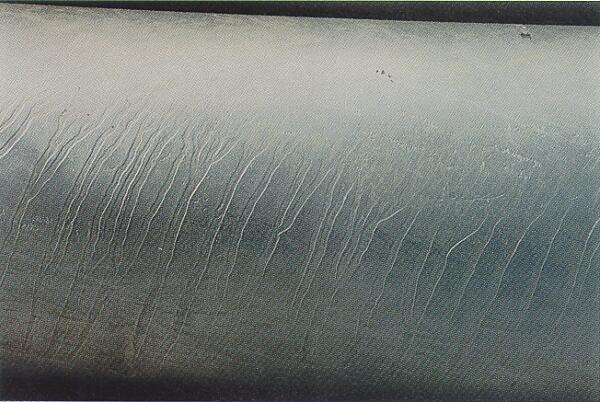
Fish boning is an irregular pattern over the entire surface of the steel part. This is caused by differences in the surface chemistry of a large diameter steel piece and variations in the reaction rate between the iron in the steel and the molten zinc. These reaction differences cause the thickness of the galvanized coating to vary in sharply defined zones across the surface. Fish boning (Figure 34) has no effect on the corrosion protection provided by the zinc coating and is not cause for rejection of the hot-dip galvanized part.
Flaking
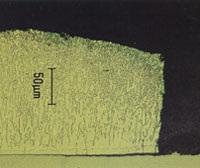
Flaking results when heavy coatings develop in the galvanizing process, usually 12 mils or greater. Excessively thick coatings generate high stresses at the interface of the steel and the galvanized coating which causes the zinc to become flaky and separate from the steel surface. Flaking can be avoided by minimizing the immersion time in the galvanizing kettle and cooling of the galvanized steel parts as quickly as possible and/or if possible using a different steel grade. Figure 35 shows a micrograph of flaking as well as a galvanized part with flaking coating. In addition, using a different steel grade, if possible, may also help avoid flaking. If the area of flaking is small, it can be repaired and the part can be accepted; however, if the area of flaking is larger than allowed by the specifications, the part must be rejected and regalvanized.
Flux Inclusions
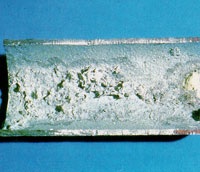
Flux inclusion can be created by the failure of the flux to release during the hot-dip galvanizing process, preventing the coating from forming under the flux spot. Because no coating grows under the inclusion, the area must be repaired prior to acceptance. If the area is small enough, it can be cleaned and repaired; otherwise, the part must be rejected. Flux deposits on the interior of a hollow part, such as a pipe or tube (Figure 36) cannot be repaired, thus the part must be rejected. The potential for flux spots can increase if the flux is applied using the wet galvanizing method, which is when the flux floats on the zinc bath surface. Any flux spots or deposits picked up during withdrawal from the galvanizing kettle do not warrant rejection if the underlying coating is not harmed, and the flux is properly removed.
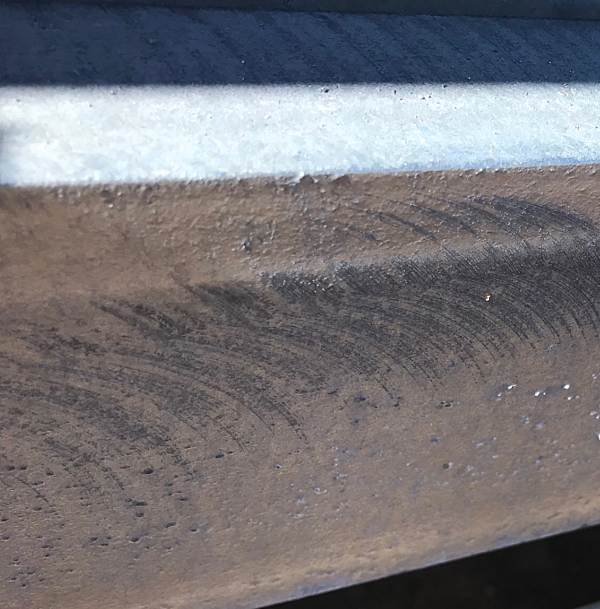
Grinder Marks
Grinders are often used to remove unacceptable surface conditions such as drainage spikes, or lumps which affect the intended use of the product. Occasionally, visible marks may remain upon remediation of these areas. These marks left on the surface after grinding are purely cosmetic and do not affect the corrosion protection performance of the coating. Grinder marks are acceptable provided excessive grinding or thinning of the coating is avoided.
.
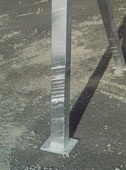
Oxide Lines
Oxide lines are light colored film lines on the galvanized steel surface created when a product is not withdrawn from the galvanizing kettle at a constant rate (Figure 38). This may be due to the shape of the product or the drainage conditions. Oxide lines will fade over time as the entire zinc surface oxidizes (weathers). Strictly an aesthetic condition, oxide lines have no effect on the corrosion performance; and therefore, are not a cause for rejection of the hot-dip galvanized parts.