P-R
Products in Contact
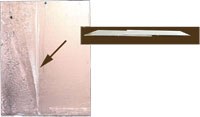
Another type of surface condition can occur if steel products come in contact with one another or are stuck together during the galvanizing process. This can occur when many small products are hung on the same fixture, creating the chance products may become connected or overlapped during the galvanizing process (Figure 39). The galvanizer is responsible for proper handling of all products to avoid defects from products in contact. If this causes the surface area of a product to have a larger bare area than can be repaired according to the specification, then the product must be stripped and regalvanized.
Rough Surface Condition
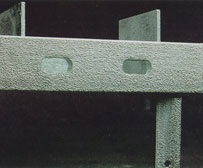
Rough surface condition or appearance is a uniformly textured appearance over the entire product (Figure 40). The cause for rough surface condition could be the steel chemistry or the preparation of the surface by mechanical cleaning such as blasting before the part is delivered to the galvanizer. Rough surface condition may be avoided by purchasing steel with a silicon content less than 0.03% of the steel by weight. However, the rough surface condition can actually have a positive effect on corrosion performance because of the thicker zinc coating produced. One of the few situations where rough coating is cause for rejection is if it occurs on handrails as it impacts the intended use of the product. On other products, it is not cause for rejection because the corrosion performance of galvanized steel is not compromised.
Runs
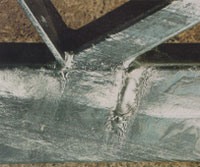
Runs are localized thick areas of zinc on the surface that occur when zinc freezes on the surface of the product during removal from the zinc bath. This is more likely to occur on thinner sections with large surface areas that cool quickly. In order to avoid runs (Figure 41), adjustments of the dipping angles can be made, if possible, to alter the drainage pattern to be more effective. Runs are not cause for rejection unless they affect the intended use of the steel part. If runs are unavoidable due to the design of the product, but will interfere with the intended application, they can be buffed.
Rust Bleeding
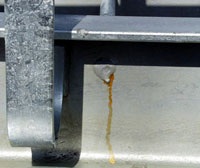
Rust bleeding appears as a brown or red stain that leaks from unsealed joints after the product has been hot-dip galvanized (Figure 42). Bleeding is caused by pre-treatment chemicals that penetrate an unsealed joint. During galvanizing of the product, moisture boils off the trapped treatment chemicals leaving anhydrous crystal residues in the joint. Over time, these crystal residues absorb water from the atmosphere and attack the steel on both surfaces of the joint, creating rust that seeps out of the joint. Rust bleeding can be avoided by seal welding the joint where possible or by leaving a gap greater than 3/32 in (2.4 mm) wide to allow solutions to escape and zinc to penetrate during hot-dip galvanizing. If bleeding occurs, it can be cleaned by washing the joint after the crystals are hydrolyzed. Bleeding from unsealed joints is not the responsibility of the galvanizers and is not cause for rejection.