Zinc-Based Solder
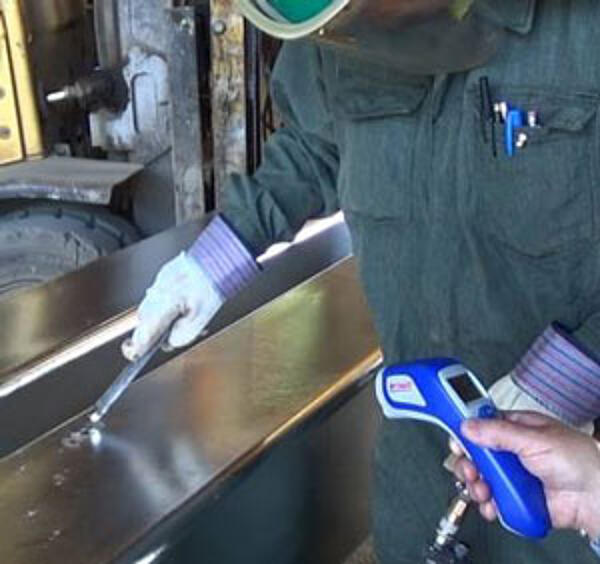
Soldering with zinc-based alloys is achieved by applying zinc alloy in either a stick or powder form. The area being repaired needs to be preheated to approximately 600 F (315 C). The most commonly used solders for repair (Figure 55) include zinc-tin-lead, zinc-cadmium, and zinc-tin-copper alloys.
Surface Preparation
According to ASTM A780, the surface to be reconditioned shall be wire brushed, lightly ground, or mildly blast cleaned. This surface preparation shall extend into the surrounding, undamaged galvanized coating to ensure a smooth repair and good adhesion. The cleaned area also needs be preheated to 600 F (315 C) and wire brushed while heated. Pre-flux may also be necessary to provide chemical cleaning of the bare spot. Finally, special care should be given to insure that the surrounding galvanized coating is not overheated and burned by the preheating.
Application
The soldering method is the most difficult of the three repair methods to complete. A high level of caution must be taken while heating the bare spot to prevent oxidizing the exposed steel or damaging the surrounding galvanized coating. Solders are typically not economically suited for touch-up of large areas because of the time involved in the process and because heating of a large surface area to the same temperature is very difficult. When the repair has been completed, the flux residue needs to be removed by rinsing the surface with water or wiping with a damp cloth.
Final Repaired Product
The final coating thickness for this repair must meet the specification requirement for the material category and thickness range of the steel part being repaired. The thickness should be measured by any of the methods in A123/A123M that are non-destructive. Zinc-based solder products closely match the surrounding zinc and blend in well with the existing coating appearance.