A-C
Bare Spots
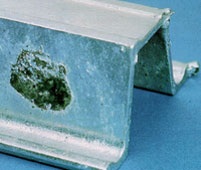
Bare spots, or uncoated areas on the steel surface, are the most common surface defect and occur because of inadequate surface preparation, welding slag, sand embedded in castings, excess aluminum in the galvanizing kettle, or lifting aids that prevent the coating from forming in a small area. Only very small areas, less than 1 inch in the narrowest dimension with a total of no more than 0.5%of the accessible surface area, may be renovated using ASTM A780. This means narrow, bare areas may be repaired; however, if they are greater than one inch-square areas, the product must be regalvanized. In order to avoid bare spots, (Figure 24), the galvanizer must ensure the surfaces are clean and no contaminants or rust are present after pretreatment. If the size of the bare spot or total surface area causes rejection, the parts may be stripped, regalvanized, and then re-inspected for compliance to the specifications.
Blasting Damage
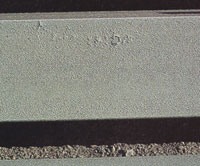
Blasting damage creates blistered or flaking areas on the surface of the galvanized product. Blasting damage follows abrasive blasting prior to painting of the galvanized steel. It is caused by incorrect blasting procedures creating shattering and delamination of the alloy layers in the zinc coating. Blasting damage, (Figure 25), can be avoided when careful attention is paid to preparation of the product for painting. In addition, blast pressure should be greatly reduced according to ASTM D6386 Practice for Preparation of Zinc (Hot-Dip Galvanized) Coated Iron and Steel Product and Hardware Surfaces for Paint. More information about proper surface preparation of hot-dip galvanized steel for painting can be found in the American Galvanizers Association's (AGA's) Preparing Hot-Dip Galvanized Steel for Paint instructional DVD and guide booklet. Since blasting damage is induced by a post-galvanizing process, the galvanizer is not responsible for the damage.
Chain and Wire Marks
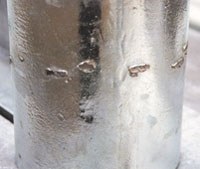
Another type of surface defect occurs when steel is lifted and transported around the galvanizing plant using a chain or wire. These lifting aids can leave uncoated areas on the finished product that will need to be repaired. The superficial marks (Figure 26) left on the galvanized coating from the lifting attachments are not grounds for rejection unless the marks expose bare steel; in such a case, the galvanizer must repair the bare areas before the part is acceptable as the ASTM specifications do not allow any bare spots on the finished galvanized part. One potential way to avoid these types of marks is to design permanent or temporary lifting points in the fabrication.
Clogged Holes
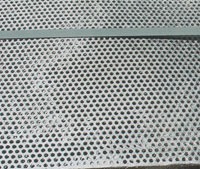
Clogged holes are caused by molten zinc metal not draining adequately and partially or completely filling holes. Molten zinc will not drain easily from holes less than 3/32 in (3 mm) in diameter due to the viscosity of zinc metal. The screen in Figure 27 is a good example of this issue. Clogged holes can be minimized by making holes as large as possible. Trapped zinc can be removed by using active fettling when the part is in the galvanizing kettle, vibrating the cranes to jostle the parts, or blowing compressed air into the galvanized parts. Clogged holes less than 1/2 in (12.7 mm) in diameter are not cause for rejection, unless it prevents the part from being used for its intended purpose.
Clogged Threads
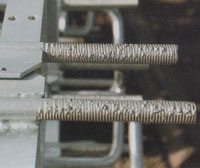
Similarly, clogged threads are caused by poor drainage of a threaded section after the product is withdrawn from the galvanizing kettle. Clogged threads (Figure 28) can be cleaned using post-galvanizing cleaning operations such as a centrifuge or by heating them with a torch to about 500 F (260 C) and then brushing them off with a wire brush to remove the excess zinc. Clogged threads must be cleaned and free of excess zinc before the part can be accepted.