Process Temperature
During the hot-dip galvanizing process, steel is heated to approximately 830 F (443 C) for the galvanizing reaction to occur. Every time steel is heated and cooled, stress is added to the fabrication. Hot-dip galvanizing does NOT change the mechanical properties of the steel, but there are certain design practices that should be followed to reduce any issues with the heating of the galvanizing process.
Mechanical Properties
The hot-dip galvanizing process produces no significant changes in the mechanical properties of the structural steels commonly galvanized throughout the world. The International Zinc Association (IZA) sponsored a four-year research study of the mechanical properties of 19 structural steels from major industrial countries. The University of Plymouth Enterprise Ltd. investigated the steels, including those conforming to ASTM Specifications A36, A572 Grade 50, and A572 Grade 65.
HDG temperature does not change:
- Steel chemistry
- Tensile strength
- Yield strength
- Bend properties
- Impact properties
- Micro-structure
Further industry research also confirms this finding, and all of these studies are available by contacting the AGA Technical Department.
Cold Working Steel
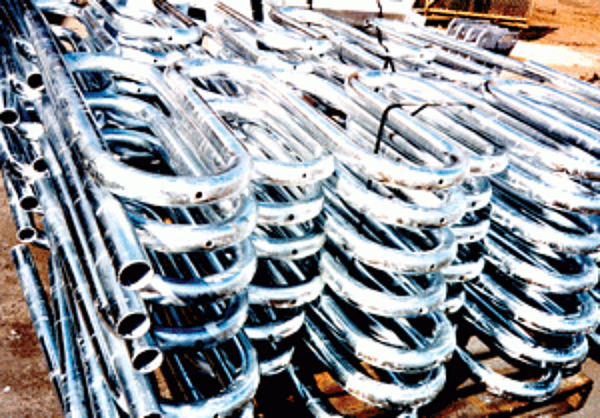
Many structures and parts are fabricated using cold-rolled steel or cold-working techniques. In some instances, severe cold-working may lead to the steel becoming strain-age embrittled. While cold working increases the possibility of strain-age embrittlement, it may not be evident until after galvanizing. This occurs because aging is relatively slow at ambient temperatures, but more rapid at the elevated temperature of the galvanizing bath. Any form of cold-working reduces steels ductility. Operations such as punching holes, notching, producing fillets of small radii, shearing, or sharp bending may lead to strain-age embrittlement of susceptible steels. Cold-worked steels less than 1/8" (3 mm) thick that are subsequently galvanized are unlikely to experience strain-age embrittlement. Cold working is the strongest contributing factor to the embrittlement of galvanized steel.
Tips to Reduce Strain-Age Embrittlement:
- Select steels with carbon contents below 0.25%.
- Choose steels with low transition temperatures since cold-working raises the ductile-brittle transition temperature and galvanizing (heating) may raise it further.
- Specify aluminum-killed steels; they show less susceptibility to strain-age embrittlement.
- For steels with a carbon content between 0.1% and 0.25%, maintain a bending radius of at least three times (3x) the section thickness. If bending is required to be less than 3x, the material should be stress-relieved at 1100 F (595 C) for one hour per inch (2.5 cm) of section thickness.
- Avoid notches they increase stress. Notches may be caused during shearing or punching operations. Flame-cutting or sawing is preferred, particularly for heavy sections.
- Drill, rather than punch, holes in material thicker than 3/4-inch (19 mm). If holes are punched, they should be punched undersize and then reamed an additional 1/8" (3 mm) overall or drilled to size. Material between 1/4 - 3/4" (6.5 - 19 mm) thick is not seriously affected by cold punching if the punching is done under good shop practice. Material up to 1/4" (6.5 mm) thick that has been cold-worked by punching does not need stress-relieving before galvanizing.
- For steel sections with edges greater than 5/8-inch (16 mm) thick subject to tensile loads, cut using normal shop procedures. Edges of sections up to 5/8" (16 mm) thick may be cut by shearing.
- In critical applications, the steel should be hot-worked above 1200 F (650 C) in accordance with the steel manufacturers recommendations. Where cold-working cannot be avoided, stress-relieve the part.
ASTM A143, Safeguarding Against Embrittlement of Hot-Dip Galvanized Structural Steel Products and Procedure for Detecting Embrittlement, and CSA Specification G164, Hot-Dip Galvanizing of Irregularly Shaped Articles, provide guidance on cold-working and stress-relieving procedures. However, it is best to avoid severe cold-working of susceptible steels. If there is concern with possible loss of ductility due to strain-age embrittlement, advise your galvanizer. A sample quantity of the cold-formed items should be galvanized and tested before further commitment.
Hydrogen Embrittlement
Hydrogen embrittlement is a ductile to brittle change that occurs in certain high-strength steels. Hydrogen embrittlement can occur when the hydrogen released during the pickling process is absorbed by the steel and becomes trapped in the grain boundaries. Normally, at galvanizing temperatures, hydrogen is expelled from the steel. Although hydrogen embrittlement is uncommon, precautions should be taken to avoid it, particularly if the steel involved has an ultimate tensile strength exceeding 170,000 psi (1200 MPa). If high-strength steels are to be processed, grit- blasting instead of acid-pickling is recommended in order to minimize the introduction of gaseous hydrogen during the pickling process.
Cope Cuts
Flame cut copes on beams can be extremely sensitive to residual stresses in the steel and the surface of the cut can be rough. Both of these factors can contribute to cracks forming in the cut edges. The potential for cracking can be significantly reduced by thermal conditioning the cut edge. Weld bead should be applied in the highlighted area on both sides of the copes. A simple technique for accomplishing this is to apply a weld bead along the cut edge, thereby reducing residual stresses and avoiding cracking.
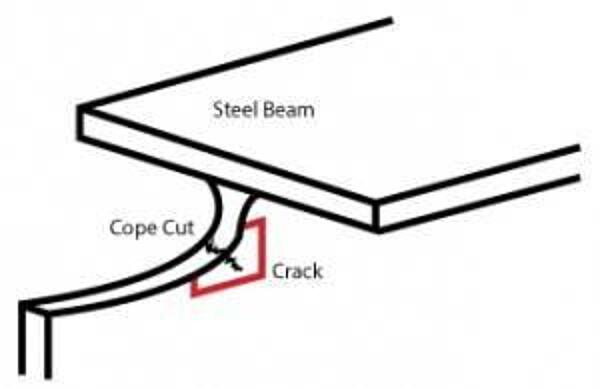
There is still a small potential for cracking on these cut edges as well as on the corners of HSS rectangular tubing. The two areas should be visually inspected after galvanizing to detect the presence of any cracks. Any cracks can be repaired by removing steel around the crack, filling the area with weld material, smoothing the weld and then applying a zinc coating per ASTM A780 Practice for Repair of Damaged and Uncoated Areas of Hot-Dip Galvanized Coatings before the steel is delivered.
Heating and Cooling Rates
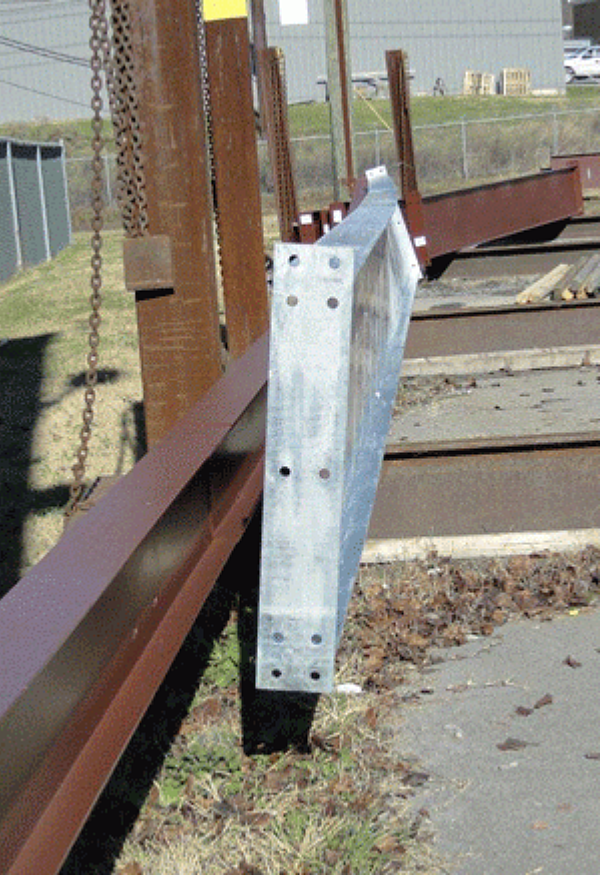
Steel that is being galvanized is exposed to a wide temperature range from ambient to 850 F. Because parts are immersed at an angle, uneven heating and cooling occur. This exposure to temperature variations allows the steels internal stresses to be relieved at different times. Some fabricated assemblies may distort at galvanizing temperature as a result of relieving stresses induced during steel production and in subsequent fabricating operations. For example, a channel frame with a plate should be galvanized separately and bolted later rather than welded together before galvanizing, or it can be welded after galvanizing. Guidelines for minimizing distortion and warpage are provided in ASTM A384, Safeguarding Against Warpage and Distortion During Hot-Dip Galvanizing of Steel Assemblies, and CSA SpecificationG164, Hot Dip Galvanizing of Irregularly Shaped Articles.
Tips for Minimizing Distortion
The best way to prevent warpage and distortion is to follow the recommended design practices within ASTM A384 and to facilitate communication between the galvanizer, designer, and fabricator early in the design process to ensure induces stresses from design and fabrication are minimized where possible.
Other methods to minimize the potential for warpage and distortion are to:
- Avoid susceptible designs which are thin and asymmetrical (less than 1/4" or 20 gauge). Where possible, use symmetrically rolled sections in preference to angle or channel frames. I-beams are preferred to angles or channels.
- Use parts in an assembly of equal or near equal thickness, especially at joints.
- Avoid designs that require progressive-dip galvanizing. It is preferable to build assemblies and subassemblies in suitable modules so they can be immersed quickly and galvanized in a single dip. In this way, the entire fabrication can expand and contract uniformly. Where progressive dipping is required, consult your galvanizer.
Asymmetrical Designs
- Specify symmetrically rolled sections instead of angle or channel frames.
- Assemble two asymmetrical sections back-to-back using temporary bracing and spacers to create a symmetrical section.
- Install temporary bracings for curved plates, channel frames, and troughs which are proportional to plate thickness; located at quarter points of product height.
- Tees should be dipped flange-side first while channels should be dipped web-side first.
- Perform immersion as quick as possible and at the largest possible dip angle.
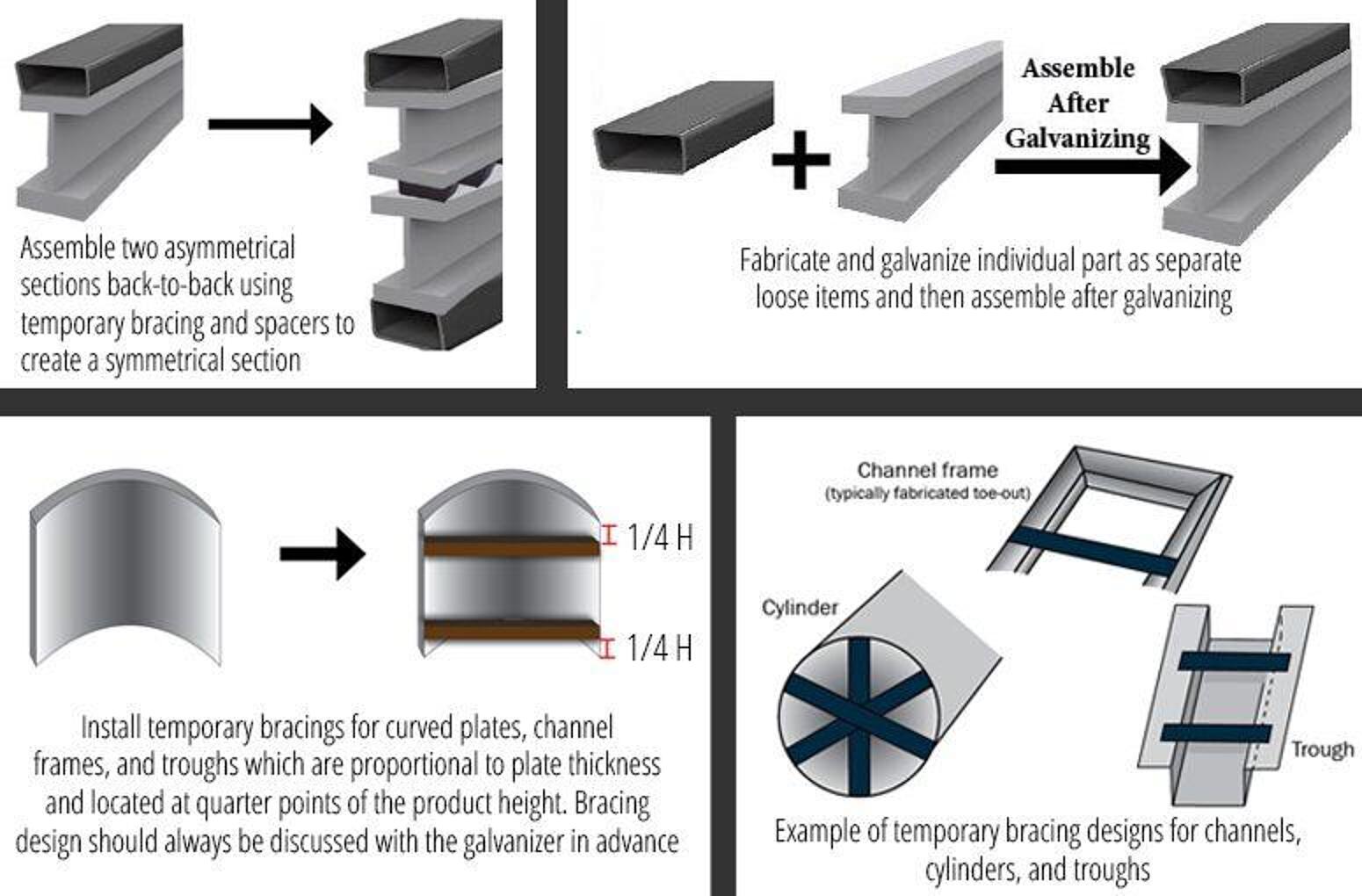
Thin and Thick Material Within Assembly
- Steel thicknesses should vary as little as possible throughout the assembly.
- Add stiffeners to the design of structures containing unsupported flat sheets.
- Flange-to-web thickness of fabricated beams should be no more than 3 to 1.
- Galvanize thick and thin portions separately and join them after galvanizing.
- Perform immersion as quick as possible and at the largest possible dip angle.
Progressive Dipping
- Consult with the galvanizer to take into account length variations of the assembly and plan for thermal expansion conditions.
Poor Drainage/Venting and Lifting Points
- Lift points for galvanizing should be located at quarter points along the product length.
- Design drainage/venting holes per ASTM A385 and maximize drainage for hollow sections.
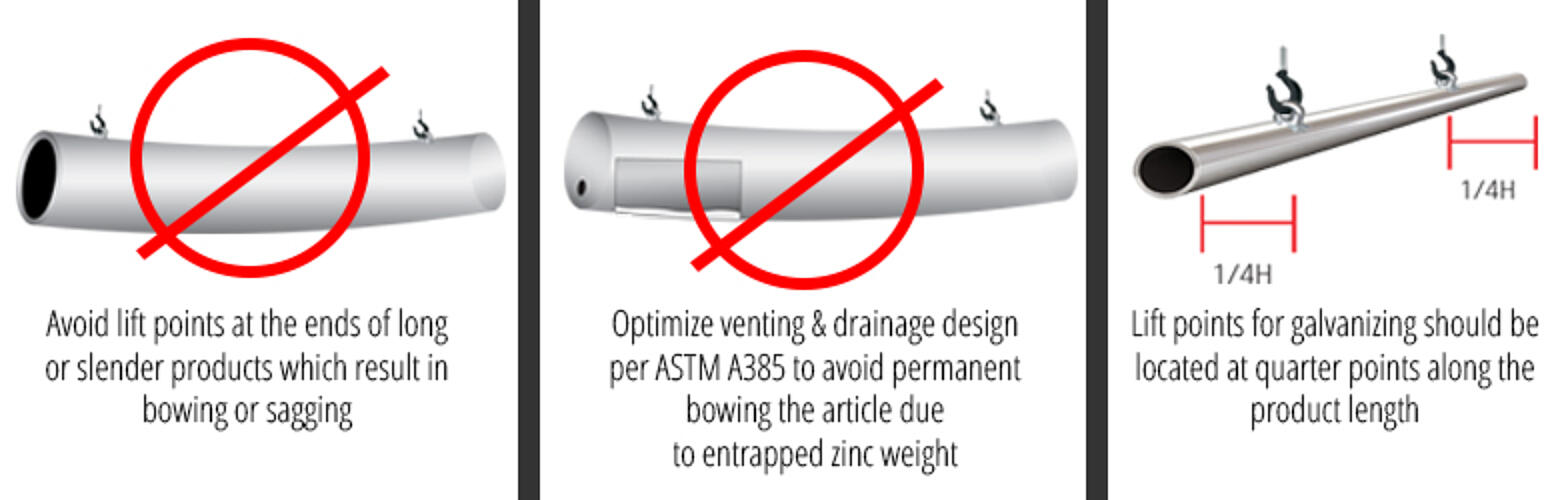
There are also some process controls which can be performed by the galvanizer, such as performing a quick immersion in the kettle and allowing parts to air cool, but these controls have a limited effect on minimizing warpage and distortion.