In Moisture-Rich Environments
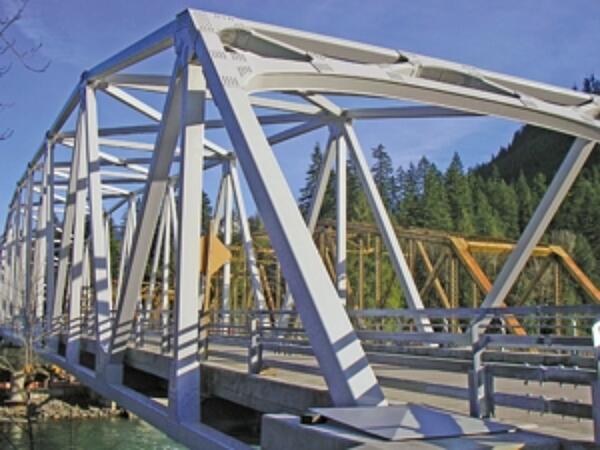
A less common environment for steel in the transportation sector is submerged in or exposed to water. Moisture is highly corrosive to most metals including steel and zinc. However, because of the development of the passive, mostly non-water soluble zinc patina, the corrosion rate of galvanized steel is much slower than bare steel. There are many different types of water (pure water, natural fresh water, potable water (treated drinking water), and seawater) and each has different mechanisms that determine the corrosion rate.
Similar to soils, the varieties of water make predicting corrosion rates difficult. Though pH level has the most profound effect, many parameters affect corrosion of metals in a water environment including oxygen content, water temperature, agitation, the presence of inhibitors, and tide conditions. Despite the difficulty of predicting corrosion, hot-dip galvanizing steel is one of the best methods of corrosion protection for submersed applications because of its complete, uniform coverage.
Bridges host the primary concern for steel in moisture-rich environments, as they often either span water or have submerged substructure elements. For elements completely submerged in water, there is constant exposure to the corrosive attacks of moisture. Galvanized steel performs very well under these conditions, performing flawlessly even in harsh water environments such as seawater for 8 - 12 years.
Maintenance-Free Cast Study
Riviere Cohon Gras Bridge- Perches, Haiti, 2019
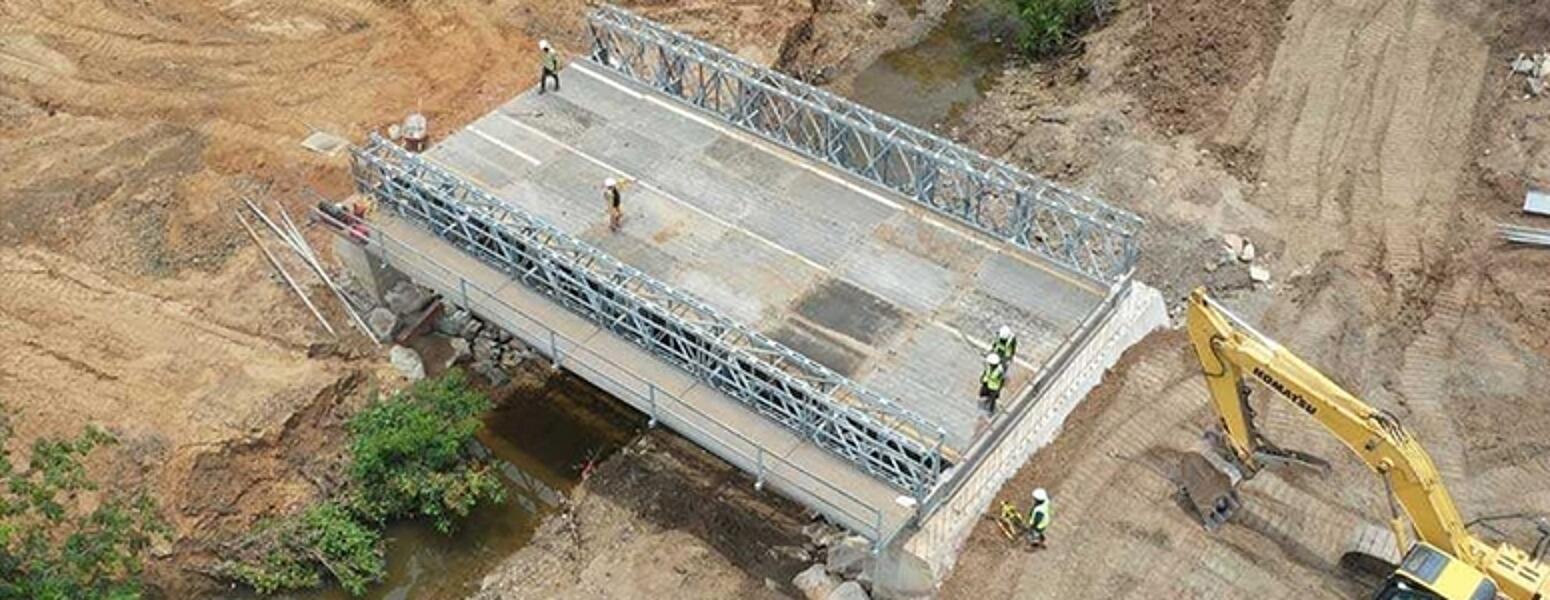
There’s an old saying, “one person’s trash is another person’s treasure.” In the case of the Riviere Cochon Gras Bridge, that saying became reality. An 80-foot section of the temporary Fore River Bridge which carried people over the river between North Weymouth and Quincy Point, Massachusetts for 15 years, was reused to help the community of Perches, Haiti.
Perches is a remote community in Haiti near the Riviere Cochon Gras. The river crossing was prone to regular flooding and there was no bridge in place. When the river flooded, residents were restricted from medical care and local services, and there had even been a few cases of drownings over the year as people attempted to cross the river to get into town.
With this re-purposed structure now in place, the bridge will provide residents greater access to other parts of their country and help to improve the daily lives of everyone in the community.
In its previous life, this bridge made up part of the massive temporary bridge on Route 3A connecting the city of Boston with the vacation/recreational area of Cape Cod. When the original Fore River Bridge was designed and built by Acrow Corporation, the company knew they had to build a temporary bridge that would be maintenance free for at least fifteen years. The company and the bridge owners got much more than they expected. The bridge handled about 46,000 total vehicles per day with a high percentage of heavy trucks at around 20% or 9,000 per day. Fifteen years of high traffic demand, harsh New England winters, salt and deicing chemicals were no match for the hot-dip galvanized coating on the structure.
Once the temporary bridge was taken down, the new bridge owner, the Cashman Family Foundation, knew there was much more life left in it and others who could benefit from the structure. Their idea was to reuse sections of the bridge to help third world countries connect people with local infrastructure, without the risk of crossing flooded waters. In Perches, an unpaved road with no crossing was the only way to access a local hospital and an industrial park to the North. During the three of four rainy months, the crossing is frequently impassable. The reused bridge section would literally be a lifesaver for the residents in the community.
With help from Tighe & Bond and volunteers from Engineers Without Borders, the Cashman Foundation worked with local officials to make the project happen. The section of the former Fore River Bridge required no repair, showed no signs of corrosion and required no additional coating costs for future protection.
Hot-dip galvanizing was the only coating able to stand the test of time serving 15 years as the Fore River Bridge in Massachusetts only to be disassembled, shipped halfway around the world, and then reused in Haiti with no signs of corrosion or repair required. Hot-dip galvanized steel’s durability and maintenance-free longevity make the possibilities for other projects like this endless.The life-cycle cost savings are too substantial to even put into numbers.
Plain and simple, this project is a win-win. Reusing the temporary bridge eliminates the need for reprocessing the galvanized steel for new projects, reducing environmental impact. The community of Perches, Haiti is now connected with potentially life-saving infrastructure for decades to come. None of this would be possible without the use of hot-dip galvanized steel.
According to Brian Brenner, an engineer with Tighe & Bond, plain and simple, this project is a win-win. Reusing the temporary bridge eliminates the need for reprocessing the galvanized steel for new projects, reducing environmental impact. And the community of Perches, Haiti is now connected with potentially life-saving infrastructure for decades to come. None of this would be possible without the use of hot-dip galvanized steel.