Efficiency
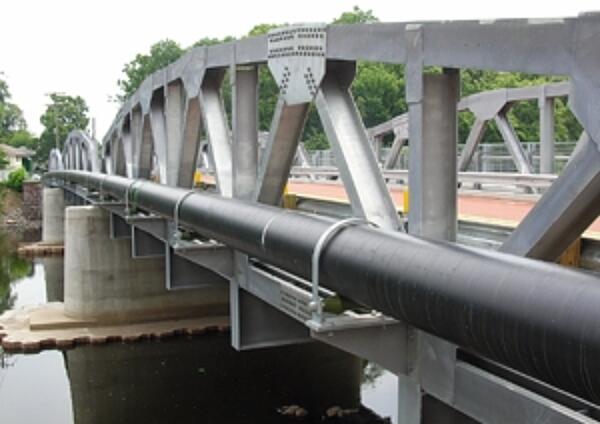
With galvanized steel, you can do more with less. Because of the high strength-to-weight ratio of steel, bridge elements or sign structures are less taxing on the support structure than significantly heavier materials, such as concrete. According to the World Steel Association, the strength-to-weight ratio minimizes substructure costs and can also save money on transportation and handling. Additionally, utilizing less material, one ton of steel can do the same as eight tons of concrete, positively contributes to sustainable development as well.
This benefit is particularly important for bridges spanning large bodies of water, wetlands, or environmentally protected areas, which may require cost-effective long span bridge elements to reach across the long distances in a weight-efficient manner. The ability to use long-span beams minimizes the necessary supports and reduces overall stress to the supporting structure. With galvanized steel you can do more with less, keeping bridge design as simple and strong as possible.
The reduced weight of the overall bridge structure will allow for lighter foundations, which can be particularly helpful in areas with poor ground conditions. Because the foundation transfers and distributes the weight of the bridge from the structure to the ground, a lighter foundation means the surrounding soil will not have to need as much reinforcement to support the weight.
Reducing the weight of a bridge or other transportation structure in total translates to cost savings throughout the process. One of the biggest advantages of steel is weight savings, which mean lower erection costs. The lighter weight of the pieces means they will require lighter, less costly handling equipment during construction.
Efficiency Case Study
City of Utuado Bridges (After Hurricane Maria)- Utuado, Puerto Rico, 2018
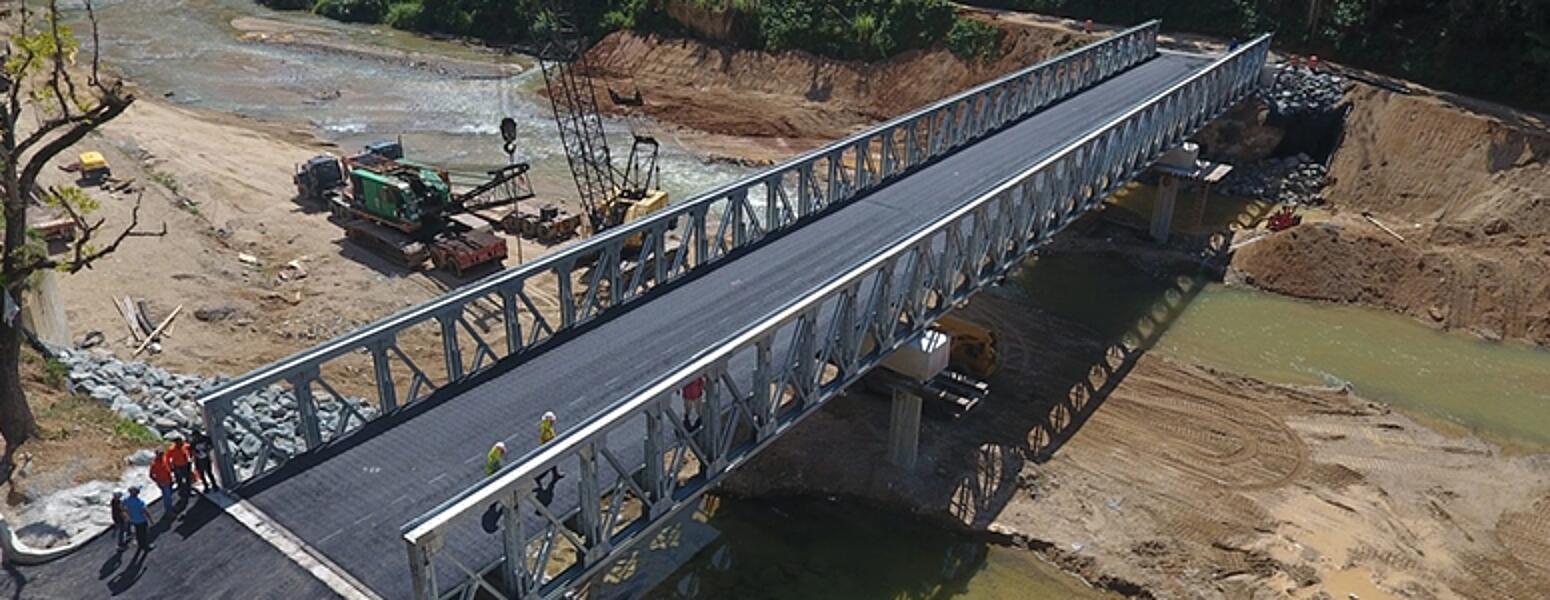
In September of 2017, Hurricane Maria, a category 5 storm, brought devastation to the island of Puerto Rico. Maria left the country without power and more than 1,100 lives were lost to this catastrophic event. Puerto Ricans were left struggling to access basic needs like fresh water, food, and shelter.
Back in Ohio, U.S. Bridge set to work to bring relief to the communities throughout the island by designing and installing modular Liberty bridges. To meet the urgent needs as winter was setting in and to ensure the bridges could survive the tropical climate, hot-dip galvanizing was chosen to protect the structures.
Employees of U.S. Bridge and V&S Columbus Galvanizing took a sense of pride in this project, even working through some of their own holidays (Thanksgiving and Christmas) to aid the families of Puerto Rico. In just six weeks the first of the hot-dip galvanized bridges were manufactured and installed, within six months, all of the bridges were completed reconnecting five communities across the island.
More than 850 metric tons of hot-dip galvanized US steel was used to create more than 950 feet of bridges, including the embedments, stringers, cross members, and all major structural support elements. The flooring was also galvanized and coated with a special grit surface. As the bridge was galvanized many miles away from where it would be erected, careful packaging and precaution was taken to guard against wet storage stain during transit.
Barges were loaded when the contractor had arranged them to go, and correct packaging was critical so when they arrived the contractor would receive the right bridge at the right town in the order necessary for the contractor and labor to get to work. Not only was hot-dip galvanizing production easier to accomplish in the heart of winter, it also meant no need for touch-up when the steel arrived. The end result was aesthetically pleasing, functional hot-dip galvanized bridges which will keep these communities connected for generations to come.