Case Studies
DIA Parking Garage Stairs - Denver, CO; 2011
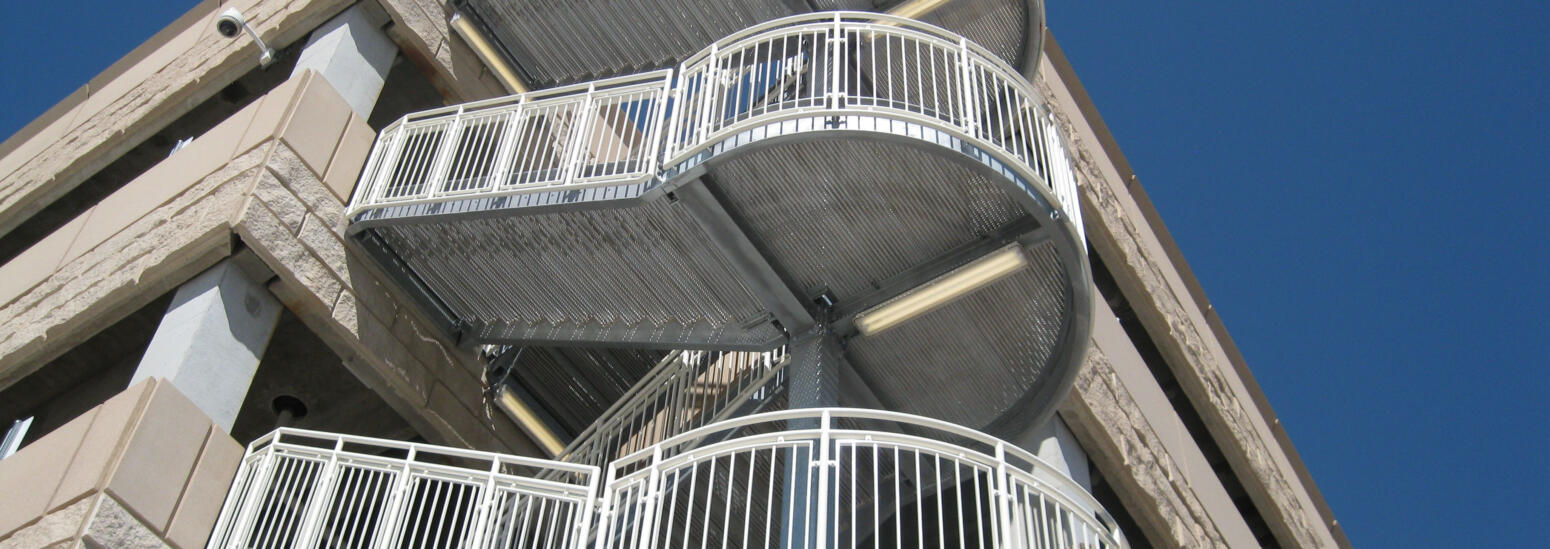
Denver International Airport (DIA) found out the hard way painted stairs on the parking garage only last 15 years. After learning this lesson, the stair towers were hot-dip galvanized (HDG) to provide durability and realize sustainable, cost-effectiveness on that portion of the $7.5 million renovations for worn out components. Safety has always been a major concern so HDG's projected 50 years or more of life lessened the concern. The HDG coating is harder than the steel itself making it perfect for the abrasive wear and tear of the 60 million passengers passing through the airport each year.
The airport environment is very corrosive due to engine exhaust and extreme temperatures of hot and cold weather; hot-dip galvanizing, with its metallurgical bond, was the wise choice to protect the stairs from this abuse. The stairs are viewed by every passenger arriving or departing the airport on passenger cars or rental car buses, and the combination of the duplex coating and exposed HDG was ideal to continue the mountain peak architecture of the original design and provide sustainable, cost-effective corrosion protection that will help keep the facility attractive and rust-free for decades.
Moynihan Station - Manhattan, NY; 2019
Moynihan Station expands the nation's busiest train station, Penn Station, New York across 8th Avenue into the historic James A. Farley Post Office Building, part of a mixed-use redevelopment of the entire block. The complete overhaul of the old post office and new design of a sky lit atrium had the specifiers thinking galvanizing from the start.
With tons of steel components exposed to the commuters visually it was really a no brainer to assure a long life cycle and minimal maintenance. The advantages of not having to shut down a busy train station for cosmetic repairs made galvanizing not just the smart choice but the only choice.
Moynihan Station is a world-class intercity and commuter passenger boarding concourse for Amtrak and MTA-Long Island Rail Road passengers. The facility will provide relief to Penn Station’s crowded boarding conditions for Amtrak’s intercity passengers and MTA-Long Island Rail Road commuter rail passengers. Retail and food shops will make this station a popular place to be and the galvanizing will assure it's there for a long time.
US 41 Retaining Wall - Fox Valley, WI; 2011
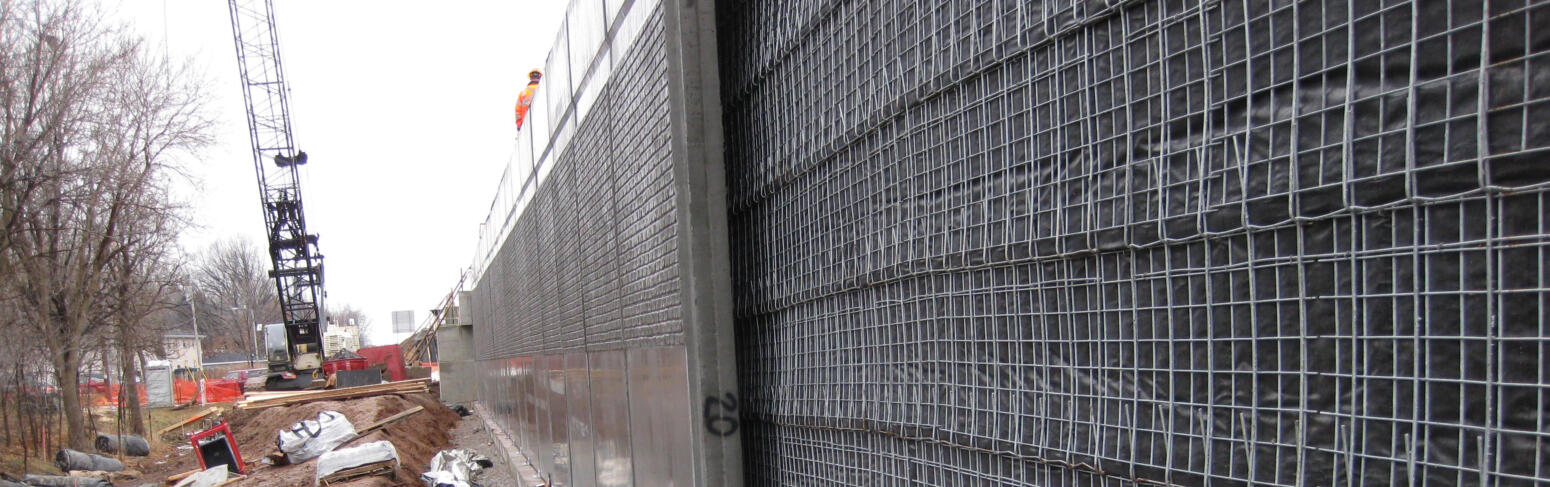
Reinforced soil retaining walls, commonly known as Mechanically Stabilized Earth (MSE) represent an innovative method of resolving familiar as well as unfamiliar and challenging problems. The walls behave as gravity structures in an integral unit and provide structural flexibility. Welded wire mats placed within layers of compacted backfill provide the necessary tensile strength, while native soils at the site or from the excavation are used for backfill. The resulting structure is strong and resilient. Hot-dip galvanized (HDG) wire ensures the strength and resiliency are maintained for 75+ years.
When the customer is expecting long life expectancy, galvanizing is the hands down choice to ensure the wall lasts for generations. Because maintenance of these walls would be expensive (if not impossible), the specifier needed a proven coating to deliver years of maintenance-free protection; HD provides that confidence. For taxpayers that means the low upfront costs of HDG provides positive returns for many years to come. For the taxpayer, it is a win-win; low upfront costs combined with long-lasting, zero maintenance. On top of that, zinc is infinitely recyclable and a common element in the earth's soils. As a result, no harm will occur to the land or water streams and there will be no worries about costly disposal in 100+ years. As our infrastructure shows rapid decay, the taxpayers want longer solutions with no environmental impact. HDG is a perfect fit. Projects such as this one are perfect examples of the cost-effective, flexible, environmentally safe benefits of HDG.
Bridges of Stark County-Stark County, OH; 1970s
The Bridges of Stark County Ohio are galvanized bridges and have been for 40 years. In the early 1970s, Rich Larocco was a young bridge engineer for Stark County, just out of college. At that time, 110 of Stark County's bridges were deficient and 50% of the bridge budget was used to repaint bridges. Rich worked with the former owner of the galvanizing facility to change those numbers. Rich decided rather than continue to repaint bridges over and over, he would dismantle the bridge. He had the decks and beams removed. The beams were sandblasted and galvanized. Then the entire "recycled" bridge was reinstalled. After that, they never repainted an old bridge or painted a new bridge even if the long beams or large trusses had to be progressively dipped in the galvanizing plant. There are 442 Bridges in Stark County, 335 of which are maintained by the county. Many are short span low clearance steel bridges over creeks and streams in rural areas, making an ideal environment for hot-dip galvanized bridges.