Durability
Another aspect of hot-dip galvanizing is its extreme durability, a key benefit for transportation elements across the spectrum. There are three keys to hot-dip galvanizing's durability: abrasion resistance, complete coverage, and uniform protection.
Abrasion Resistance
A unique characteristic of the hot-dip galvanized (HDG) coating is the development of tightly-bonded (3,600 psi), abrasion resistant intermetallic layers. This photomicrograph (below) is a cross-section of a galvanized steel coating showing the three intermetallic layers (Gamma, Delta, and Zeta) and top layer of pure zinc (Eta). During the galvanizing process, these layers develop naturally during a metallurgical reaction between the iron in the steel and zinc in the kettle. The photomicrograph also notes the hardness of each of the layers as a Diamond Pyramid Number (DPN). As you can see, the three intermetallic layers are harder than the base steel, while the eta layer has ductility which makes damaging the HDG coating very difficult.
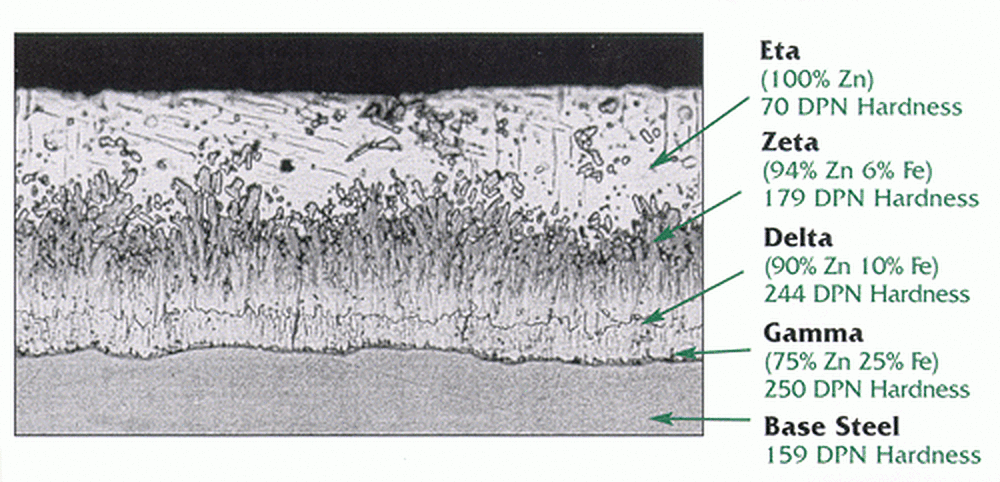
HDG's abrasion resistance is beneficial in several transportation markets. For instance, kicked up rocks and road debris on bridges and highways could easily scratch structure or guardrail coatings with less bond strength. Also, airport baggage handling systems need corrosion protection that will withstand the rough abuse of thrown luggage. Other corrosion protection systems, such as paint, only have bond strength of 300-600 psi. Due to rough construction environments, immersion in soil, and exposure to the elements, hot-dip galvanized steel elements in mechanically stabilized earth (MSE) structures capitalize on the dependable durability of the zinc coating. The abrasion resistant intermetallic layers of hot-dip galvanizing can withstand these rigors without damage or maintenance.
Complete Coverage
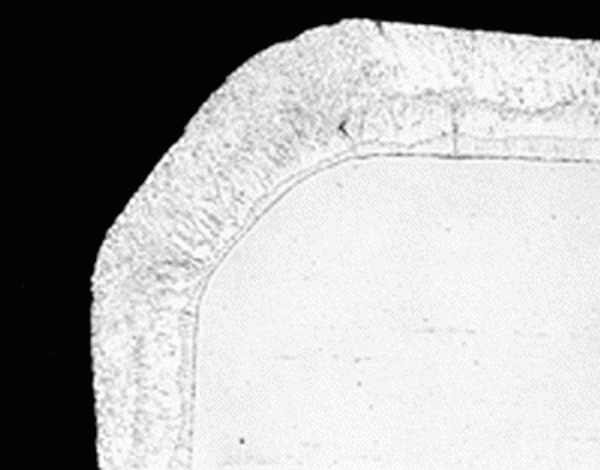
Hot-dip galvanizing is a total immersion process meaning the steel is fully submerged into cleaning solutions and the molten zinc coating all interior and exterior surfaces. This complete coverage ensures even the insides of hollow and tubular structures and the threads of fasteners are coated. As corrosion tends to occur at an increased rate on the inside of hollow structures where humidity and condensation occur, interior coverage is very beneficial. Hollow structures that are painted have no corrosion protection on the inside. Fully coating fasteners is equally important as they are utilized at connection points which are critical to structural integrity.
Uniform Protection
In addition to complete coverage, galvanized coatings also provide uniform coating thickness ensuring uniform corrosion protection throughout the piece, including vulnerable corners and edges. This is important when dealing with items such as baggage handling conveyors and pushers as well as handrail and bus/train station elements. Corners and edges of these items often have more potential for scratching or rubbing abrasion that would penetrate and weaken the already thinner areas of brush and spray applied coatings.
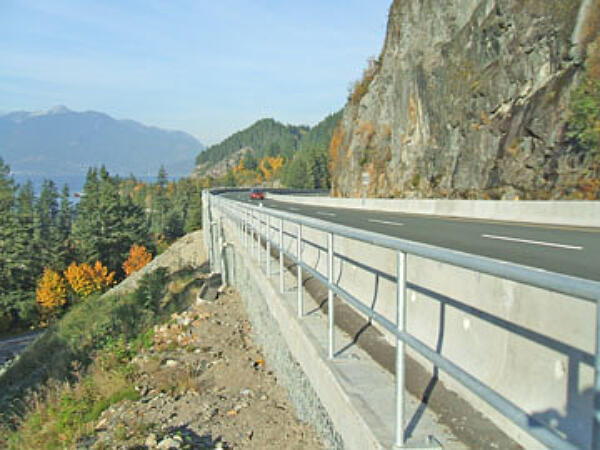
Complete, uniform coverage can benefit transportation infrastructure elements such as signage, electrical poles, handrails, etc. - made with hollow tubular materials which are protected inside and out by the consistent zinc coating. Protecting the entire fastener, including threads, along rail lines is critical to prevent maintenance repairs and keep tracks safe. Similarly, galvanized rebar is not allowed any voids in its coating, unlike epoxy-coated rebar, so there are no weak points when embedded in the concrete of bridges, runways, and other infrastructure.
Durability Transportation Case Study
Chicago CTA's 95th Street Red Line Terminal - Chicago, IL, 2018
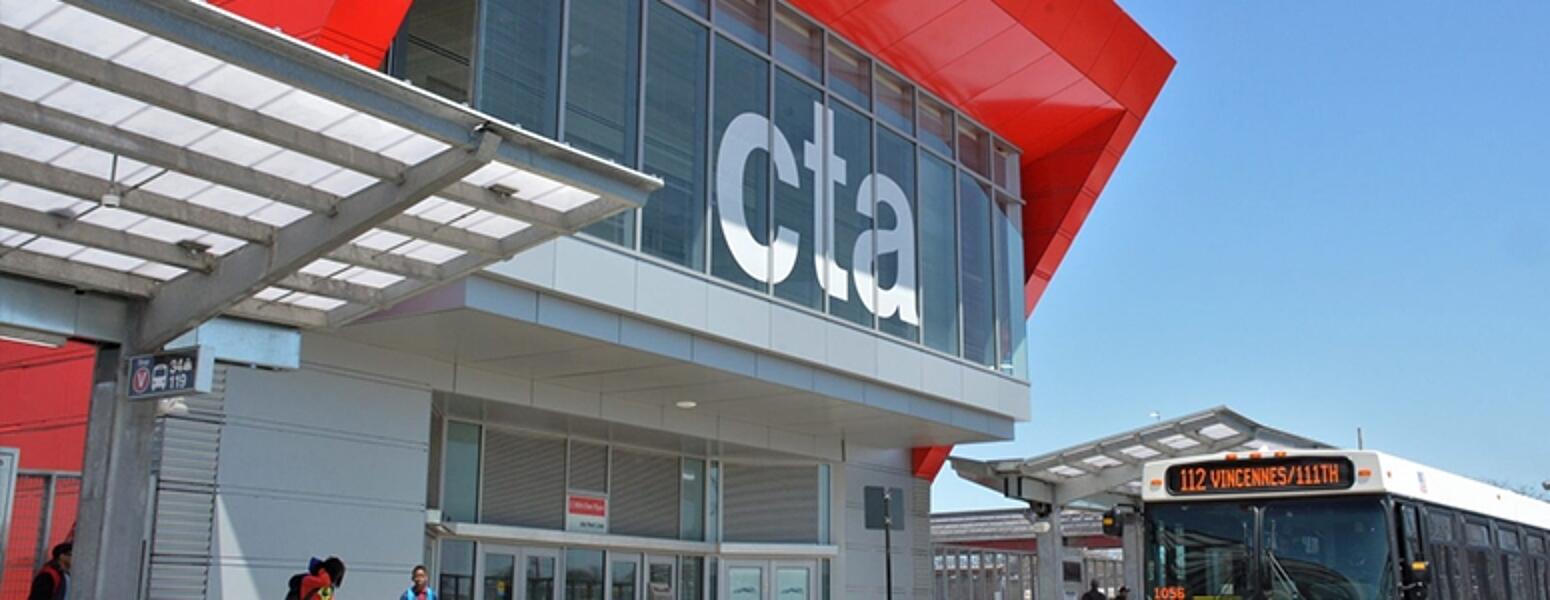
Partially covered in eye-popping red panels and largely enclosed by glass and galvanized steel, the new South Terminal rises above the Dan Ryan Expressway like a phoenix. The striking $280 million terminal features highly visible hot-dip galvanized canopy arms surrounding the entire facility and helps protect riders from the rain, snow, wind and biting cold of Chicago. The Chicago Transit Association’s (CTA) 95th/Dan Ryan station is a critical piece of the CTA's Red Line. It connects Far South Side communities to job centers throughout the region and serves as a transit gateway for the South Side and suburbs.
Early design considerations and the selection of hot-dip galvanizing (HDG) was strongly shaped by corrosion control over design life, ingenuity in use of galvanizing, final appearance and the strong visible zinc finish on the terminal canopy structure. Cost effectiveness of HDG was also paramount as this project required quick turn service from last minute design tweaks, and a demanding delivery schedule of trucks to the job-site to minimize road closures in the middle of the night.
The Red Line has the highest ridership of any "L" line and the 95th/Dan Ryan station is one of the CTA's busiest stations. Originally built in 1969, the station serves more than 20,000 bus and rail passengers a day with 24-7 Red Line service plus 1,000 CTA and Pace bus trips on typical day. The city estimates there are roughly 300,000 people who live within walking distance of the bus routes serving the terminal.
The station has been transformed into a modern, multi-modal transportation hub the city will be proud of and build momentum for Federal and State funding for the CTA’s proposed $2.3 billion extension of the Red Line which the CTA targets for a 2022 start. A strong positive around this $280 million development is the solution to an age-old problem of far south side residents facing prohibitive commute time to the city for employment. Important safety enhancements were also incorporated with widened platforms and bus bays for improved passenger flow and ease of congestion.
One fascinating aspect of the project was the decision to include a “living art” component. The art installation includes a radio DJ booth and features live artists mixing music, as well as oral histories. Internationally recognized local artist, Theaster Gates, is creating the largest public art installation in the CTA’s collection at the station.
One project titled “America, America” consists of two large tapestries, made from colorful strips of fire hoses and galvanized steel. The choice of materials refers to hoses turned on marchers during the African-American civil rights movement and, perhaps the bars of jail cells. The CTA says the tapestries “reflect the importance of the civil rights movement and the struggle and acknowledgement that the work of equity and equality is an ongoing effort not carried by one people, but by all.”
This new CTA Terminal is proving to be a transformative station and a vibrant landmark in the community. The use of hot-dip galvanized steel throughout the station’s exposed structures ensures this station will be able to continue serving the community for decades to come.
The distinctive new 95th Street Red Line station is a huge accomplishment for the city of Chicago and for the south side. The new station includes a heated glass pedestrian bridge connecting the terminals. The number of bus bays increased from 12 to 26 for reduced waiting times.