HDG Bridge Design Considerations
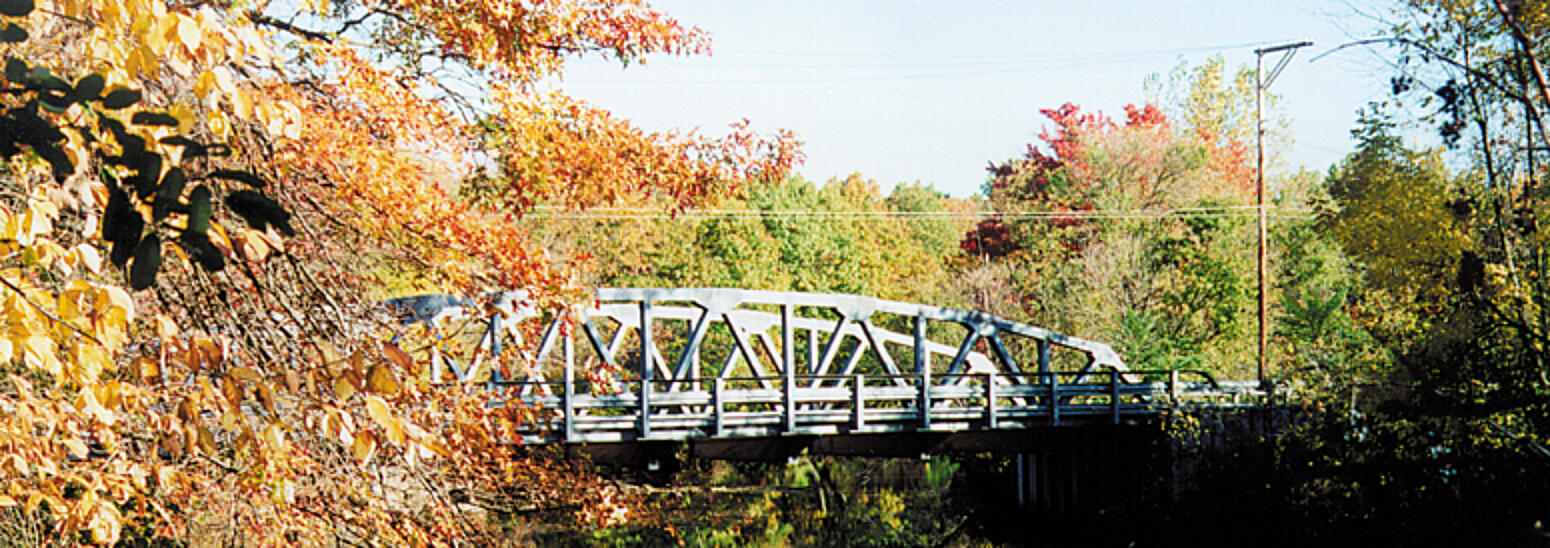
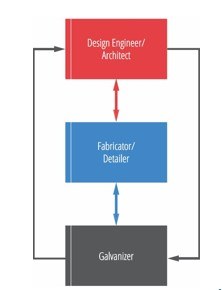
The key to designing successful hot-dip galvanized steel bridges begins at the drawing board. Communication between the design engineer, fabricator, and galvanizer early in the design process can alleviate potential pitfalls. There are certain design and fabrication details that will produce better quality galvanized coatings, help reduce costs, and improve turnaround times. There are a handful of ASTM specifications developed to facilitate the design of products for hot-dip galvanizing which are also explained in detail in the AGA’s design guide, The Design of Products to be Hot-Dip Galvanized after Fabrication.
Bridge engineering requires exact calculations and testing to ensure the overall integrity of the bridge. The information in the Design Guide is a great starting point, but there are a few additional considerations that should be factored into the bridge design when planning to galvanize. The hot-dip galvanizing process does not change the mechanical properties of the steel, but because the process requires the parts to be heated and cooled, it can induce or relieve stresses in the steel. Furthermore, the thickness and weight of the bridge parts will be slightly different after galvanizing because of the addition of the zinc coating. This can be particularly important in respect to connections and fasteners. This section of the publication will provide more information about specific, common areas of concern when designing galvanized steel bridges. These are good topics to discuss with the galvanizer early in the process.
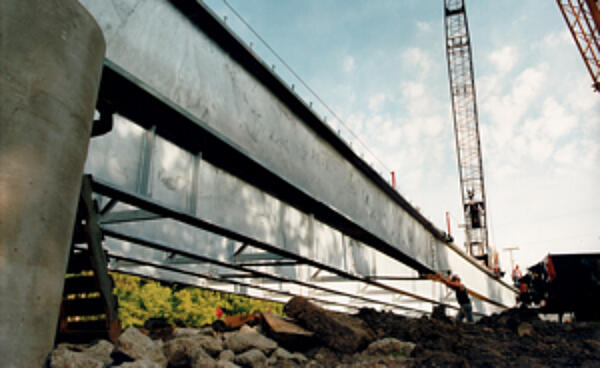
This section of the seminar will provide more information about specific, common areas of concern when designing galvanized steel bridges. These are good topics to discuss with the galvanizer early in the process. In addition to these bridge specific topics, engineers and designers should familiarize themselves with the basic design best practices covered in ASTM specifications and detailed in the Design Guide.