Bearing and Slip Critical Connections
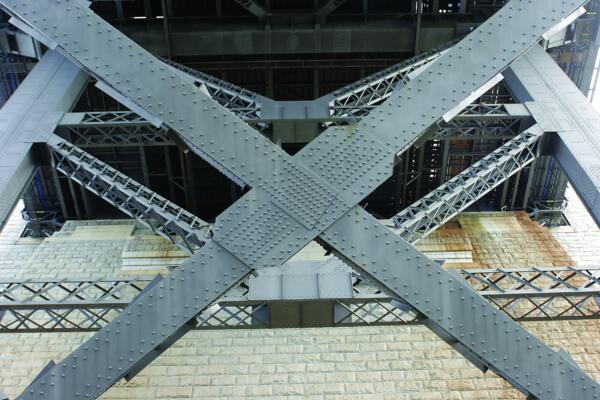
Bearing Type Connections
The presence of protective zinc coatings on the contact surfaces of bearing type connections is not detrimental to their performance. Galvanized joints of this type have a long and outstanding performance history in multiple industries. If hot-dip galvanized fasteners are to be used in a bearing type connection design, the clearance holes must be designed to the standard clearance hole diameter. This may necessitate unblocking or cleaning of the hole after galvanizing, but the American Institute of Steel Construction (AISC) guidelines in the AISC Manual of Steel Construction: Load Resistance Factor Design states oversized holes are not to be used in bearing type connections.
Slip Critical Connections
Hot-dip galvanized steel slip coefficients have been misunderstood for a number of years. Newly galvanized steel tends to be very smooth, and thus has a lower slip coefficient than bare or mild steel. However, weathered galvanized steel increases the slip resistance of galvanized faying surfaces. Furthermore, over time, two galvanized faying surfaces in a friction connection will experience a lock-up phenomenon. As friction continues to build between the two zinc surfaces, they will start to bond to one another, causing the surfaces to lock-up, and reduce the slip.
Lock Up Effect
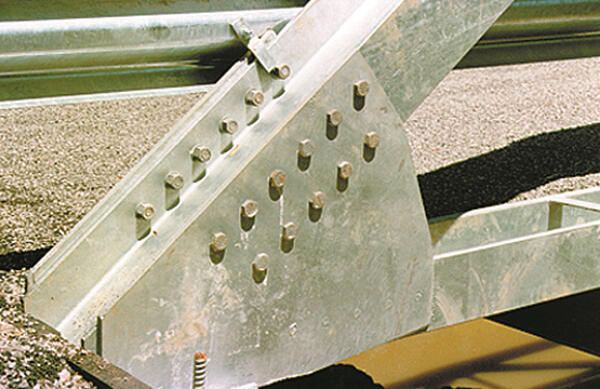
Some time after the connection is made, galvanized joints develop a characteristic known as "lock-up." Initially, galvanized surfaces will slip more than bare joints, acting like a lubricant. However, after the first few cycles of applied stress, any slippage will stop and the surfaces will start to bond to one another. The lock-up is a result of friction between the two galvanized surfaces during movement. To disassemble a locked joint requires prying of the steel surfaces. Therefore, if some initial slippage is acceptable for the joint, galvanized steel can be used in the slip critical connections with the same number of bolts as bare steel designs, because over time the galvanized surface will lock-up and provide a slip coefficient equal to black surfaces.
Mean Slip Coefficient
It is currently accepted the galvanized surface will have the friction properties as listed within AISC or RCSC specifications (Class A, mean slip coefficient, µ = 0.30) or AASHTO LRFD Bridge Design Specifications (Class C, mean slip coefficient, µ = 0.30). When galvanized parts are used for slip-critical connections, wire brushing of galvanized faying surfaces is no longer required for hot-dip galvanized structural connections, and is now prohibited by these standards. Painting the HDG coating with zinc-rich paints is known to greatly improve friction if time allows for qualification and testing according to the procedures in the RCSC standard (Appendix A). For example, AASHTO LRFD Bridge Design Specifications now includes a Class D surface condition (mean slip coefficient, µ = 0.45) to include blast-cleaned surfaces (including HDG) painted with organic zinc-rich coatings when qualified.
Tensioning of Galvanized Bolts
When tensioning using hot dip galvanized fasteners, a washer should be placed underneath turning pieces in order to prevent damage to the hot-dip galvanized coating. Any of the following three methods can be used to tighten hot-dip galvanized bolts: calibrated wrench, direct tension indicator, or turn of nut. Additionally, some type of lubrication is advised for ease of tensioning.