Girder Design Considerations
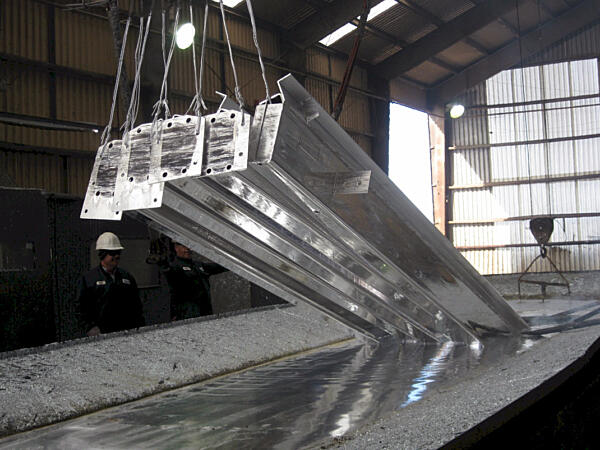
The unique web and flange steel thickness in modern girder design, coupled with welding 75-100 feet (23-31 meters) weld lengths, can create specific challenges associated with galvanizing that must be considered by the design team in order for the highest quality galvanized girder to be delivered to the job site. Here is a quick list for effective Girder Design:
- The flange-to-web thickness ratio should be no more than 3-to-1 to avoid distortion of the web.
- The finished galvanized girder should be air cooled and not water quenched to minimize the induced stress from the cooling cycle.
- Continuous welding should be used to prevent weld fracture from large forces generated when stress relieving the steel at the galvanizing temperature, or from trapped pre-treatment liquids expanding at the galvanizing temperature.
- Hot-dip galvanizing may accentuate or remove a camber. This is not usually problematic as the diaphragm members attached during construction can be used to draw the girder in to place. This is done by welding or fastening (with hot-dip galvanized connections) the diaphragm steel members to the girder, starting at one end of the girder and working to the other end.
- Stiffeners should be used and they should be liberally cropped (1" [2.5 cm] or greater) to allow for the free flow of cleaning solutions and molten zinc within the web space.
- Steel should not be left in the molten zinc bath longer than necessary. A longer immersion time applies more than the necessary to heat the steel and can result in relieving more stresses which may manifest as warpage/distortion.
- Any lifting (material handling) of the girder should be at the quarter points to avoid permanent deflection caused by the self-weight of the product.
- To completely support a positive or negative camber and avoid flattening, lay the newly galvanized girder on the strong axis and support with as many blocks as possible.