Steel Selection
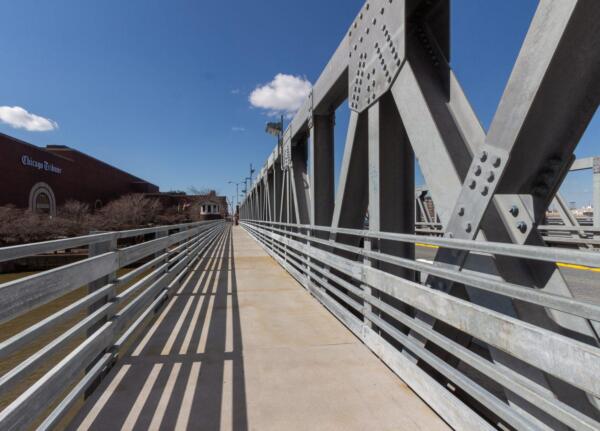
Steel composition has a profound effect on the characteristics of the galvanized coating. Selecting steels with recommended chemistries for hot-dip galvanizing is important to help control the coating thickness and appearance. The two trace elements that are most important, as they act as catalysts to the galvanized coating growth, are silicon and phosphorous. There are a few guidelines in steel selection to try to control the level of these trace elements and others to provide typical galvanized coatings:
- Levels of carbon less than 0.25%, phosphorus less than 0.04%, or manganese less than 1.35% are beneficial
- Silicon levels less than 0.04% or between 0.15%-0.22% are desirable (Silicon may be present in many steels commonly galvanized even though it is not a part of the steel’s controlled composition, because silicon is used in the steel deoxidation process and is found in continuously cast steel.)
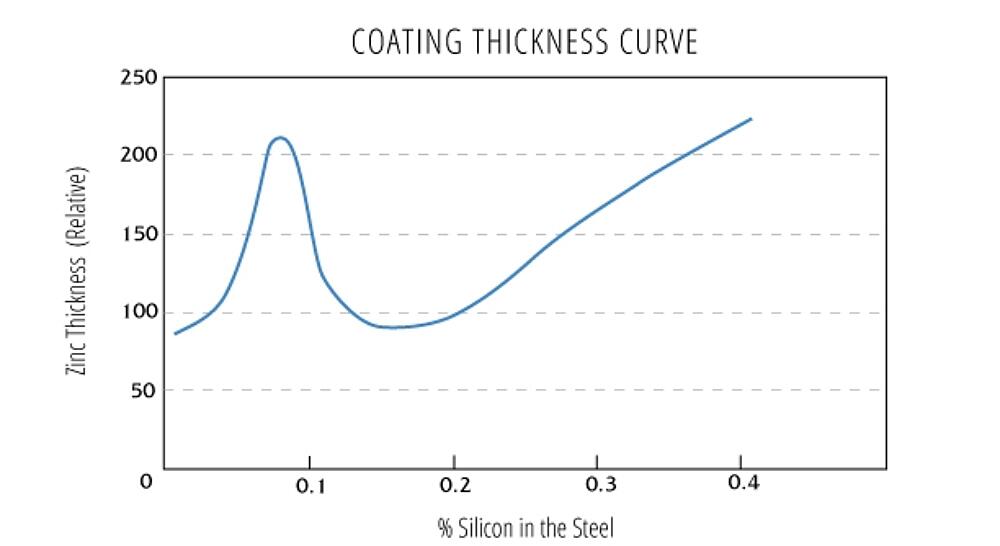
Steels with the recommended ranges of silicon and phosphorus will develop typical zinc-iron alloy layers that represent 50-70% of the total coating thickness, with an outer layer of free zinc. However, even when both elements are individually held to desirable limits, the combined effect between them can still produce an atypical coating.
Atypical galvanized coatings produced from reactive steels may produce coatings comprised entirely or almost entirely of zinc-iron alloy layers (below). These tend to be thicker coatings that can affect both the appearance and adherence of the zinc coating. Because of the increased thickness, atypical coatings tend to have a matte gray appearance and a rougher surface than typical galvanized coatings. If the highly reactive steel leads to an excessively thick coating, adhesion concerns such as flaking and delamination can occur, particularly under external stress.
Reactive steel are still galvanized on a regular basis, and it is important to note the difference in appearance has no effect on the corrosion protection afforded by the zinc. However, the additional coating thickness can cause other concerns, particularly for bridge designs.
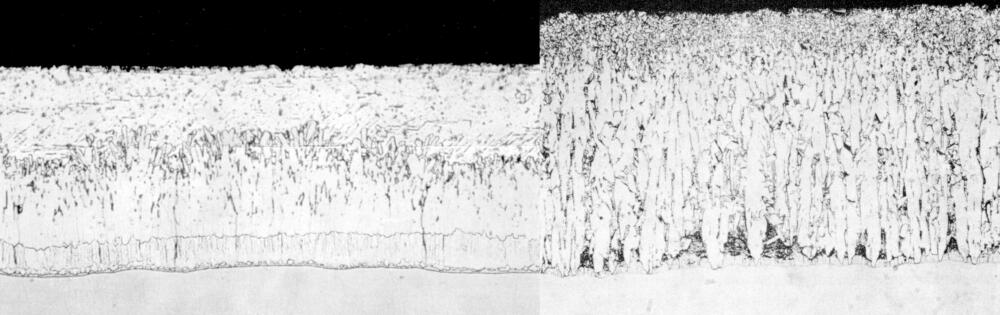
Coating Thickness
In order for the metallurgical reaction between the iron and zinc to occur, the steel must be heated to the bath temperature. Because certain bridge elements, such as girders are often large, heavy structures, they are more susceptible to producing thicker coatings. First of all, the larger pieces will be in the bath and/or near bath temperature for longer periods, which can lead to more coating growth. Second, the most common steel bridge specifications have maximum silicon ranges at 0.40%, so it is possible to have highly reactive steels to start with. Finally, as mentioned before, progressively dipped pieces are likely to have thicker coatings in the overlapped area. It is also important to consider the chemistry of weld rod material when welding before galvanizing, because the silicon content of the weld material can affect the coating growth in that area.