Increased Inspection During Intake
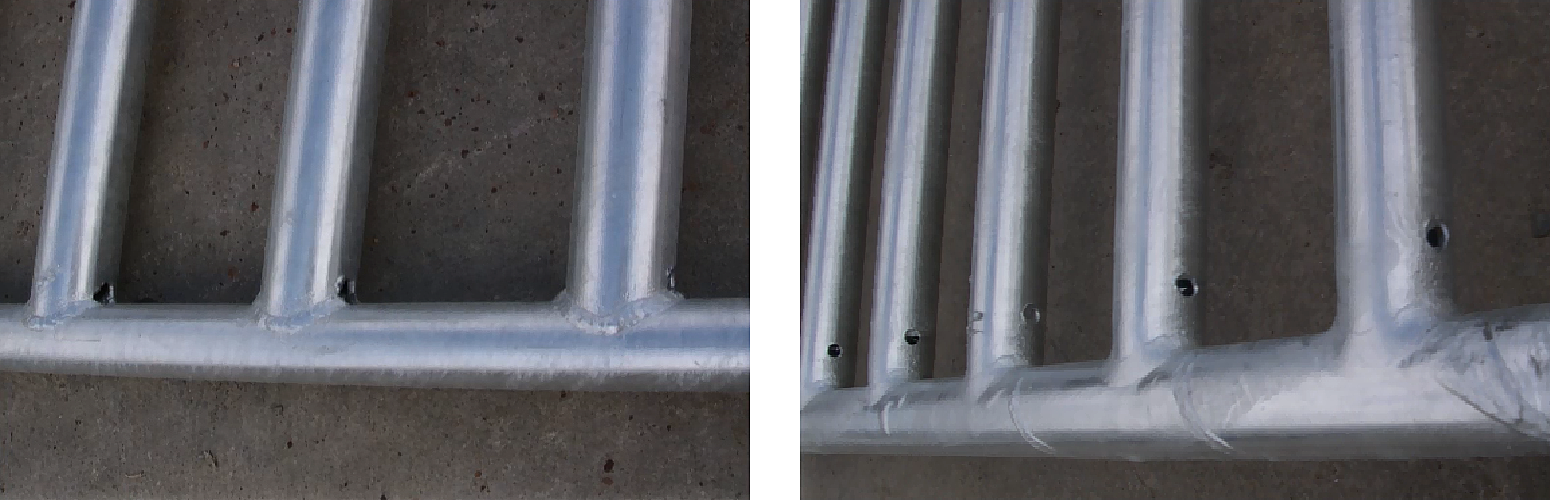
Before processing material slated as AESS, a more intense screening of the parts is warranted. It is beneficial to have an internal meeting with operations personnel (kettle and finishing), sales, shift foreman and quality manager, etc. when the material arrives to ensure everyone is on the same page with processing the job. Based on the AESS category characteristics and any custom characteristics desired, it is important to verify the proper fabrication methods and cleaning were executed such as abrasive blast cleaning before galvanizing, venting/drainage holes, removal of welding slag and spatter, avoiding weld porosity, grinding of HSS seams and mill markings, etc.
When working with ASTM A123 projects, it is common to let some of these things slide, or accept less than the required venting or drainage, but when trying to achieve AESS finishes, you may need to establish and enforce more strict standards with your customer around these items as well as larger and strategic venting/drainage. Additionally, it is helpful to inspect for and notify the customer of any damages (cosmetic or otherwise) to the steel before galvanizing as a result of transportation or handling. Hot-dip galvanizing accentuates many of these imperfections, so starting with a clean, properly fabricated piece is critical. These initial surface imperfections are much more difficult and time/labor intensive to address or remedy after galvanizing than before. If you notice any issues or have concerns, it is best to contact the fabricator before galvanizing the pieces to discuss remediation. To avoid the perception of blaming the fabricator, the best practice is to plan for potential remediations to address skipped design/fabrication steps before any work begins and mutually agree on a procedure for communicating and resolving such issues.