Hanging Material
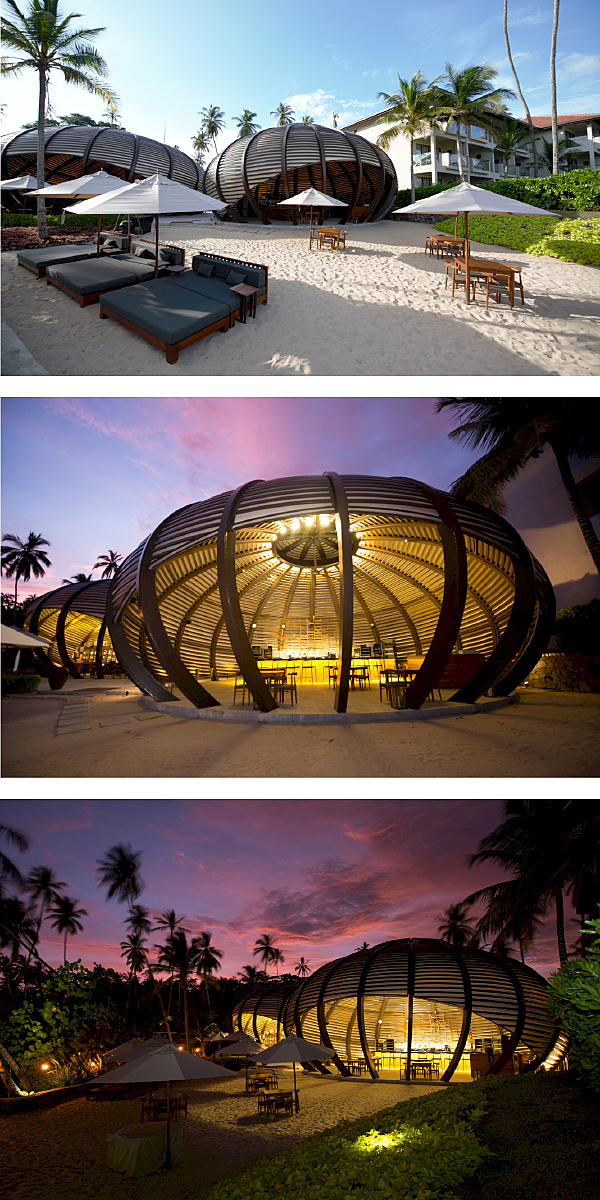
For most galvanized articles, the typical practice is to fit the highest volume possible on a rack. However, when working with AESS material, or other projects looking to maximize appearance, the best practice is to hang fewer pieces on a rack. This provides advantages such as reducing the time and labor required to smooth all touch marks and the ability to immerse and withdraw racks quicker. Planning to run less material per rack will require more forward thinking when pricing your quote, as it may be beneficial to plan out how you will space a rack for maximum loads without compromising appearance. Your target cost per rack should be applied to the necessary square footage needed to accommodate the AESS pieces, even if some of that space is bare.
In addition to hanging fewer pieces on a rack, it is also beneficial to connect the material with looser wires or chains. This allows the pieces to float in the kettle without contacting the wires to reduce chain and wire marks on the final piece. Depending on the shape, weight, and level of AESS desired, it may also be necessary to discuss optimizing lifting points with the customer. There may be areas of the piece which will be less visible and therefore might be less concerning if marks from the process are left.
Finally, hanging material to allow for the sharpest dip and withdrawal angles in the molten zinc should be prioritized. A sharper angle allows for quicker immersion and withdrawal, reducing the opportunity for excessive coating buildup, inclusions inside hollow parts, and oxide lines while maximizing drainage. This reduces the need for smoothing zinc runs or drainage spikes.