Laydown, Storage, and Handling
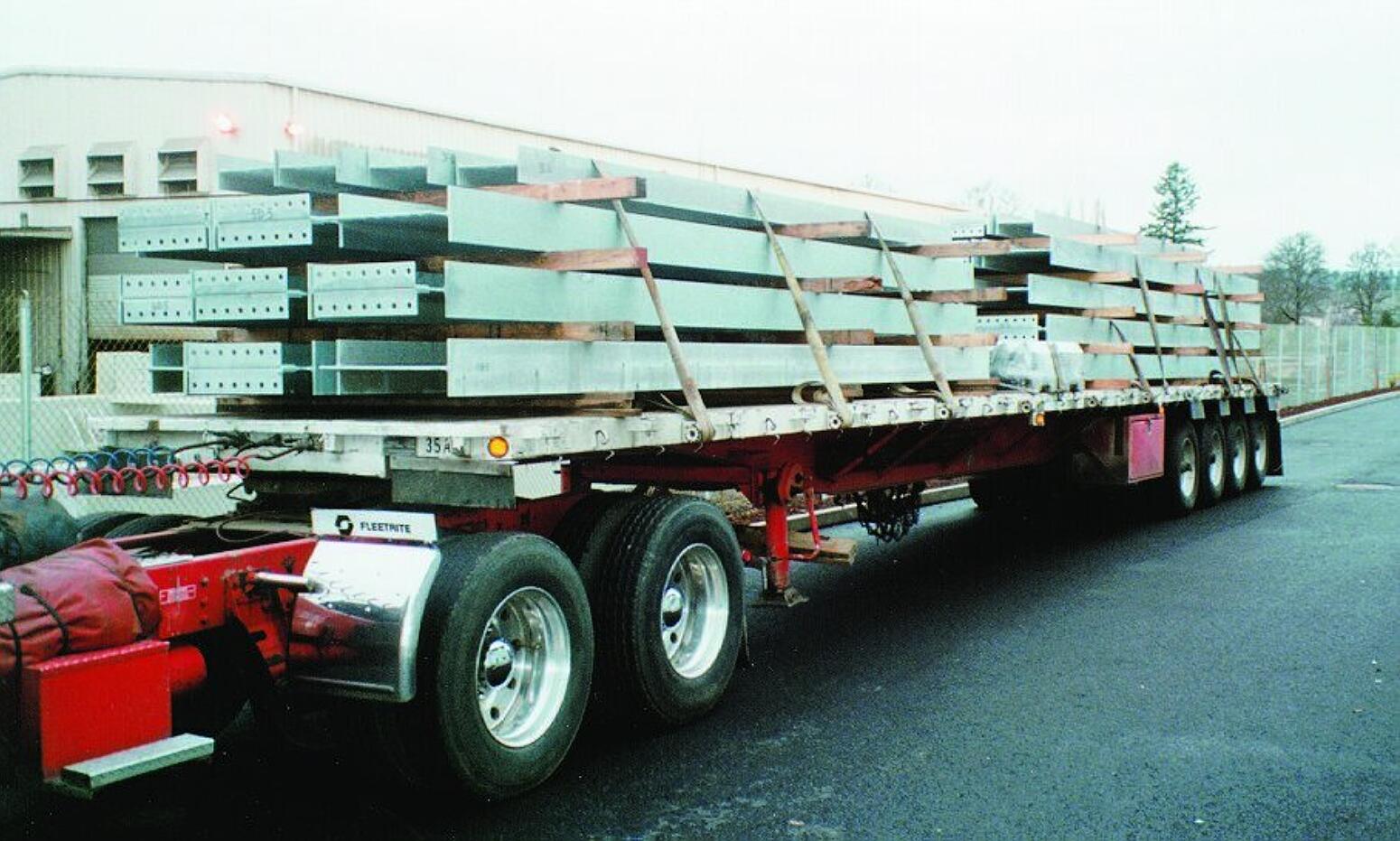
Whether at the galvanizer’s facility, customer’s shop, or erection site, it is important to use proper laydown, handling, and storage practices to avoid any post galvanizing visual concerns. Considering everything with AESS projects is focused on appearance, it is important to take care in the selection of dunnage as well as how you lay down the material. Often when hot-dip galvanized steel is placed onto dunnage, it is not completely cooled. This can char the wood dunnage and leave burn or discoloration marks on the steel.
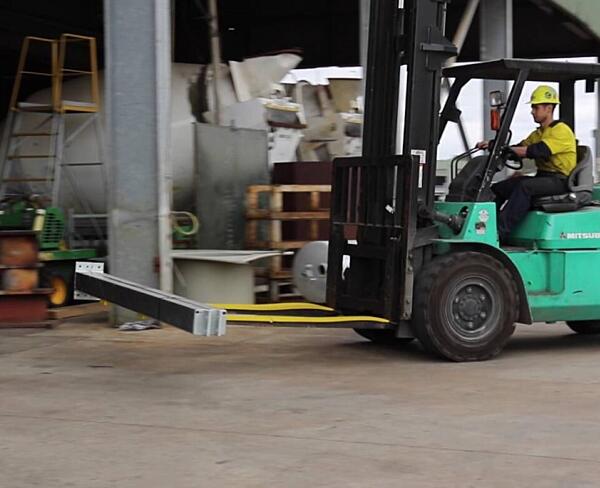
Wet Storage Stain (WSS) is the most common storage concern. A detailed list of best practices to minimize or avoid wet storage stain is provided in the AGA publication Wet Storage Stain. If wooden spacers are used to promote free flowing air around the surface of AESS members, avoid resinous or sappy woods known to cause staining. Styrofoam or synthetic spacers and rope are sometimes used in place of or in conjunction with wood dunnage, depending on the type and weight of the material, to avoid marring the material during storage or shipment. There are practical limitations to avoiding WSS at the plant and in the field. Therefore, it is best to address customer concerns over WSS before hot-dip galvanizing by discussing these limitations and mutually agreeing on the preventative methods to be used at the plant. Further, it is also in your best interest to help the customer develop a procedure at the job site for avoiding WSS, determining rejection/acceptance criteria, and cleaning with surface conditioning disc/belts (when necessary).
Some galvanizers are fairly limited in their storage options due to space constraints and should evaluate their capabilities before storing finished AESS work at the plant. In these instances, it may be beneficial to work with the customer to have tighter pickup schedules to move the galvanized material to a more ideal storage area at their facility or the job site. It is also a good idea to consider special packaging and shipping procedures for AESS materials. For example, to minimize cosmetic damage from handling, nylon slings can be used for lifting, and carpet/padding can be placed on lifting devices, forks, stands, and rests. You may also consider additional cushioning on dunnage. Where possible, take photos of outgoing loads to show the condition of the material prior to leaving your property.