At the Kettle
There are things that can be done during the dip, while in the bath, and upon withdrawal of the steel in the kettle that can help maximize appearance. As noted in the hanging section, working to immerse and withdraw the pieces at a steep angle and consistent withdrawal rate provide the best opportunity for a smooth finish. For the galvanizer to employ these best practices, some pieces require additional and/or very strategic venting and drainage placement, which is something that should be addressed at the pre-planning meeting and verified during intake. Furthermore, it is beneficial to have additional personnel around the kettle when dipping AESS material. These extra eyes and hands can help move skimmings away from the withdrawal surface, knock off drips to avoid spikes, or even deploy air wands.
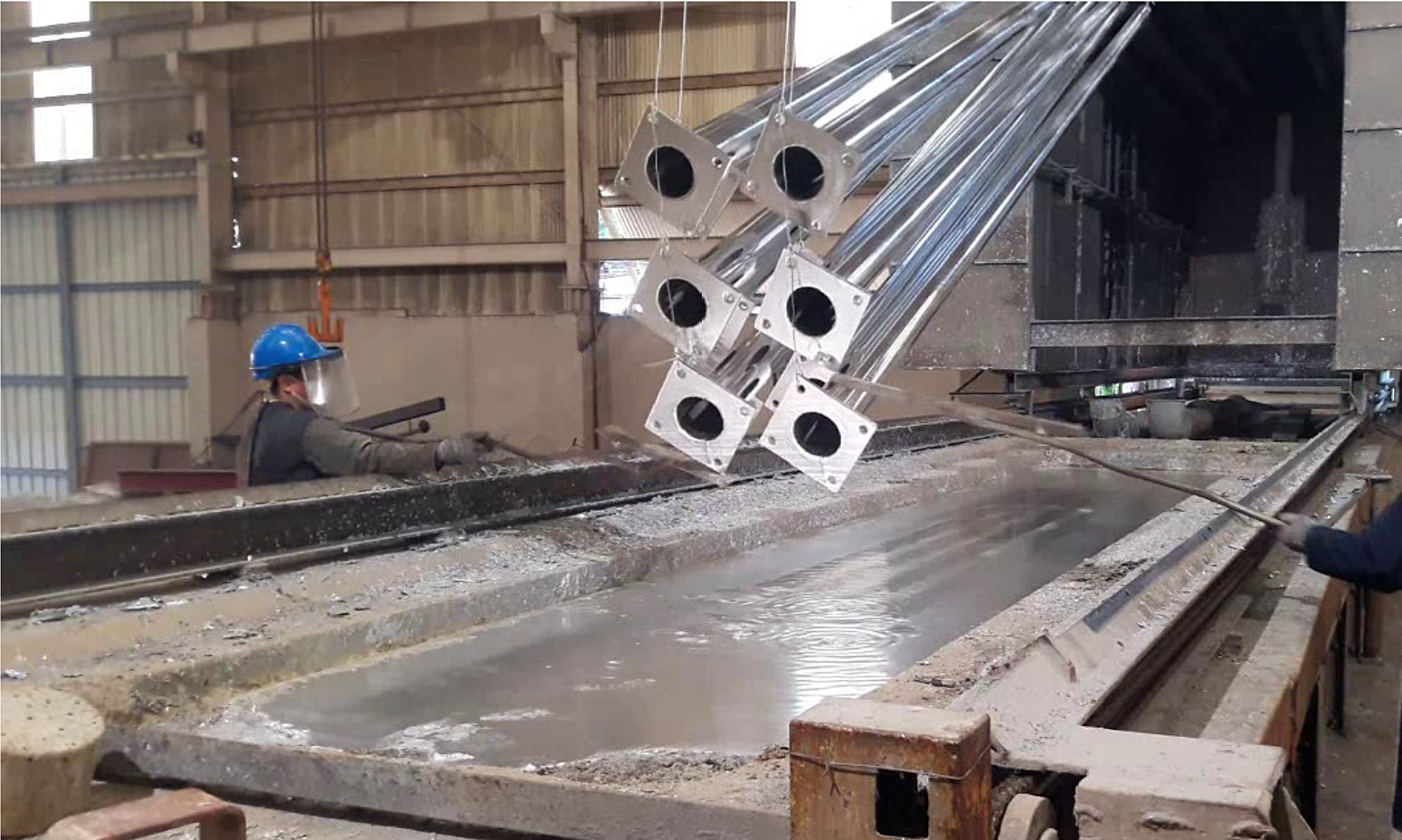
While in the galvanizing bath, it is critical to move the pieces within the bath more thoroughly and consistently than high volume racks. This ensures the parts are moved away from their hanging wires and /or chains and have the opportunity to float in the zinc bath to coat all surfaces. Some common methods include shaking or vibrating the parts within the bath. The use of vibratory equipment is known to be especially effective at improving aesthetics for pipes and small parts. However, movement should be done with caution to avoid disturbing dross particles at the bottom of the kettle. Some galvanizers prefer to process AESS material soon after drossing, but it is helpful to allow a settling period after drossing (or any other activities that stir up dross) to minimize carryout onto the parts. As dross inclusions are unsightly and difficult to clean and smooth effectively after galvanizing, it is best to minimize or avoid them during processing using any available means.