Cooling
Extended cooling times can sometimes promote the Kirkendall effect and increase susceptibility to peeling. Water quenching or spraying parts with a fine mist of water can be used, but these practices may not be desired if the part is specified to be painted or powder coated after galvanizing, or if there are concerns of warpage/distortion. At minimum, avoid stacking hot parts on top of each other which is a practice often associated with peeling.
A fish-boning appearance (common for large diameter parts) results in uneven striping across the entire part, and can be extremely challenging to smooth depending on the AESS Category Characteristics desired. Sometimes fish boning can be avoided by improving the cooling of the part so the eta layer does not remain semi-molten. Common methods employed by galvanizers to avoid this appearance include a combination of maintaining the steepest angle possible during withdrawal and cooling to allow hot air to escape from inside the part, rapid withdrawal rates, and spraying parts with a fine mist of clean water immediately upon withdrawal.
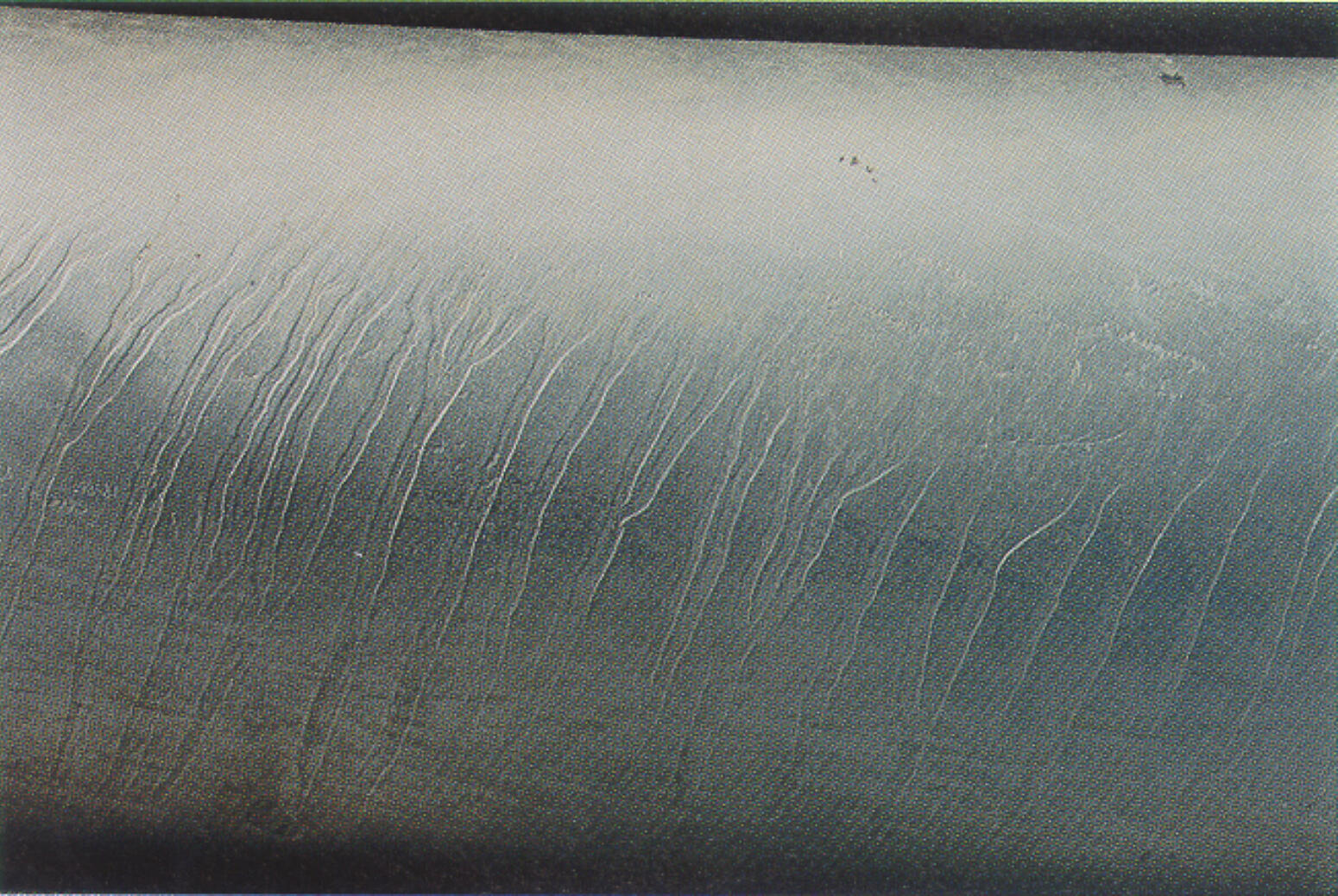