Grinding, Filing, & Other Smoothing
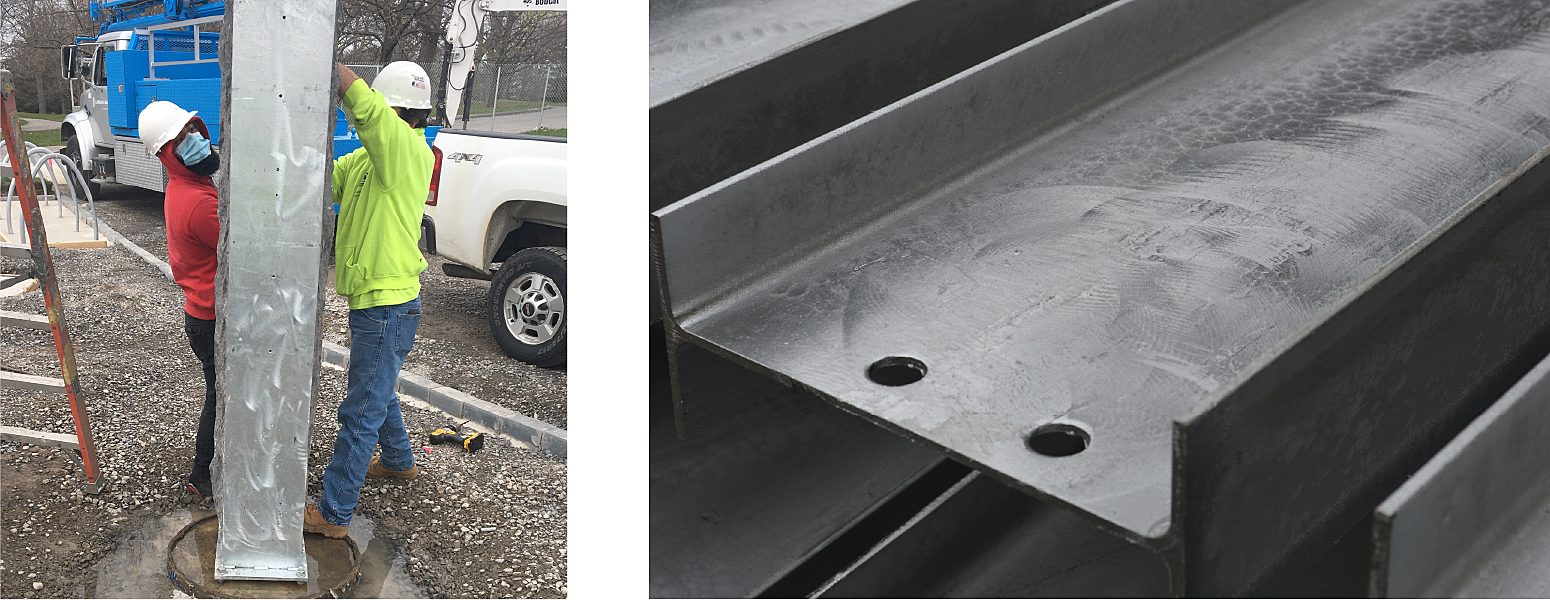
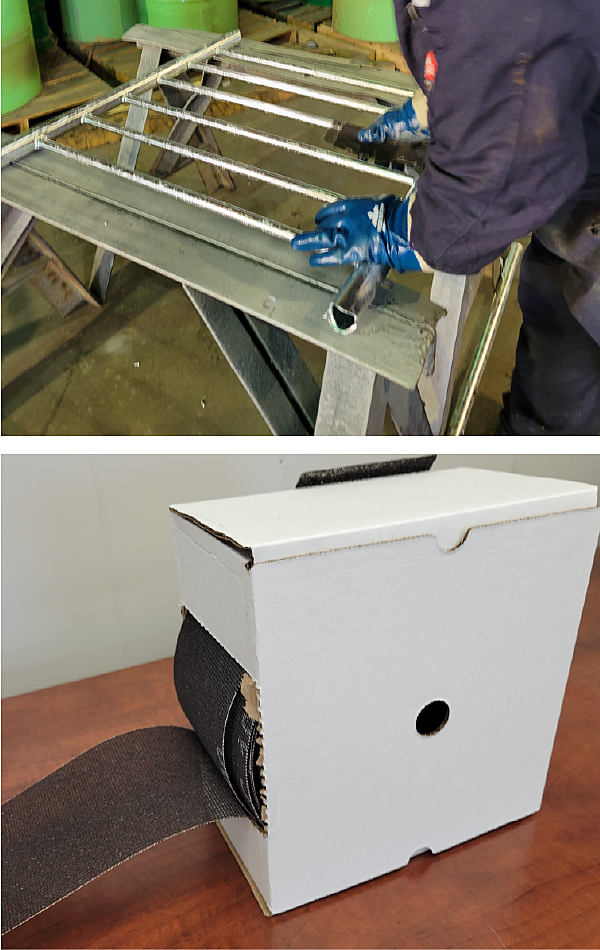
A standard practice in the finishing and touch-up area is to use hand grinders to touch-up zinc build up, spikes, and other cosmetic issues. Hand grinders are a quick and effective method for cleanup, but they also leave distinct marks on the coating surface which can cause frustration in AESS projects. Some galvanizers find it helpful to perform smoothing with wire brushes and hand files first to better identify the areas where grinding or other power tools with sanding pads are truly necessary. If you elect to use grinders, they need to be used with caution and to minimize any surface marks on the coating. In areas where grind marks cannot be avoided, it would be preferable to limit grinding as much as possible and follow up with hand filing or sanding.
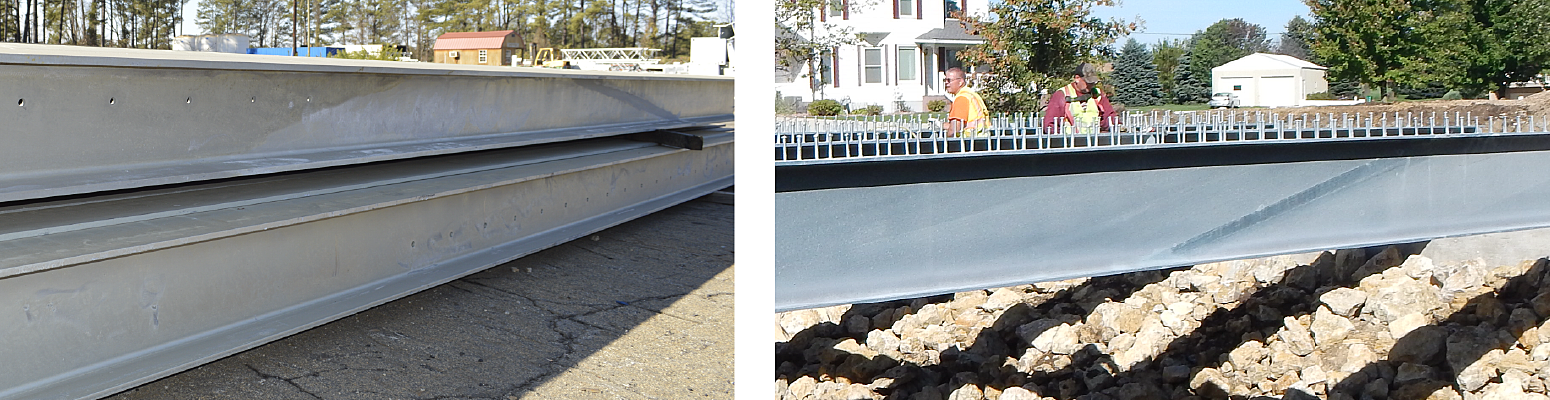
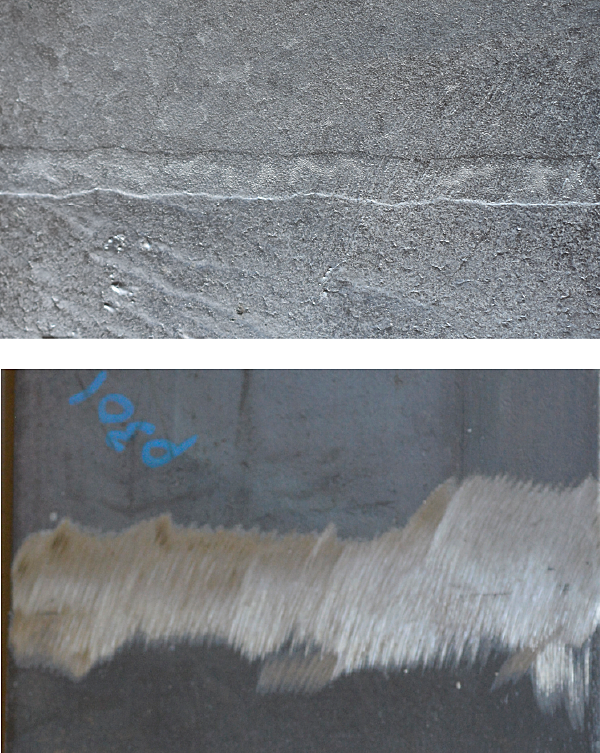
Three surface conditions that also may require discussion before grinding or smoothing are progressive dip lines, thermally cut edges, and raised welds. These surface conditions are likely to irritate the customer, specifier and/or end user on higher levels of AESS projects. It is important to consider whether the remedy will be more detrimental than the existing condition. This is an issue that is highly recommended to involve the customer and end user in initial discussions and/or when the issue arises. You may find different customers prefer to leave them while others prefer touch-up.
Finally, plugging vent/drain holes will require additional care and finishing standards. Similar to dip lines and raised welds, this is an area where discussion with the customer, specifier, and end user may be necessary. When working with AESS projects, the customer may prefer a specific type of plug, steel reinforced epoxy, more smoothing, putty, and/or touch-up materials around the plug to improve the visual element of the holes. Discussion during the bidding phase, potentially using visual examples will help the galvanizer to account for the additional cost of specific plugs and/or any additional touch-up work in the bid.
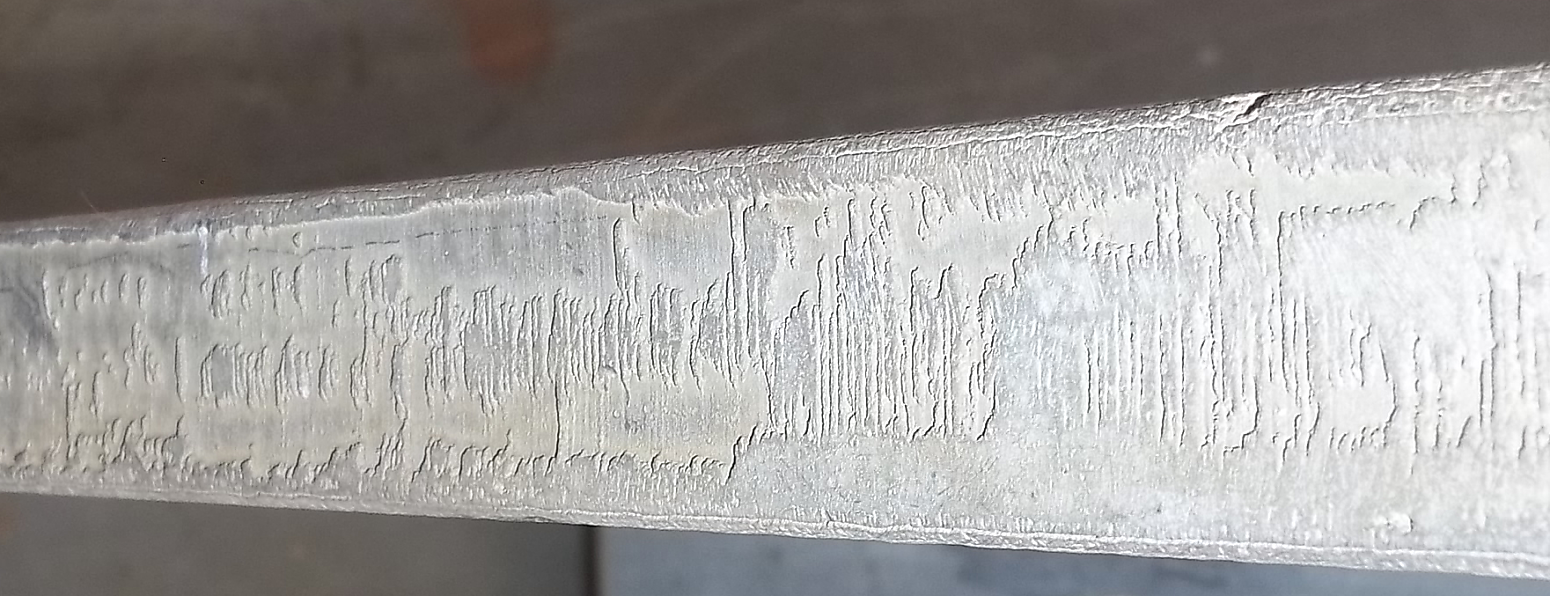
To achieve a high-quality finish along thermally cut edges, the steps necessary are beyond the capabilities of the galvanizer. The fabricator must ensure the flat surface of all thermally cut edges are ground at least 1/16 in. into the parent material before galvanizing in addition to the grinding of sharp edges as outlined per AESS category requirements. Despite a high initial cost, this method is much more efficient, cost-effective, and visually appealing compared to remedying the appearance after hot-dip galvanizing. Due to the additional cost to remedy this appearance, the appearance of thermally cut edges should be addressed when discussing both budget and AESS Category Characteristics.
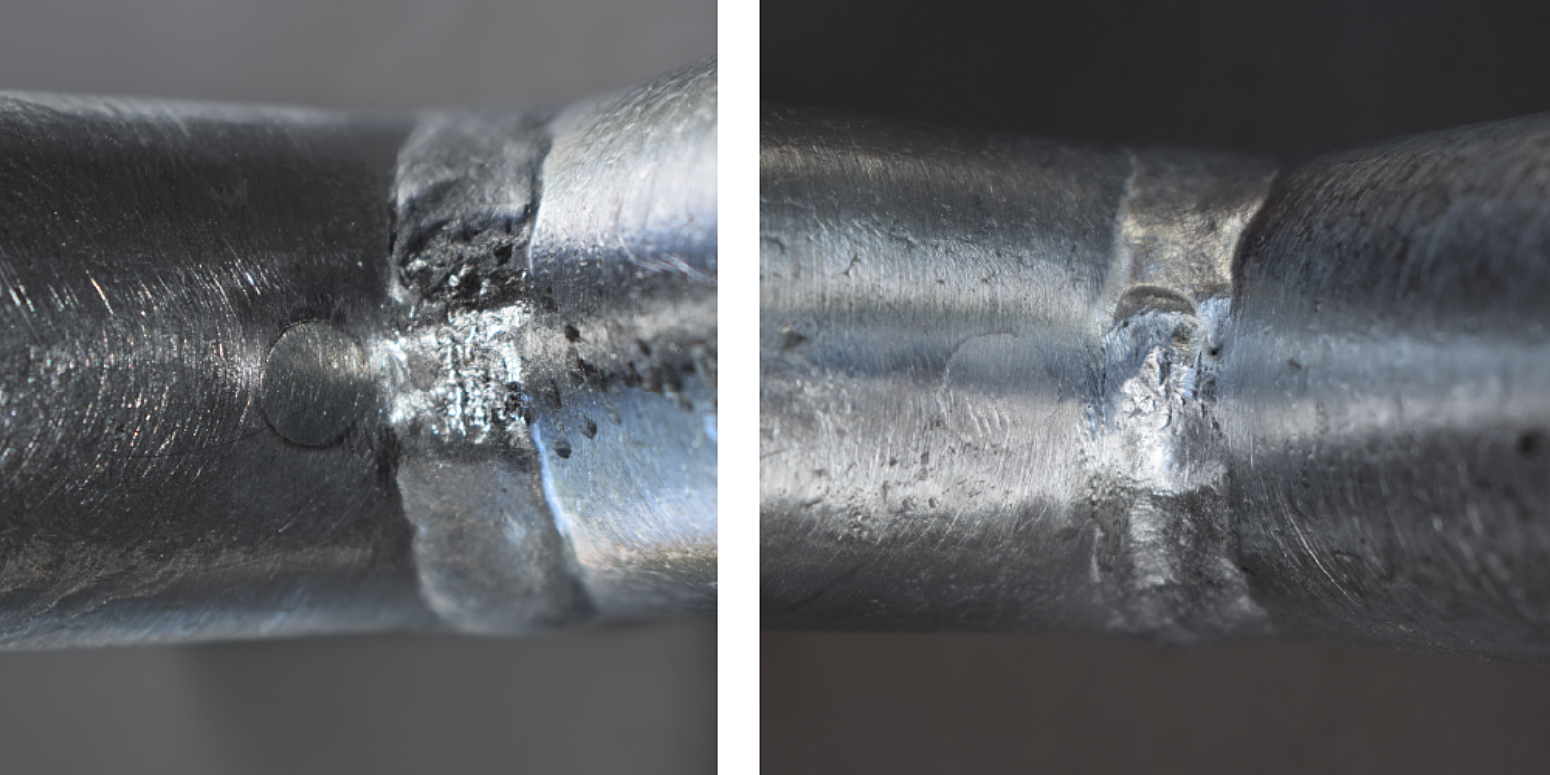