Hot-Dip Galvanizing Process
Whether an artful sculpture glinting under the sun or a sturdy bridge arching over a rushing river, hot-dip galvanizing protects steel from corrosion for generations throughout the world. New technologies and creative chemistry continue to evolve this 150-year old process, which facilitates its continued use in myriad applications as well as innovative ideas for new ones. Before we get into the details of designing for hot-dip galvanizing, it is important to understand the hot-dip galvanizing process. The galvanizing process consists of three basic steps: surface preparation, galvanizing, and inspection.
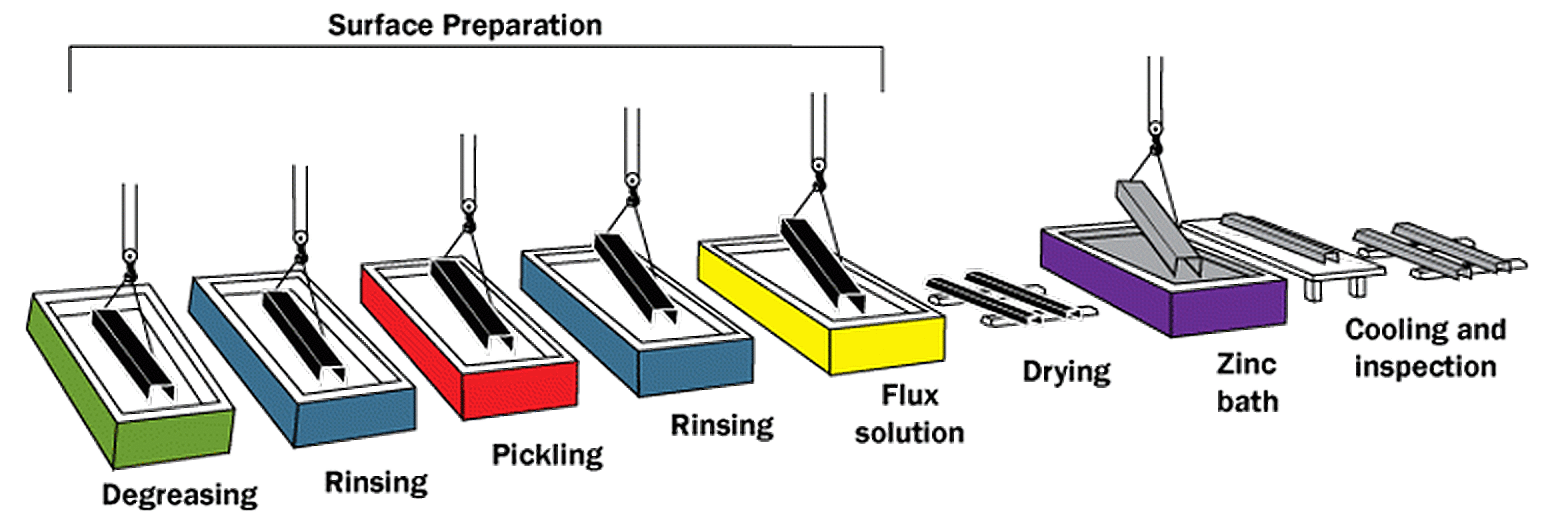
Surface Preparation
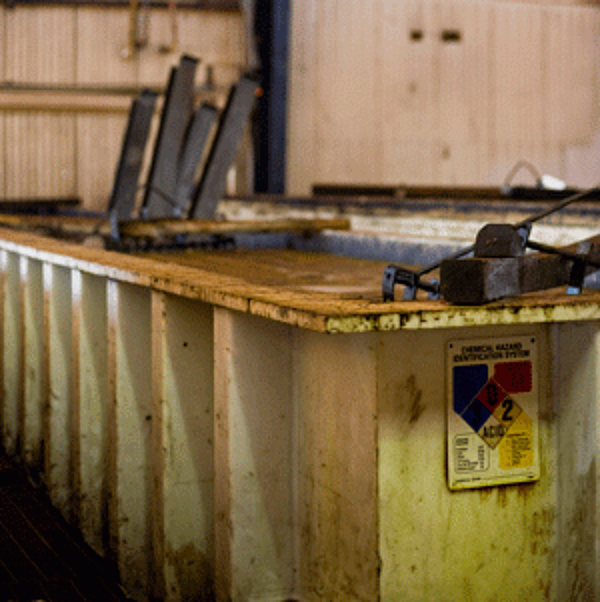
There are three steps in the galvanizing process however, surface preparation is a critical step in the application of any coating. In most instances where a coating fails before the end of its expected service life, it is because of incorrect or inadequate surface preparation.
The surface preparation step in the galvanizing process has its own built-in means of quality control because zinc simply will not react with unclean steel. Any failures or inadequacies in surface preparation will be immediately apparent when the steel is withdrawn from the zinc bath because the unclean areas will remain uncoated, and immediate corrective action can be taken.
Surface preparation consists of three steps:
- Degreasing - A hot alkali solution, mild acidic bath, or biological cleaning bath removes organic contaminants such as dirt, paint markings, grease, and oil from the metal surface. Epoxies, vinyls, asphalt, or welding slag, which cannot be removed by degreasing, must be removed before galvanizing by grit-blasting, sand-blasting, or other mechanical means.
- Pickling - A dilute solution of heated sulfuric acid or ambient hydrochloric acid removes mill scale and iron oxides (rust) from the steel surface. As an alternative to or in conjunction with pickling, this step can also be accomplished using abrasive cleaning or air blasting sand, metallic shot, or grit onto the steel.
- Fluxing - The final surface preparation step, a zinc ammonium chloride solution, serves two purposes. It removes any remaining oxides and deposits a protective layer on the steel to prevent any further oxides from forming on the surface prior to immersion in the molten zinc.
Galvanizing
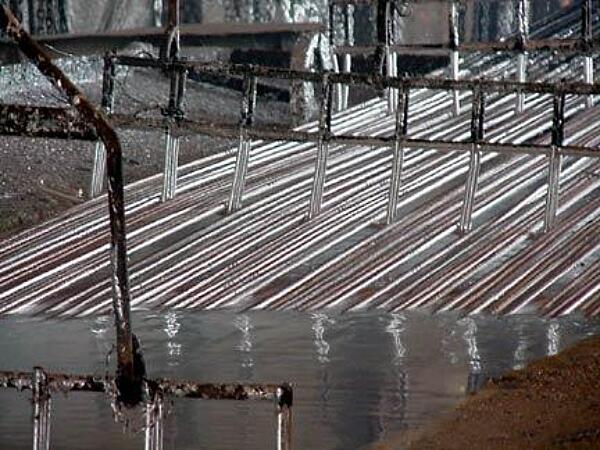
The “galvanizing” step of the process occurs when steel is completely immersed in a bath (kettle) of molten zinc. According to specification, the bath chemistry must be at least 98% pure zinc and maintained at a temperature approximately 840 F (449 C). The 2% of additives are to the galvanizers’ discretion within certain limits. The most common additives are aluminum, bismuth, and nickel – which help with things such as fluidity of the zinc, controlling coating thickness and appearance.
While immersed in the kettle, the iron in the steel reacts with the molten zinc to form a series of intermetallic (zinc/iron) alloy layers. Rather than a “surface” coating, the galvanized coating essentially becomes a part of the steel, as the metallurgically-bonded layers of the coating are tightly connected ~3,600psi. The steel will stay in the bath until it reaches bath temperature, and then is slowly withdrawn at an angle from the galvanizing bath. Excess zinc is removed by draining, vibrating, and/or centrifuging (spinning).
The metallurgical reaction will continue after the material is removed from the bath, as long as the article remains near bath temperature. Articles are cooled either by immersion in a passivation solution or water by being left in open air.
Inspection
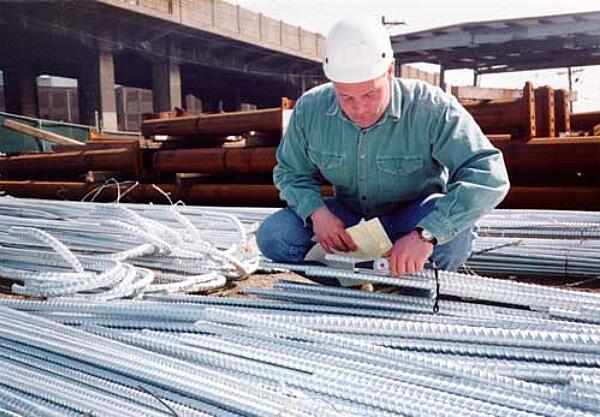
The inspection of hot-dip galvanized steel is simple and quick. The two properties of the hot-dip galvanized coating closely scrutinized are coating thickness and coating appearance. There are additional tests outlined for adherence, but these are typically only administered as a “referee” test, or when an issue is suspected.
Products are galvanized according to long established, accepted, and approved standards of ASTM, the International Standards Organization (ISO), the Canadian Standards Association (CSA), and the American Association of State Highway and Transportation Officials (AASHTO). These standards cover the minimum coating thicknesses required for various categories of galvanized items as well as finish/appearance, and adherence.
Testing methods and interpretation of results are covered in the publication, The Inspection of Products Hot-Dip Galvanized after Fabrication, as well as in our Online Inspection Course and free Inspection App. Links to all of these resources can be found on the AGA’s website. The majority of these resources is focused on visual inspection, as there are a variety of coating inconsistencies that can happen during galvanizing. The app, publication, and course examines what causes these various conditions and whether or not the acceptable according to the specifications.
Galvanized Rebar Case Study
Stoneham Arch Bridge- Stoneham, Quebec, 2012
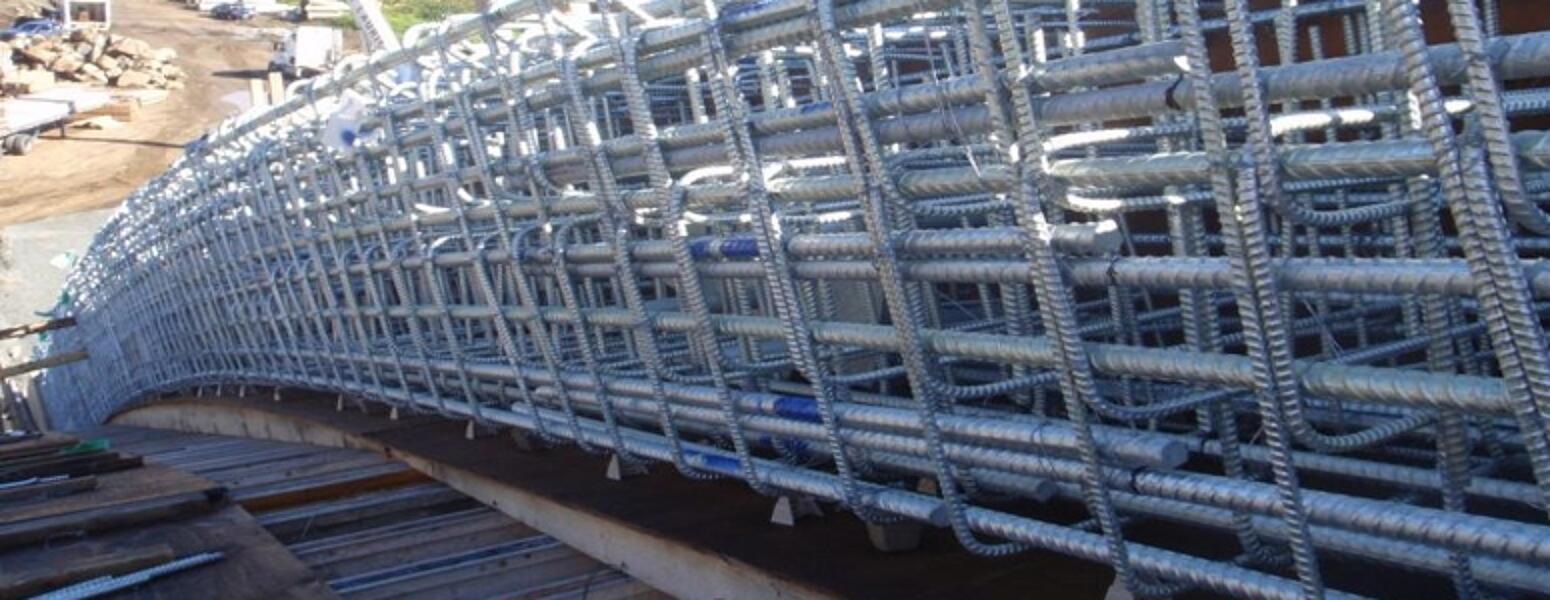
This suspended arch bridge is an aesthetically pleasing solution to a unique site requirement. The choice of hot-dip galvanized steel was preferred by the engineer because of its durability and cost compared to weathering steel in this highly corrosive environment. The resulting bridge is a beautiful and cost-effective marriage between structural steel and reinforced concrete.
The arched bridge design, unusual for a highway overpass, was chosen primarily to overcome two problems; uneven and rocky field conditions, as well as the very obtuse angle at which the road passed over the highway, which did not fit well with typical overpass construction. Steel beams were chosen for the deck because of the lower weight as compared to concrete. These beams were also designed to be galvanized rather than metallized, again, for economic and performance reasons. As for the reinforcing steel, the choice of hot-dip galvanizing was obvious since the concrete arches needed to be protected both structurally and aesthetically.
This type of bridge design, combining steel and concrete, is not often used. The unique design of this type of bridge makes it very interesting both architecturally and structurally. The use of galvanizing in all aspects of the bridge breaks new ground for our industry. Galvanized structural steel, galvanized reinforcing steel in the concrete, and even the supporting cables are galvanized (cables were supplied galvanized by the cable manufacturer).
The province of Quebec has a long history of being a leader in the use of galvanizing, going back to fully-galvanized road bridges from the early 1960s and galvanized reinforcing steel since the 1990s in road structures. The new ministry standards for an expected 75-year lifespan further drove the need for galvanizing in road infrastructure.