Durability & Bond Strength
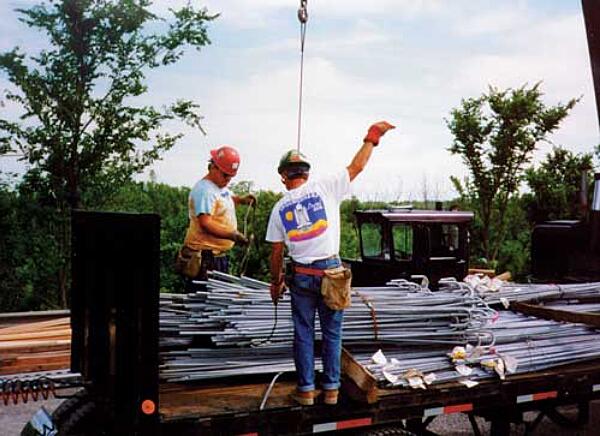
A strong metallurgical bond between the steel rebar and zinc coating is created during the galvanizing process. Galvanizing is metallurgically bonded to the steel, meaning when rebar is dropped, kicked, stepped on, or rubbed against existing concrete or other rebar pieces on the job-site, the protective coating will remain tightly adhered. This durable zinc coating will withstand the effects of UV light, temperature extremes, and exposure to rain or snow, thus protecting the rebar both while it is stored and when in use. From installation through the use phase, galvanized rebar is abrasion resistant and durable.
Abrasion Resistance
A unique characteristic of the hot-dip galvanized coating is the development of metallurgically bonded (~3,600 psi), abrasion resistant intermetallic layers. The photomicrograph below is a cross-section of a galvanized steel coating showing the three intermetallic layers (Gamma, Delta, and Zeta) and top layer of pure zinc (Eta). During the galvanizing process, these layers develop naturally during a metallurgical reaction between the iron in the steel and zinc in the kettle. As the photomicrograph also shows the hardness of each of the layers as a Diamond Pyramid Number (DPN), you can see the three intermetallic layers are harder than the base steel, while the eta layer has ductility which makes damaging the HDG coating very difficult. Hot-dip galvanizing's abrasion resistance provides unmatched protection against damage caused by rough handling during transport and erection, as well as in service. Other coatings with lower bond strengths (300-600 psi) can be easily damaged during shipment and construction, weakening their effectiveness, as barrier protection is dependent upon the integrity of the coating.
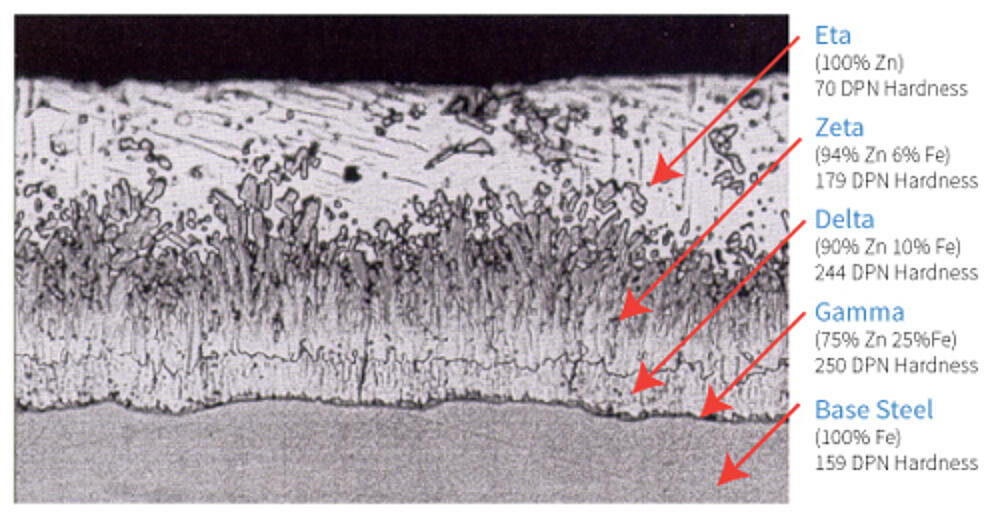
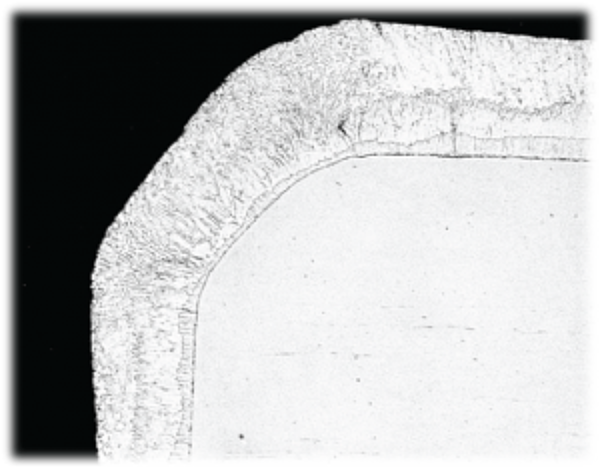
Uniform Protection
Another aspect of HDGs durability is its uniform protection. During the metallurgical diffusion reaction in the galvanizing kettle, the galvanized coating grows perpendicular to all surfaces. Therefore, the coating is naturally as thick on corners and edges as flat surfaces. Since coating damage commonly occurs at edges, added protection at these junctures is important. Brush- or spray-applied coatings have a natural tendency to thin at corners and edges leaving the part prone to attack. The uniform protection of hot-dip galvanized steel leaves no weak points for accelerated corrosion.
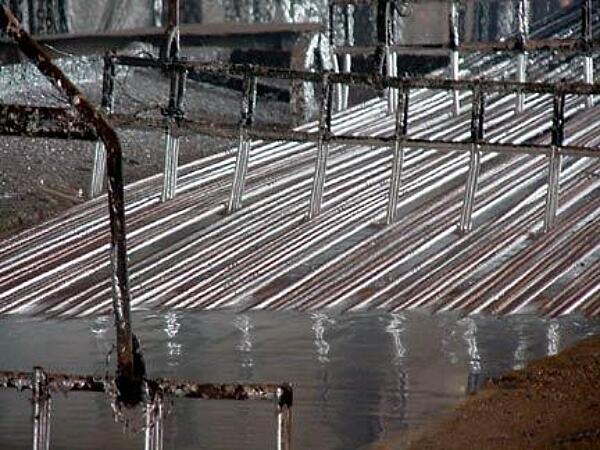
Complete Coverage
Hot-dip galvanizing is a total immersion process, meaning the steel is fully submerged into cleaning solutions and the molten zinc coating all interior and exterior surfaces. This complete coverage ensures the entire bar and all design details are coated. Fully coating bars is equally important as they are utilized at connection points which are critical to structural integrity.
Bond Strength
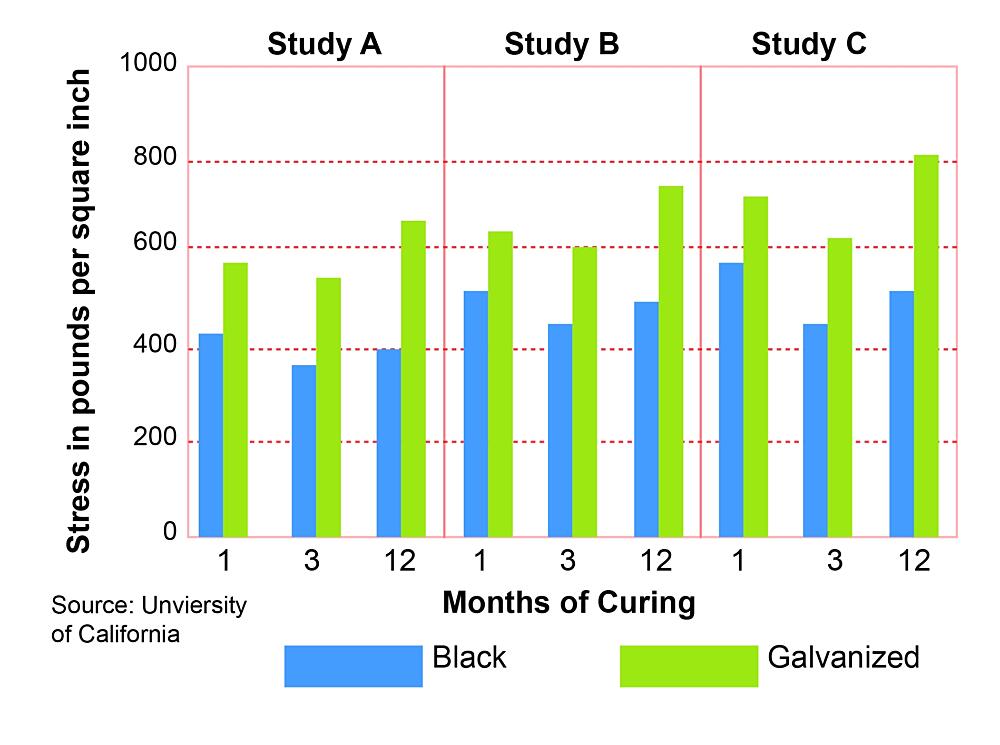
Good bonding between reinforcing steel and concrete is essential for the reliable performance of reinforced concrete structures. When protective coatings on steel are used, it is essential to ensure they do not reduce bond strength. Studies on the bonding of galvanized and black steel bars to Portland Cement concrete have been investigated.
The results of these studies indicate:
- Development of the bond between black or galvanized steel and concrete depends upon cure time and environmental factors.
- In some cases, the full bond for galvanized rebar may take longer to form than for uncoated steel, depending on the zincate/cement reaction.
- As reported by Stephen Yeomans in Galvanized Steel Reinforcement in Concrete, there are a number of studies that have concluded the fully developed bond strength of galvanized rebar has no significant difference from black rebar bond strength.
- A study by C. Andrade in Spain monitored bond strength of galvanized rebar samples over 10 years immersed in seawater and found no deleterious effects on bond strength over that time.
Durability Case Study
I-85/I-385 Gateway Project: Greenville, SC; 2018
The South Carolina Department of Transportation and their contractor, Flatiron-Zachry, have been constructing the I-85 and I-385 new intersection in Greenville, South Carolina since February of 2016. The project will improve the safety of the traveling public, increase public capacity for this interchange and create a financial boost for the economy in a very fast-growing region of this county.
The South Carolina Department of Transportation will try to improve the wintry weather road conditions using different types of ... salt. This salt can seep into the concrete and create a corrosion problem for non-coated reinforcing steel.
The scope of this project is to construct several new bridges and overpasses all while widening the lanes going to these new bridges. In total, the project will have ten bridge structures constructed, two new flyovers, some rehabilitation done to two current bridge structures, and some modification on the foundations of one existing bridge.
Hot dip galvanizing has been specified on several bridges on this I-85 corridor portion in South Carolina for many years. The reason for the hot dip specification is due to the proximity of these bridges when winter weather arrives to this South Carolina “Upstate” area. Most of the time this area of the corridor will see the creation of ice and a wintry mix of frozen rain and sleet. The South Carolina Department of Transportation will try to improve the wintry weather road conditions using different types of brine that contain salt. This salt can seep into the concrete and create a corrosion problem for non-coated reinforcing steel.
The concern for a future corrosion problem combined with the maintenance free longevity of galvanized reinforcing is the reason for this specification.