Longevity
Hot-dip galvanized steel is often utilized in some of the harshest environments imaginable, yet it provides maintenance-free longevity for decades. The corrosion resistance of hot-dip galvanizing varies according to its surrounding environments but generally corrodes at a rate of 1/30 of bare steel in the same environment. Measurements of the actual consumption rate of the coating during the first few years of service provide good data for projecting a conservative estimate for the remaining life to first maintenance.
When embedded in concrete, hot-dip galvanized steel can withstand the different corrosive elements and fulfill the intended design life. More information about hot-dip galvanized steel's longevity in various environments can be found in the AGA's publication Performance of Hot-Dip Galvanized Steel Products.
Zinc's Initial Reaction in Fresh Concrete
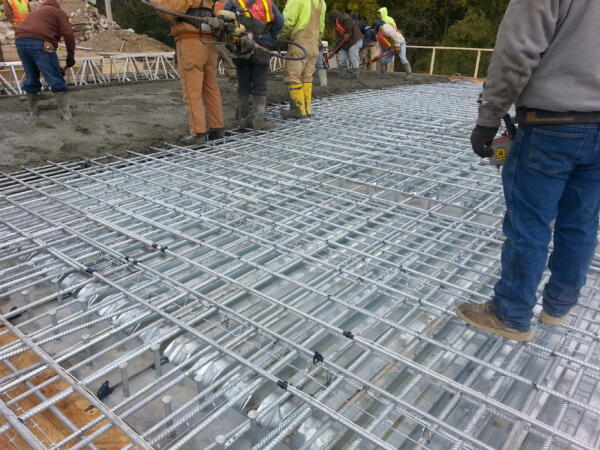
During curing, the galvanized surface of steel reinforcement reacts with the alkaline cement paste to form stable, insoluble zinc salts accompanied by hydrogen evolution. This has raised the concern of the possibility of steel embrittlement due to hydrogen absorption. Laboratory studies indicate liberated hydrogen does not permeate the galvanized coating to the underlying steel and the reaction ceases as soon as the concrete hardens.
ASTM A767 requires hot-dip galvanized reinforcement be chromate passivated after galvanizing. Many cement mixtures contain small amounts of chromate that may serve the same purpose as chromate passivating the zinc coating. The reaction between the alkaline cement paste and the zinc coating is dependent on the amount of zinc-coated surface in the concrete with the potential for reaction increasing with more zinc metal in contact with the concrete.
Zinc reacts with wet concrete to form calcium hydroxyzincate accompanied by the evolution of hydrogen. This corrosion product is insoluble and protective of the underlying zinc (provided that the surrounding concrete mixture is below a pH of about 13.3). Research has shown that during this initial reaction period until coating passivation and concrete hardening occurs, some of the pure zinc layer of the coating is dissolved. However, this initial reaction ceases once the concrete hardens and the hydroxyzincate coating has formed. Studies of galvanized rebar recovered from field structures indicate that the coating remains in this passive state for extended periods of time, even when exposed to high chloride levels in the surrounding concrete.
For concretes of high pH, or where some background chlorides are expected, the zinc surface can be passivated, using a range of proprietary post treatments, as a safeguard against excessive hydrogen evolution that may, in serious cases, reduce the pullout strength of the bar. For normal concrete conditions, research has shown no statistical difference in bond strength between galvanized rebar that was passivated and not passivated.
Chloride Concentration vs. Time
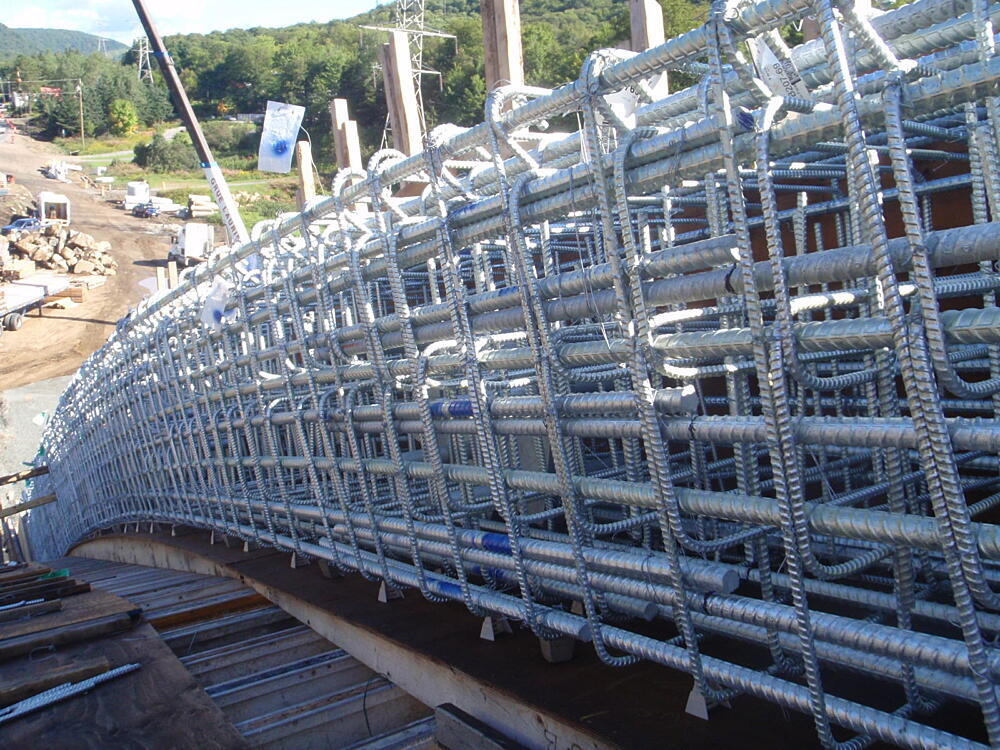
Concrete is an extremely complex material. The use of various types of concrete in construction has made the chemical, physical, and mechanical properties of concrete and its relationship to metals a topic of ongoing studies. Reinforcing steel bars (rebar) are embedded in concrete to provide strength and are critical to the integrity and performance of the structure throughout its life. As concrete is a porous material, corrosive elements such as water, chloride ions, oxygen, carbon dioxide, and other gases travel into the concrete matrix, eventually reaching the rebar.
Concrete reinforcement begins to corrode when the concentration of chloride ions at the reinforcing bar surface exceeds the threshold for the bar material. For uncoated rebar, that threshold is 0.95 kg/cubic meter. For rebar coated with zinc, the threshold is an average of 4X the threshold for uncoated bar or 3.80 kg/cubic meter.
This graph shows the buildup of chloride ions over time for two bridges; one from a northern climate where road salts are the main source of chloride ions and one from a southern climate where natural salts from the ocean are the source of chloride ions. The high threshold for zinc coatings and the slow buildup of chloride ions means the corrosion of the zinc coating doesn’t even begin for many decades and of course the substrate carbon rebar remains structurally intact. So, it is important to emphasize the galvanized rebar IS NOT the cause of concrete cracking and spalling of the concrete. Only after about 100 years and the complete corrosion of the zinc does the carbon rebar itself corrode and then lead to concrete failure.
Because failure of the rebar leads to compromised or failing structural capacity, protecting against premature rebar failure is key. Similar to in the atmosphere, galvanized rebar extends the life of the steel in concrete.
The total life of galvanized steel in concrete is made up of the time taken for the zinc to depassivate, plus the time taken for consumption of the zinc coating, as it sacrificially protects the underlying steel. Only after the coating has been fully consumed in a region of the bar will localized steel corrosion begin. Laboratory data support, and field test results confirm, that reinforced concrete structures exposed to aggressive environments have a substantially longer service life when galvanized rebar is used as opposed to bare steel rebar.
% Coating Degredation vs. Time
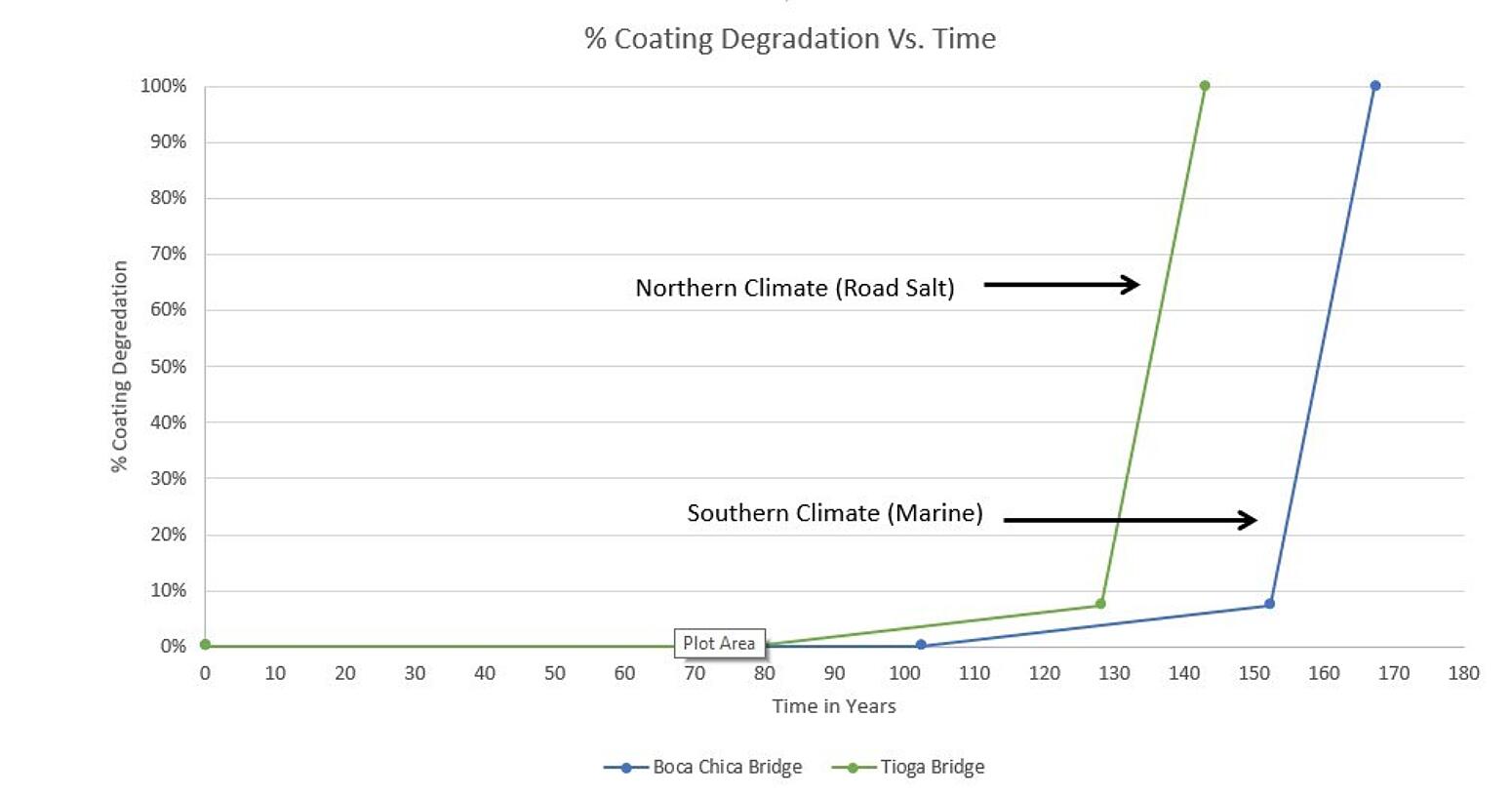
Chloride Concentration vs. Time
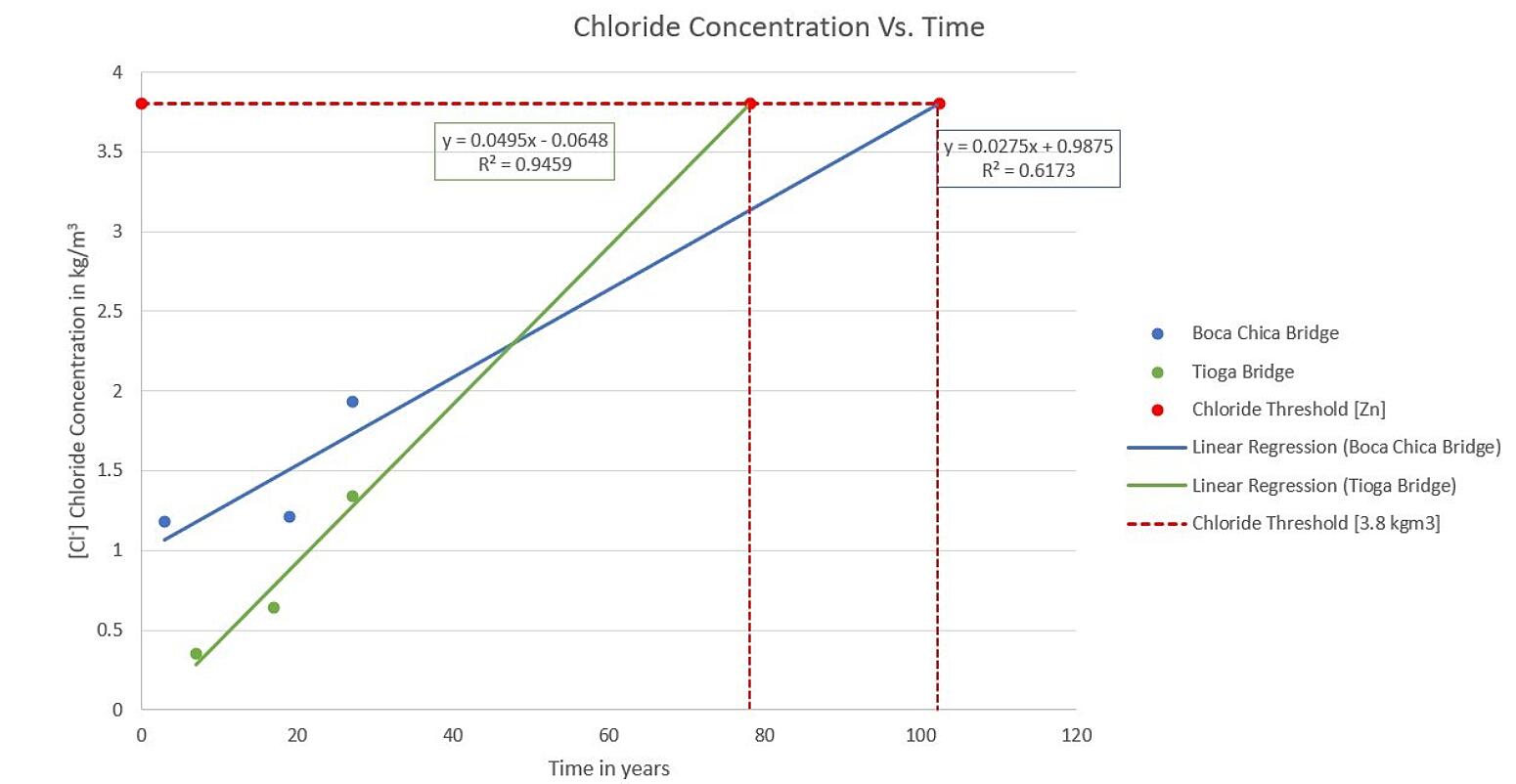
As stated in the previous slide, once the chloride ion threshold is exceeded, the zinc coating begins to corrode. The corrosion rate of the zinc in concrete has been studied and is approximately 3 microns/year. This corrosion rate depends on many factors; the amount of moisture in the concrete, the wet/dry cycles, the cracks in the concrete, the concrete cover thickness, and additives to the concrete mix are the most important factors. The total time for the zinc to corrode is also very dependent on the initial zinc coating on the reinforcing bar. Once the zinc has completely corroded, the steel becomes exposed to the chloride ions and begins the final cycle of corrosion where the steel turns into rust (iron oxide) and, eventually causes the concrete to spall.
For the two bridges cited in the graph above, (and as you can see one is located in a northern U.S. climate where substantial road salts are used, and the other in a marine environment where the chloride source is the ocean air and wind initiated spray) based on coring samples taken over the past 25 years, the chloride ion threshold will not be reached until year 78 and 102, respectively. (see the intersection of the lines with the X-axis) Then, the zinc corrodes at about 3 microns per year until it is completely consumed, roughly at year 128 and 153, respectively. Then, the steep slope of the curve begins, which indicates carbon steel corrosion.
Accelerated Testing
Efforts have been made in many zinc-coated steel applications to develop the correct test method to determine a proper "accelerated" lifetime. One test for corrosion prevention systems in the United States is ASTM B117. ASTM Committee G-1 on Corrosion of Metals has jurisdiction over the salt spray standards B117 and G85. The Committee passed the following resolution regarding the use of B117: "ASTM Committee G-1 on the Corrosion of Metals confirms that results of salt spray (fog) tests, run according to ASTM standard designation B117, seldom correlate with performance in natural environments. Therefore, the Committee recommends that the test not be used or referenced in other standards for that purpose, unless appropriate corroborating long-term atmospheric exposures have been conducted. ASTM B117 and B368 are best used as quality control tests assuring that the day-to-day quality of products and manufacturing processes are optimized. There are a number of other corrosion tests which can be used for predicting performance in service."
Salt spray tests cannot be used to accurately test zinc-coated steel because they accelerate the wrong failure mechanism. Without a proper wet/dry cycle, the zinc coating cannot form patina layers. The absence of a patina layer allows constant attack of the zinc metal and gives a very low prediction of the zinc coating lifetime. Core testing has been shown to provide the most accurate results for the performance of galvanized rebar embedded in concrete.
Longevity Case Study
Athens Bridge- Athens, PA, 1973
The Pennsylvania DOT has specified galvanized reinforcement for decades. One such bridge, the Athens Bridge, built in 1973, is an eleven-span, four-lane, divided bridge utilizing hot-dip galvanized reinforcing bars. The Athens bridge deck was initially inspected eight years after installation. Concrete cores were drilled and an analysis of chloride contamination and coating thickness was conducted. The chloride levels found in the cores exhibited concentrations between 1.8 to 7.9 lbs/yd3 of concrete. The high end of these concentrations is well above the threshold for active corrosion to occur on bare steel. Despite these extremely corrosive conditions, the coating thickness measurements indicated galvanized coatings in excess of 15 mils (approximately three times the coating thickness required on newly-galvanized rebar according to ASTM A 767).
The Athens Bridge was later inspected in 1991 and 2001, and the analysis generated similar results. No sign of active corrosion on the galvanized reinforcement was found and coating thickness measurements reported were in excess of 10 mils. These current coating thicknesses indicate an estimated 40-plus years of additional maintenance-free corrosion protection.