Corrosion Protection
Steel is an abundant, efficient building material that provides specifiers design freedom. However, for steel embedded in concrete, it is critical to coat the steel for corrosion protection. Large construction projects often target a 75-125 year design life, highlighting the need for durable, long lasting corrosion protection. Hot-dip galvanizing (HDG) provides superior corrosion resistance to reinforcing steel through its barrier protection, cathodic protection, and a high chloride threshold.
The first line of corrosion defense is barrier protection. Like paints, the hot-dip galvanized coating provides protection by isolating the steel from the electrolytes in the environment. As long as the barrier is intact, the steel is protected and corrosion will not occur. However, if the barrier is breached, corrosion will begin.
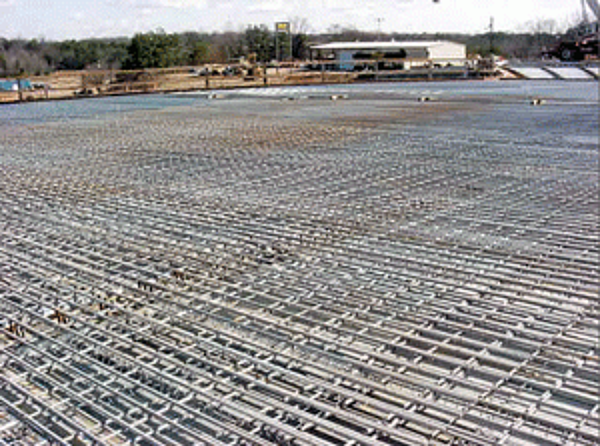
Because a barrier must remain intact to provide corrosion resistance, two important properties of barrier protection are adhesion to the base metal and abrasion resistance. The tightly-bonded, impervious nature of zinc metal makes it a very good barrier coating. Coatings such as epoxy that have pin holes are susceptible to penetration by elements causing under-film corrosion to spread rapidly.
In addition to barrier protection, hot-dip galvanizing protects steel cathodically, which means zinc will preferentially corrode to protect the underlying base steel
The Galvanic Series of Metals is a list of metals arranged in order of electrochemical activity in seawater (the electrolyte). This arrangement of metals determines what metal will be the anode and cathode when the two are put in an electrolytic cell. Metals higher on the list are anodic to the metals below them meaning they provide cathodic or sacrificial protection when the two are connected. Therefore, zinc protects steel. In fact, this cathodic protection ensures even if the HDG coating is damaged to the point bare steel is exposed (up to ¼ inch in diameter), no corrosion will begin until all the surrounding zinc is consumed.
Zinc reacts with the pour water of the concrete to form compounds that protect the metal surface from further corrosion after the concrete dries. The compounds also delay the start of depassivation by not allowing chlorides to reach the metal surface.
High Chloride Initiation Threshold
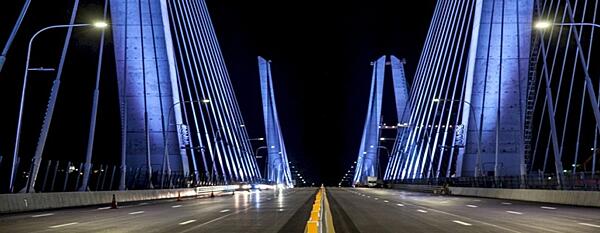
The corrosion mechanisms and performance of hot-dip galvanized steel in concrete are different than when exposed in atmospheric conditions. Steel embedded in concrete is exposed to a highly alkaline environment. Black steel is passive in alkaline concrete until the chloride level exceeds approximately 1 lb/yd3, when steel becomes depassivated and starts to corrode. Zinc, on the other hand, can withstand chloride concentration 2-4 times higher than black steel, and coupled with its impervious barrier protection, delays the onset of chloride corrosion on galvanized rebar.
Chlorides penetrate the concrete through small pores and cracks that form on the surface through use and weathering. While black steel in concrete typically depassivates below a pH of 11.5, galvanized reinforcement can remain passivated at a lower pH, thereby offering substantial protection against the effects of concrete carbonation.
Corrosion Product Migration and Concrete Matrix Densification
In addition to the higher chloride tolerance, once the zinc coating does start to depassivate, the zinc corrosion products formed are less voluminous than iron oxides and actually migrate away from the galvanized bar into the matrix of the concrete. Unlike the development of iron oxide, the migration of the zinc corrosion products from the rebar prevents the pressure buildup and eventual concrete spalling.
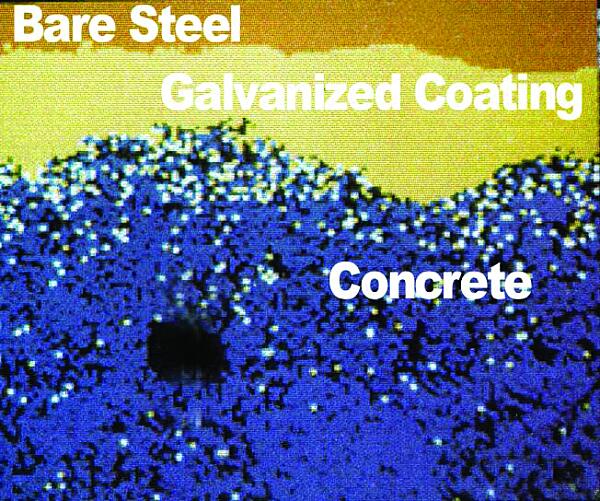
Zinc's corrosion products are loose, powdery minerals that are less voluminous than iron corrosion products and are able to migrate away from the galvanized rebar surface into the adjacent concrete matrix. As a result, corrosion of the zinc coating causes very little physical disruption to the surrounding concrete. The elemental map (left) is evidence of this migration. The white spots in the concrete indicate zinc oxide which has migrated away from the galvanized rebar/concrete interface.
There is also evidence to suggest that the diffusion of zinc's corrosion products helps fill pore spaces at the concrete/rebar interface, making this area less permeable and helps to reduce the transport of aggressive species such as chlorides through this interface zone to the zinc coating. The reactions between zinc and concrete, and the resulting corrosion product diffusion, also explains why galvanized rebar has such good bond strength with concrete.
Corrosion Protection Case Study
The Reef- Southampton, Bermuda, 2008
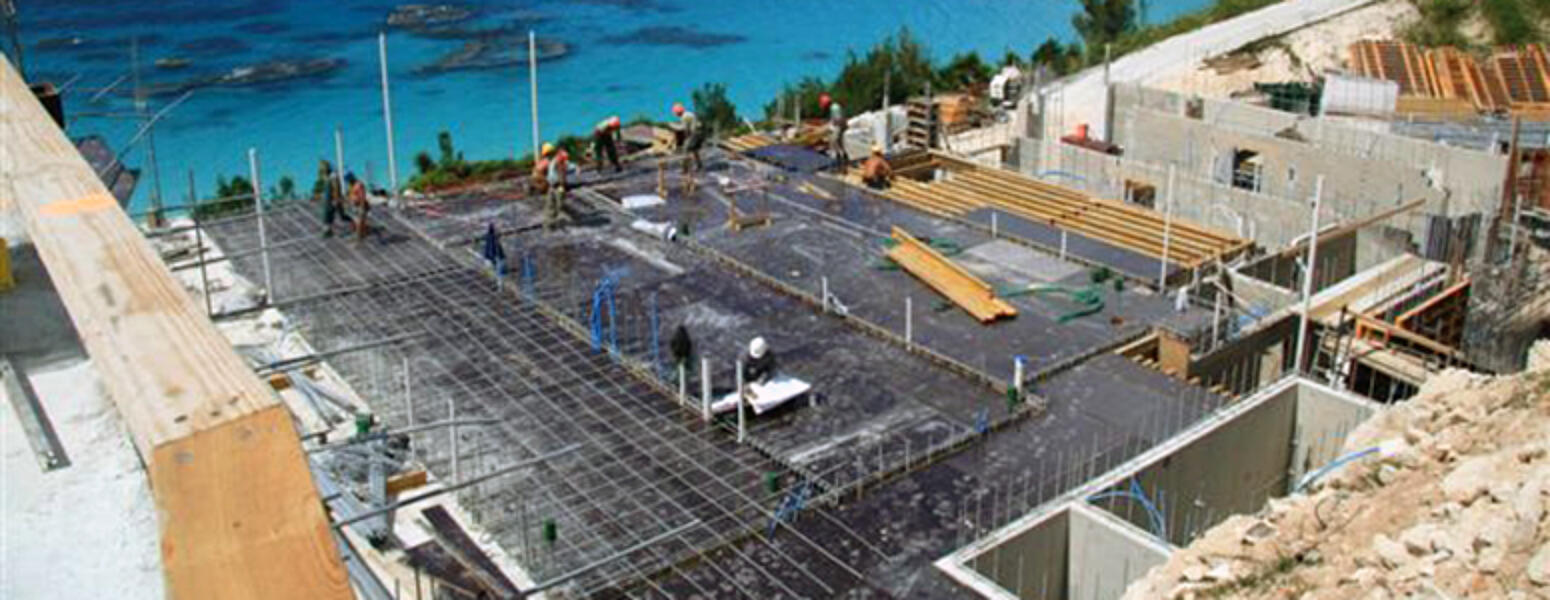
Nestled in the midst of a tropical paradise, the Reef Plaza is also subject to one of the most corrosive environments imaginable. The aquamarine waters and sunny beach location of the concrete plaza floor are susceptible to harsh sun, beating rains, and briny saltwater - making the steel rebar within the concrete susceptible to aesthetic and structural damage such as cracking and spalling. By utilizing hot-dip galvanized steel rebar, the architect of the project was protecting the plaza from the inside out. The rebar will be protected from the nicks and scratches acquired during handling, meaning the pieces will enter the concrete ready to protect against the rust and corrosion that can cause spalling. Galvanized steel rebar will keep this plaza structurally safe and aesthetically pleasing for many years of tropical delight.