Why Protect Rebar?
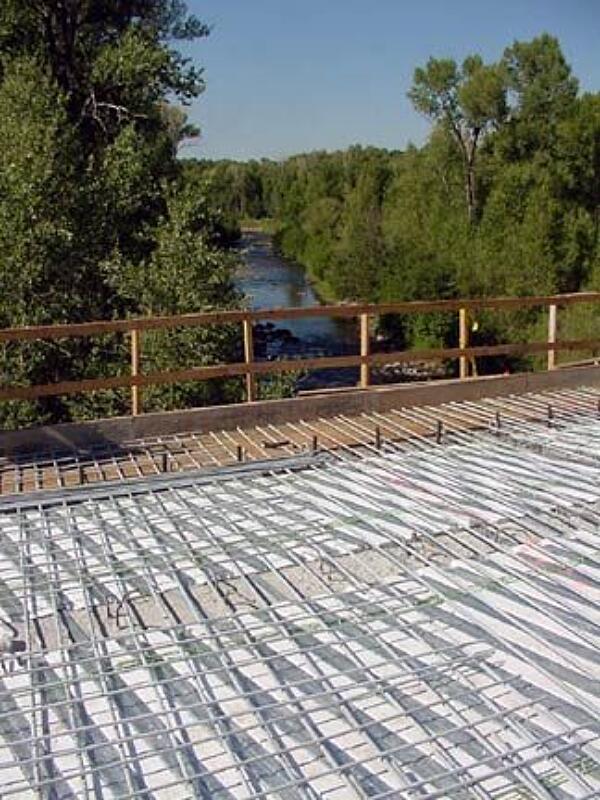
Reinforcing steel, or rebar, is used in bridges, buildings, and foundations to increase the strength of a concrete structure. Concrete is weak in tension, but steel is strong in both tension and compression, providing concrete to provide better resistance to cracking and provides longer life.
The development of reinforced concrete allowed for thinner, less-supported slabs and speedier construction; however, one thing that was not foreseen when its use became wide-spread was the potential for deterioration of the steel rebar within and its impact on the concrete structure. In fact, corrosion of reinforcement is likely the most common cause of concrete deterioration and failures. Let’s take a moment to understand how corroding rebar affects concrete structures.
Steps of Rebar Corrosion
This is a pictorial view (below) as if the concrete and unprotected rebar were sliced so that we can take a look inside. As the unprotected rebar begins to corrode, iron oxides (corrosion by-products) form. Iron oxides have a greater volume than the metal ions released from the rebar; thus, the increased volume from the iron oxides causes pressure on the surrounding concrete. To relieve this increased stress or pressure, the concrete will crack. At first the cracks will be minute, only noticeable by the staining color rising to the surface of the concrete covering.
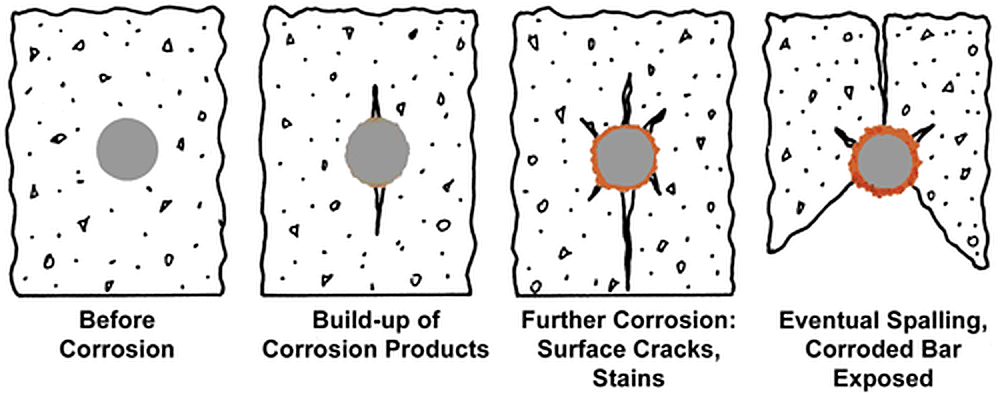
As the corrosion continues, a snowball effect is created. More cracks allow more electrolyte solution to reach the reinforcing steel, thus causing more corrosion and build-up of iron oxides, which causes more pressure and more cracks, and so on an so on. The cracks will enlarge, eventually leading to spalling of the concrete.
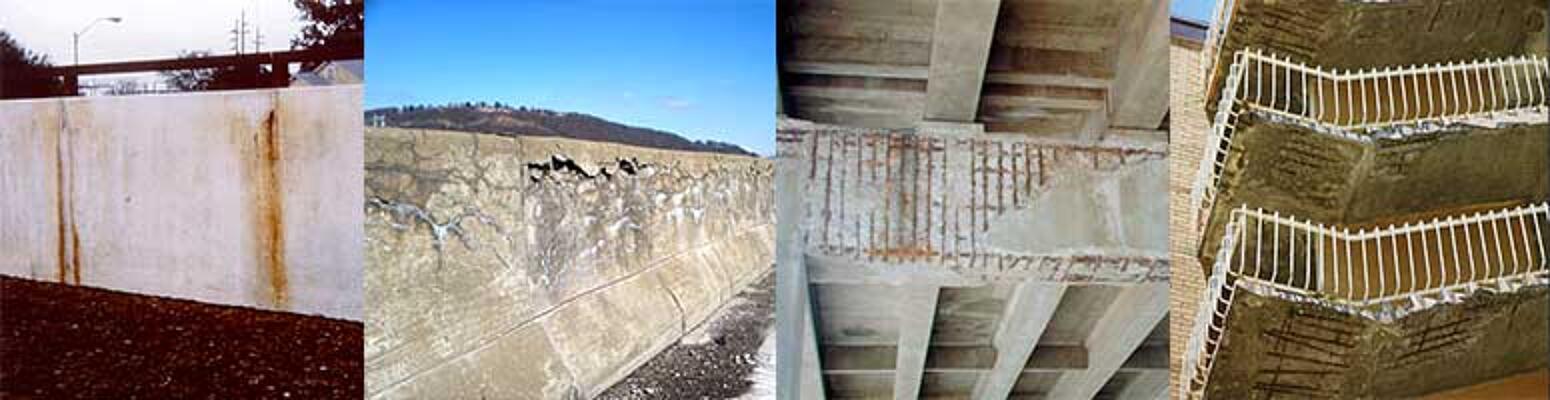
Now that you understand how the corrosion of rebar occurs, let’s examine how those steps show themselves in the real world. While rust colored staining is the first visible sign of corrosion, it’s more than just an aesthetic problem. Once staining and cracking occur, there is an easy path for more moisture to reach the steel creating more iron oxides and accelerating the corrosion process. Depending on the thickness, porosity and initial cracking of the concrete cover, this type of staining may be evident in a year or less, with spalling to follow in the next couple of years. Spalling occurs parallel to the rebar. The first signs of spalling indicate the structural integrity of the concrete is rapidly deteriorating.
Conquering Corrosion
The deterioration of reinforced concrete structures, such as bridges, is estimated to cost more than $20B annually. Increasing by nearly $500 million each year, spalling and concrete deterioration has become a major liability for highway agencies. There is, however, a way to protect these infrastructure investments from the ravages of corrosion. Using hot-dip galvanized steel rebar for corrosion protection in concrete bridge elements, such as decking, piers, or piles, ensures they will resist spalling and stand strong for generations.
Addressing corrosion after construction is expensive and disruptive as all or part of the structure needs to be closed periodically for maintenance and repair. Failure to properly address corrosion can also lead to catastrophic structural failures with potentially deadly consequences. Many of these costs and safety issues are avoidable if the potential for corrosion is minimized during construction through proper design and material selection. This is especially critical for the reinforcing steel and the structural steel connectors used to strengthen and join concrete sections. Galvanizing, the process where steel parts are immersed in a bath of molten zinc, has a proven track record and should be your first choice in corrosion protection—because it works.
Corrosion Failure Case Study
Veterans Memorial Bridge- West Virginia & Ohio, 1990
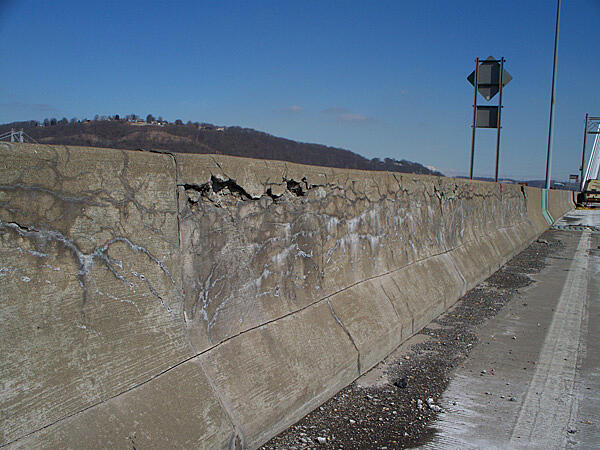
The Veterans Memorial Bridge, which spans the Ohio River connecting Weirton, West Virginia and Steubenville, Ohio, opened on May 1, 1990. The bridge is an example of what can happen when reinforcing steel fails to withstand the environment in which it is placed. These photos were taken in February 2009, and after less than 20 years in service, the rebar has corroded, leading to cracking and spalling of the concrete. Utilizing rebar able to withstand the moist river environment and damaging winter road salts would have kept the concrete intact, greatly reducing the economic and time concerning burden required to repair and replace the spalling concrete.