Safety
Engineered Consistency
One of the biggest advantages of using galvanized steel in utility projects is its consistency in strength rating. In comparison to other materials, such as wood, steel is manufactured and engineered to a very strict specification. Wood is a harvested product, which contains varied grain patterns, knots and other imperfections.
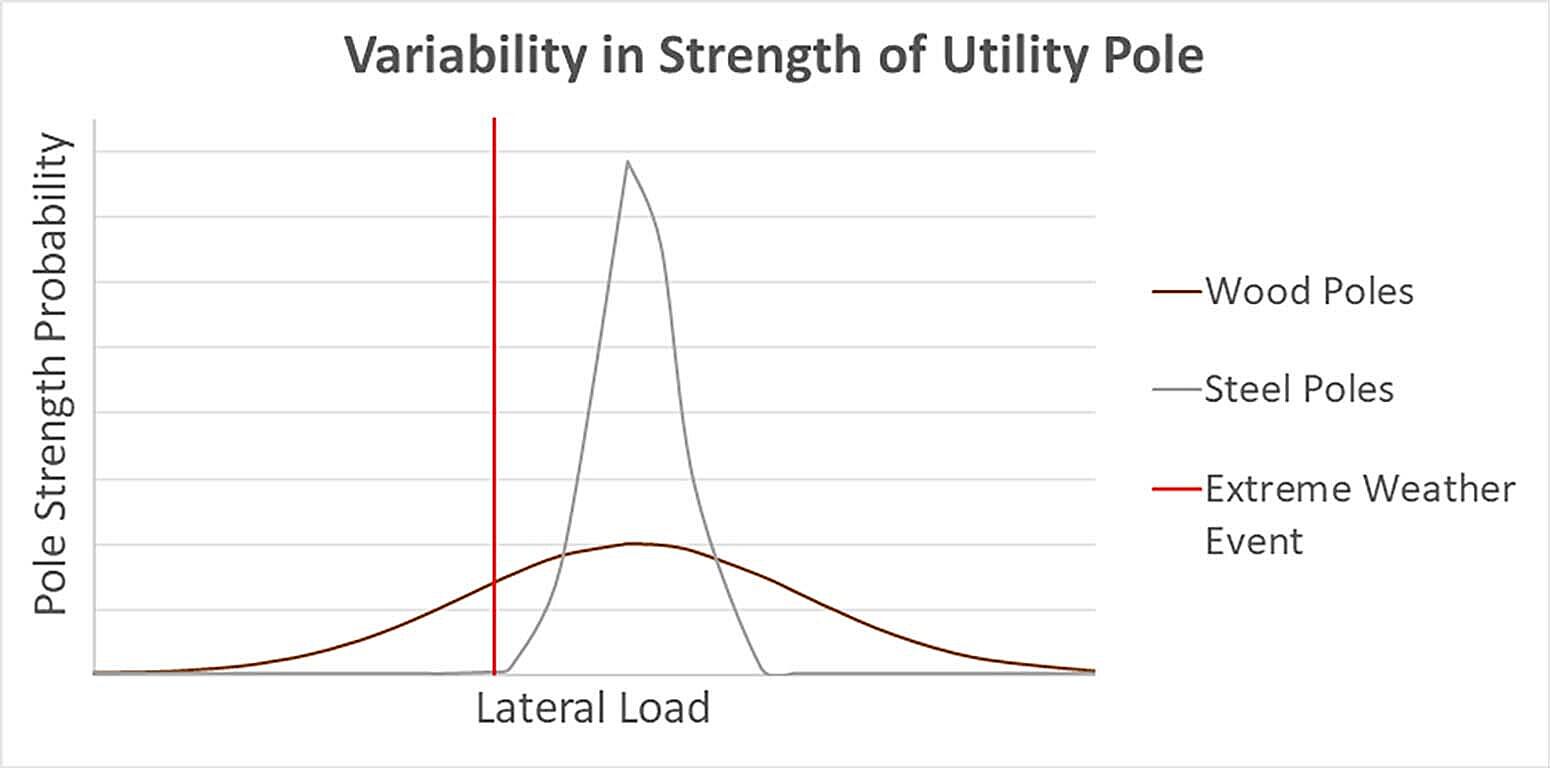
The graph represents the range in strength of utility poles you can get for a certain size. With any product there is always some variability from pole to pole on its strength. You can see from the wood line the range of strength a pole can handle is much larger compared to steel due to the difference created in wood being a harvested product. This variability becomes a problem when you see larger loads or when you're approaching the design limit of each pole. Given that for most extreme weather events will be near the limits of the designed strength rating, more poles and structures will be able to withstand these events.
You may see a similar graph to this given by someone in the wood industry stating variability is a good thing. They point to the fact that a small percentage of poles has a much larger strength rating then was specified. What fails to be taken into account is that similar percentage will have a strength rating much lower then specified, which can create safety and reliability issues.
Safety: Failure Method
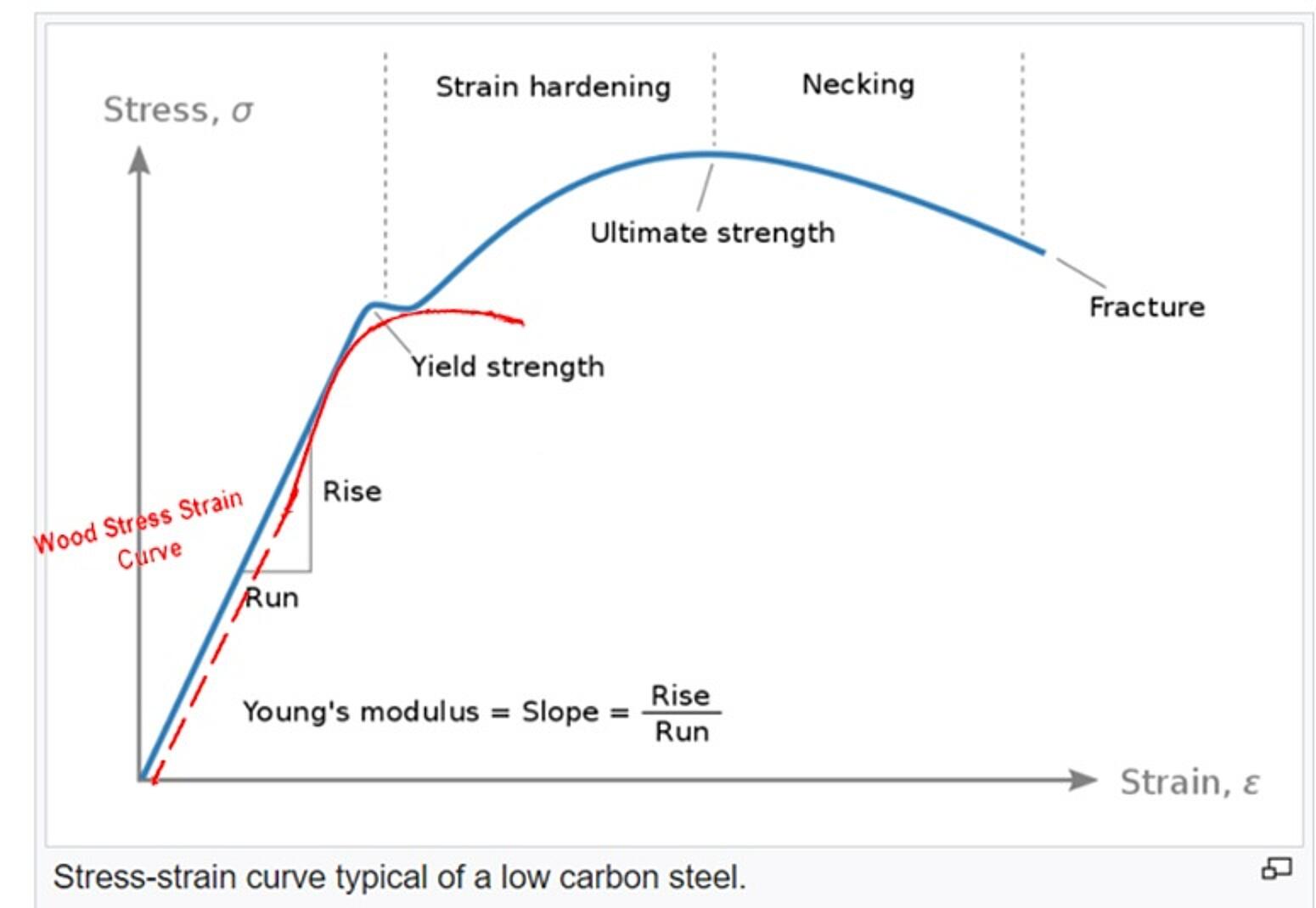
An unfortunate fact of much of our infrastructure is some of it may fail, especially that which is close to roadways or handles extreme weather events. Fortunately the failure method of steel infrastructure creates a much safer failure event compared to alternative materials.
To understand the benefits of steel’s failure method it helps to understand the relationship of stress and strain of a material as well at its yield strength. The graph above is a strain stress chart for a typical low carbon steel. To allow easier comparison of the stress/strain relationship of poles made from different materials, and engineered to the same strength rating/standard, the stress strain graphs have been scaled to overlay each other. This is a simplification but will make it easier to compare how each material acts near during extreme loading event and material failure. As strain increases, the stress a material can handle increases until you get to a dip point, which is the yield strength. Once a material experiences stress beyond its yield strength the material deforms and no longer will return to its normal shape. When a material experiences a stress before the yield point, the material will return to normal after the stress is removed with no change. Due to this, most materials are designed to have their working loads below their yield strength.
Now that you understand a material’s yield strength in relation to stress and strain you can now really understand how steel shines. When we add the stress strain relationship of wood, which has been scaled to the same size of steel for comparing poles and structures designed to the same load requirements, you can see there is not a lot more stress after yielding that the material can handle. When a wood structure is loaded past their yield strength the material fractures/ breaks at a much lower stress/force. When a steel structure is loaded past its yield strength it first experiences strain hardening which can withstand much higher stresses then necking/ deformation and then finally fails. This range of failure allows for a much larger stress/ load to be applied before a structure or power line comes down.
Safety: Failure Method Crash Test
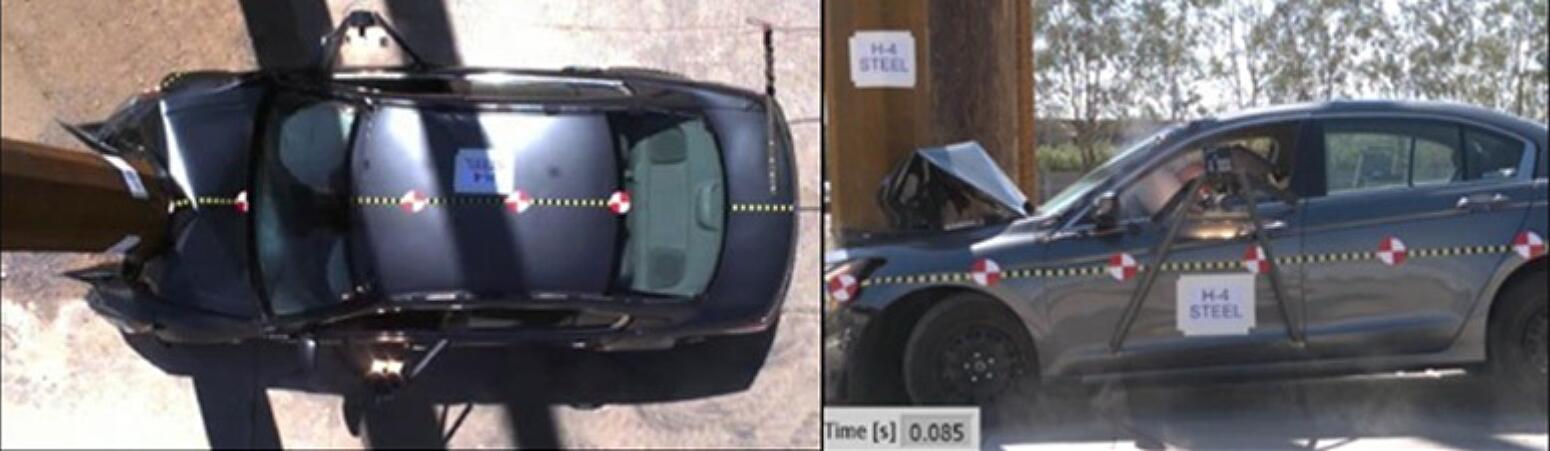
Let's examine the effects of a popular passenger vehicle crashing into a transmission-class pole that was performed in 2018 by Potomac Electric Power Company (PEPCO).
The most frequently registered passenger vehicle from 2010 to 2014 in the service territory of Pepco Holdings (Delaware, Maryland, New Jersey and Washington, DC) was used in the test. The vehicle was driven at 36mph into a 69kv steel structure (80’ H4 Class pole). The crash caused a 3-inch deep dent in the pole with the several flats of the pole buckled inward and permanent damage to the front of the vehicle. Based on the recorded data from the sensors on the ATDS, the neck injury index was below the published Injury Assessment Reference Values (IARVs), which represents a low risk of serious injury. Even though the pole was damaged and will need to be replaced it still kept the power line up and inflicted nonlife threatening injuries to the crash test dummy from the crash. If the pole would have toppled, a 69 KV line would be extremely hazardous and potentially fatal.
Safety Case Study
Carbon Power and Light
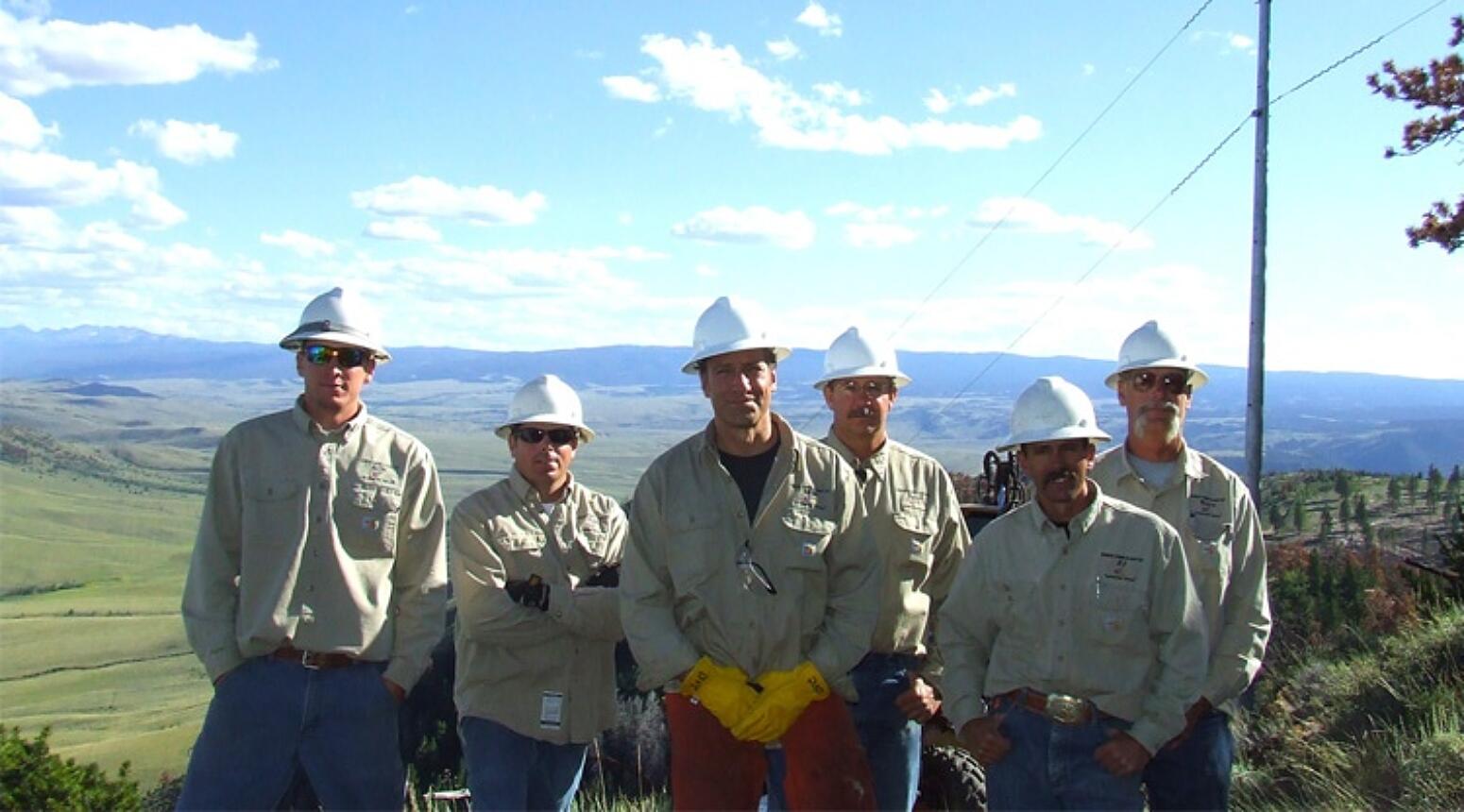
Carbon Power and Light provides power to approximately 6100 customers in several small towns on the Wyoming/Colorado border as well as the outlying areas around Laramie. At the cooperative, their number one priority is system safety.
The integration of steel distribution poles into the utility’s distribution system in the 1990s has been a very positive change for the cooperative. The cooperative only installs steel polls and now has over 4600 steel distribution poles in its system, which equates to 14.5 percent of the CPL distribution system. They install 300-400 steel polls a year on their 4500 square miles of territory. This percentage continues to rise as steel is now used for all new poles and replacement poles at CPL.
Steel poles are expected to last up to 80 years. Additionally, the poles require minimal maintenance. Steel poles may cost more, but the benefits outweigh the initial cost difference. Steel helps CPL to create a more reliable system. So overall, the life cycle cost is better with steel.