Durability
Another aspect of hot-dip galvanizing is it is an extremely durable material which benefits many different power markets.
Abrasion Resistance
A unique characteristic of the hot-dip galvanized (HDG) coating is the development of tightly-bonded (3,600 psi), abrasion resistant intermetallic layers. The photomicrograph (below) is a cross-section of a galvanized steel coating showing the three intermetallic layers (Gamma, Delta, and Zeta) and top layer of pure zinc (Eta). During the galvanizing process, these layers develop naturally during a metallurgical reaction between the iron in the steel and zinc in the kettle. The photomicrograph also notes the hardness of each of the layers as a Diamond Pyramid Number (DPN). As you can see, the three intermetallic layers are harder than the base steel, while the eta layer has ductility which makes damaging the HDG coating very difficult.
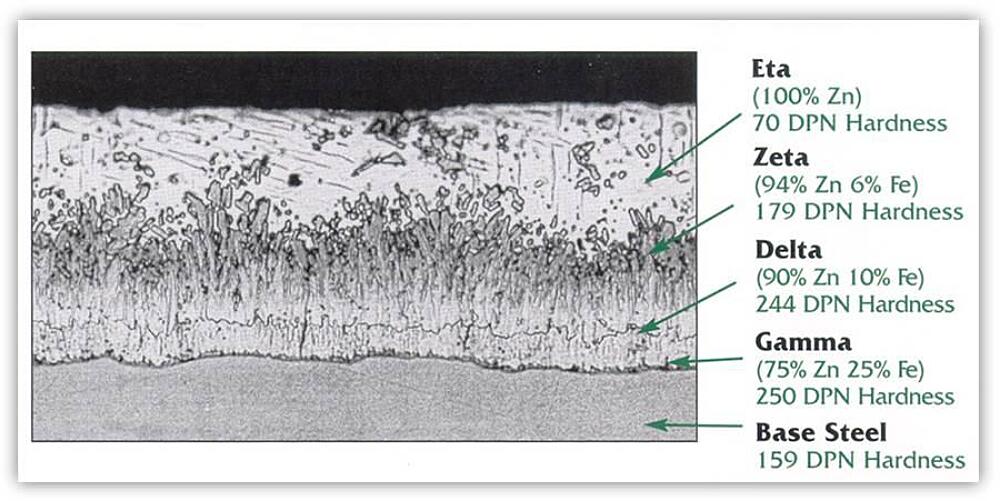
HDG's abrasion resistance is beneficial in several power markets. For instance, in coal generation, there are jagged, hard coal rocks moving through the plant on conveyor belts, into hoppers and chutes, etc. which could easily scratch or nick coatings with less bond strength. Other corrosion protection systems, such as paint only have bond strength of 300-600 psi. Wind generation similarly can be very abrasive to the turbines and ancillary structures. Harnessing wind to generate power is inherently abrasive as wind carries sand, dirt, and other debris and the towers are often in remote locations without constant access for inspection, which means damaged coatings could go unnoticed. The abrasion resistant intermetallic layers of hot-dip galvanizing can withstand these daily rigors without damage or maintenance.
Uniform Protection
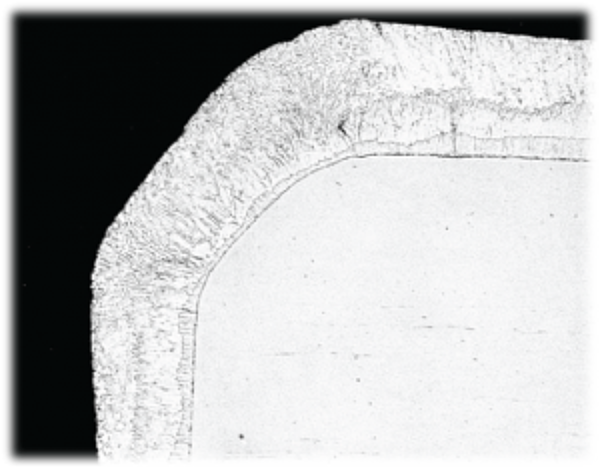
During the metallurgical diffusion reaction in the galvanizing kettle, the galvanized coating grows perpendicular to all surfaces. Therefore, the coating is naturally as thick on corners and edges as flat surfaces. Since coating damage commonly occurs at edges, added protection at these junctures is important. Brush- or spray-applied coatings have a natural tendency to thin at corners and edges leaving the part prone to attack. The uniform protection of hot-dip galvanized steel leaves no weak points for accelerated corrosion.
Complete Coverage
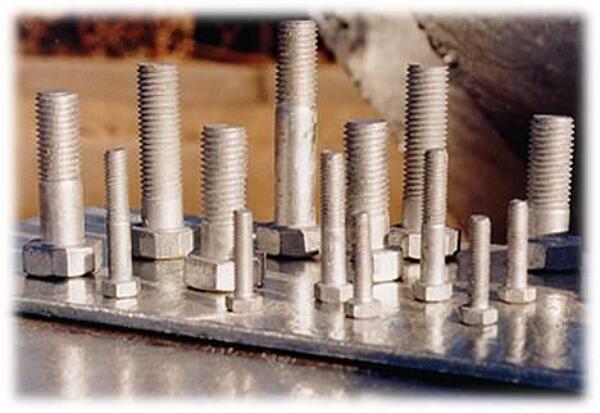
Hot-dip galvanizing is a total immersion process meaning the steel is fully submerged into cleaning solutions and the molten zinc coats all interior and exterior surfaces. This complete coverage ensures even the insides of hollow and tubular structures and the threads of fasteners are coated. As corrosion tends to occur at an increased rate on the inside of hollow structures where humidity and condensation occur, interior coverage is very beneficial. Hollow structures that are painted have no corrosion protection on the inside. Fully coating fasteners is equally important as they are utilized at connection points which are critical to structural integrity.
Many hollow structures are pertinent to the distribution of power, namely transmission and distribution poles. There are thousands of poles in each power companys' jurisdiction and many are in remote or inaccessible locations making inspection difficult. Providing equal protection on the inside of these poles will stave off sneaky interior corrosion and extend the life of these critical elements of the power grid.
Durability Case Study
Canaport - Saint John, NB, 2008
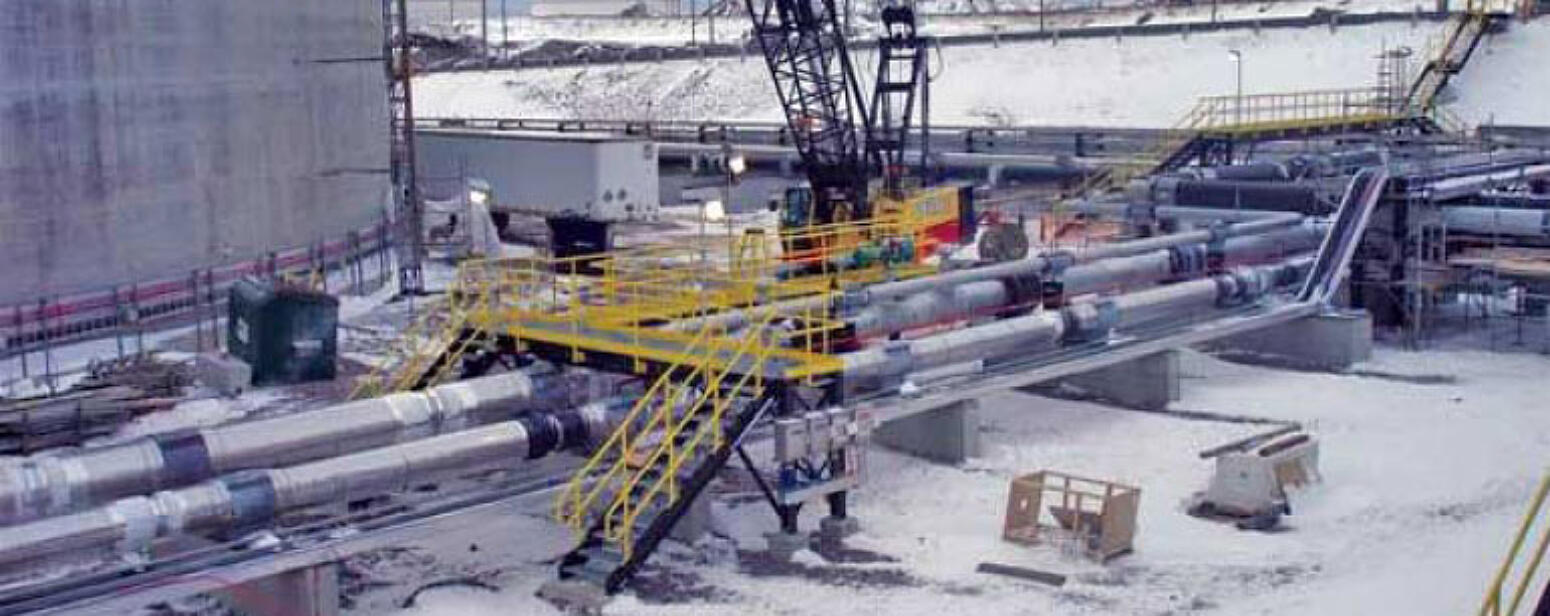
The unforgiving environment of the northern Atlantic coast, replete with strong winds, salt water, and extreme winter conditions, makes the area primed for corrosion. Utilizing hot-dip galvanized steel throughout the Canaport Liquid Natural Gas (LNG) regasification plant will combat such corrosive elements with a superior system of cathodic and barrier protection.
Reaching approximately 1,650 feet into the Atlantic Ocean, the port serves as a safe docking environment for LNG ships arriving from around the world. Grating, guardrails, and support structures totaling 250 tons, exposed to the frigid, soggy environment were hot-dip galvanized to prevent the hazardous effects of corrosion in this busy port. Canaport connects natural gas fields from around the world to North America and will supply nearly 20% of the natural gas for the Northeastern US and Canada in the near future.
For Canaport, the importance of initial versus long-term cost was a high priority the company was looking for a protective coating that would provide a long lifespan with minimum future maintenance. Hot-dip galvanized steel will remain maintenance free for 50+ years, saving the cost of constant touch up and preservation, so the port can continue corrosion-free operation for decades to come.