Longevity in Various Environments
Hot-dip galvanized steel is often utilized in some of the harshest environments imaginable, yet it provides maintenance-free longevity for decades. The corrosion resistance of hot-dip galvanizing varies according to its surrounding environments. Measurements of the actual consumption rate of the coating during the first few years of service provide good data for projecting a conservative estimate for the remaining life to first maintenance, because as zinc corrosion products build on the surface, which in most environments are adherent and fairly insoluble, the corrosion rate often slows as time progresses.
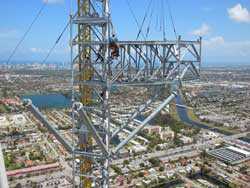
There are four main macro environments power structures are exposed to and each has different factors that dictate the corrosivity to galvanized steel. Some structures, such as distribution poles, are often exposed to more than one of these environments at the same time. More information about hot-dip galvanized steel's longevity can be found in the AGA's publication Performance of Hot-Dip Galvanized Steel Products.
Atmospheric
The most common exposure environment for hot-dip galvanized steel is atmospheric. As hot-dip galvanized steel is exposed to the atmosphere, the zinc interacts with free-flowing air and moisture to develop the zinc patina. The zinc patina is critical to the longevity of galvanized steel in the atmosphere; and thus, accelerated, salt-spray tests that do not mimic real world exposure conditions are not an accurate predictor of HDG's longevity.
The performance of atmospherically exposed hot-dip galvanized steel depends on five main factors: temperature, humidity, rainfall, sulfur dioxide (pollution) concentration in the air, and air salinity. None of these factors can be singled out as the main contributor to zinc corrosion, but they all play a role in determining the corrosion protection hot-dip galvanized (zinc) coatings can provide in certain atmospheric conditions.
For corrosion classification purposes, atmospheres are divided into five main categories based on the levels of each of these factors: industrial, tropical marine, temperate marine, suburban, and rural. Industrial atmospheres (most cities and urban areas) are the most aggressive because they contain more sulfides and phosphates which contribute to a more rapid consumption of the zinc. The least aggressive atmosphere is rural, as there are relatively low emissions in the air in such environments.
Longevity Case Study
Omaha Transmission Line
Soil
Another common exposure for hot-dip galvanized steel is partially or fully buried in soil. With more than 200 different types of soil identified in North America, hot-dip galvanizing’s performance in soil is varied and hard to predict. The main factors that dictate the corrosivity of the soil are moisture content, pH level, and chlorides. These soil conditions are affected by additional characteristics such as aeration, temperature, resistivity, and texture or particle size. A general rule of thumb is galvanizing performs well in brown sandy soils, and not as well in gray, clay-like soils. This is because soil with larger particles wick moisture away from the surface more quickly so the galvanized piece has less exposure to moisture.
At ground level, corrosion mechanics of HDG are less defined than atmospheric exposure (higher on the pole). At ground level, there is potential for soil build-up/contact, vegetation/weeds causing abrasion or holding moisture, etc. HDG steel is able to withstand this transition environment thanks to its durability and abrasion resistance, as well as the performance of the zinc patina. However, it is common to see a duplex coating on the base of the pole extending past ground level for extra protection.
Longevity in Soil Case Study
Turquoise Solar
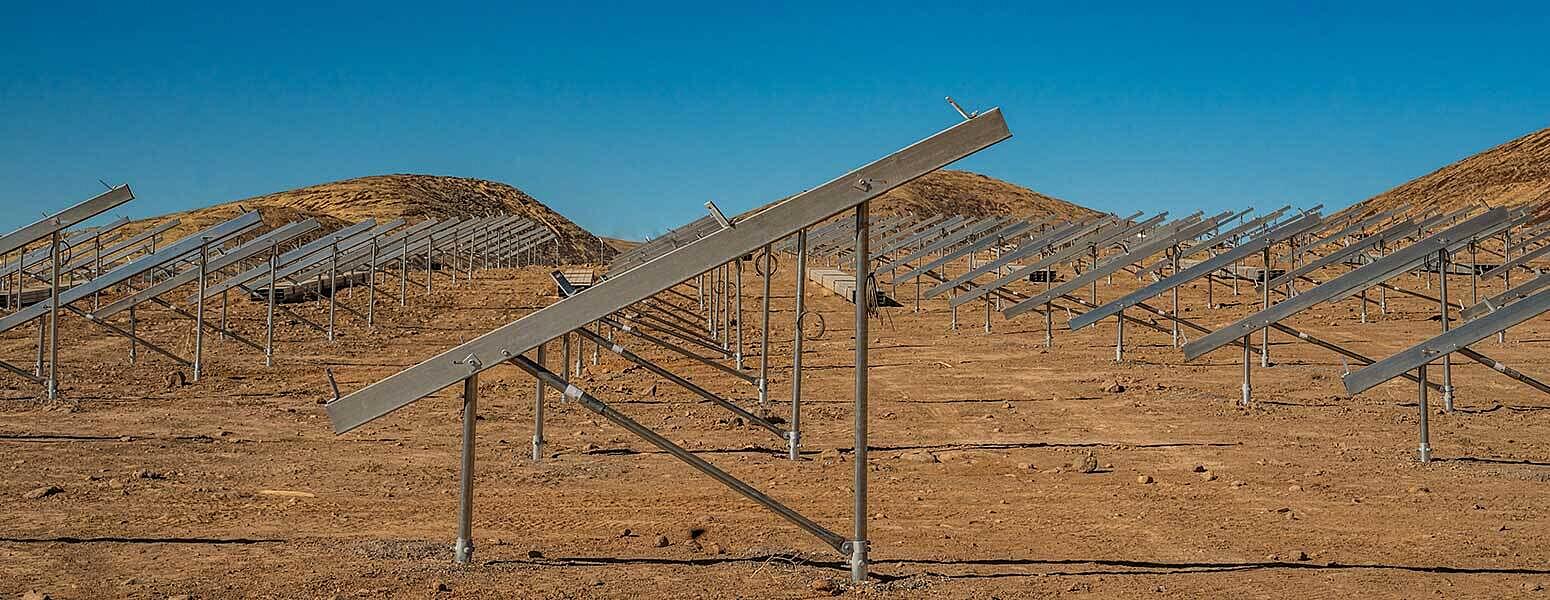
Turquoise sits on approximately 180 acres of igneous rock and ledge at a mountainous base in Washoe County, Nevada. After numerous failed trials from other solar installation companies who attempted to drive their pile system into the site’s rocky terrain, TerraSmart was hired when the project’s owner, Greenbacker Renewable Energy Company, said to call them.
This rocky climate and arid climate called for the most durable coating system available to the solar utility market. Nothing other than hot-dip galvanizing could have stood up to the task of literally being drilled into rock and then still be expected to protect steel for decades to come. The legs attach the solar racks to the screws in the ground, holding up all the weigh of the racking and panels for the years to come. The legs will be exposed to the desert heat, sand and rock. The hot-dip galvanized zinc coating will be the only thing protecting them from the environmental threats on the climate.
Upon completion, Turquoise will provide power via Nevada Energy, allocated for Apple’s data center through their Green Energy Rider Agreement with NV Energy.
Water
A third and less common environment for steel in the power sector is submerged in or exposed to water. The first step in deciding whether galvanized steel is the right coating for your application is to determine what type of water the steel elements will be exposed to. Water can be divided into a number of different types; pure water (e.g., distilled water or de-ionized water), natural fresh water, potable water (treated drinking water), or seawater. Additionally, the mineral content (hard or soft water) and temperature also cause corrosion to different degrees.
Similar to soils, the varieties of water make predicting corrosion rates difficult. Many parameters affect corrosion of metals in a water environment, including pH level, oxygen content, water temperature, water climate and tide conditions. Despite the difficulty of predicting corrosion, hot-dip galvanizing steel is one of the best methods of corrosion protection for submersed applications.
The most obvious water application in the power sector is in hydroelectric generation plants. As they are most often located in freshwater lakes, reservoirs, and rivers, galvanized steel’s performance in fresh water is most critical. As many of the transfer pipes and penstocks exist submerged in water, they are constantly exposed to the corrosive attacks of moisture. Galvanized steel performs very well under these conditions, performing flawlessly in harsh water environments such as seawater for 8 – 12 years.
Fresh water environments have two major constituents for categorizing corrosion potential: hard and soft water. Carbonates and bicarbonates, present in some concentration in fresh water, tend to deposit protective films on the zinc surface, helping to stifle corrosion. Carbonates subdue the corrosion effects of anions, the most corrosive to zinc being chloride in excess of 50 mg/L. The softer the water, the lower it is in carbonate, which means a more pronounced chloride content. Conversely, the harder the water the greater it is in carbonate and the corrosiveness of the chlorides are minimized. Therefore, the general rule is soft water is more corrosive to hot-dip galvanized steel than hard water.
Water agitation also can be a factor when determining corrosion rates. If the pipes are located in an area of fast moving river currents or even perpetual wave motion, these are important considerations in determining the corrosion protection delivered by galvanized steel. Often this motion of “washing” the carbonates off the zinc surface and not allowing them to form a protective film, along with zinc erosion, can be the cause for accelerated corrosion of zinc coatings.
Regardless of water type, fresh or saltwater, galvanized steel provides corrosion protection that will limit maintenance and last for decades, keeping your facility operating smoothly and uninterrupted.
Longevity Near Water Case Study
Wind Turbine Bolt Platforms
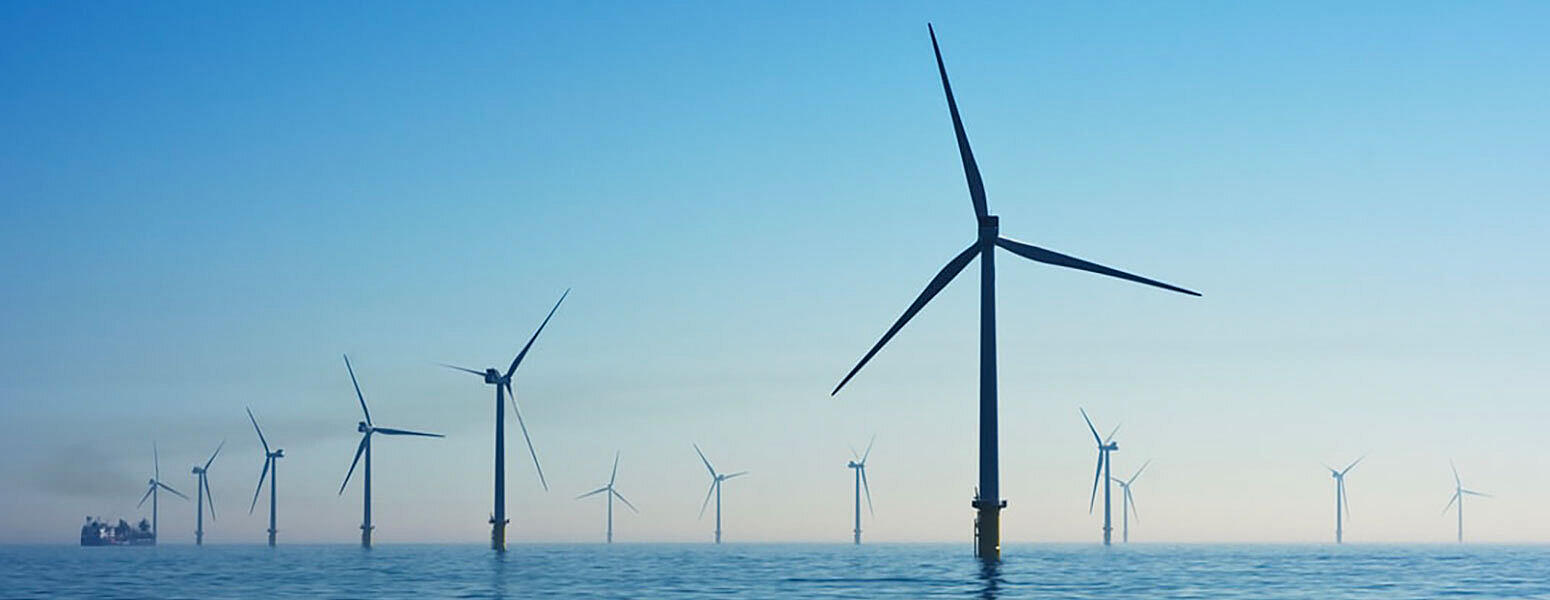
Wind has been an energy source in the U.S. since the late 1800’s. In the last couple of decades we have seen wind farms emerge all across the United States as one of the fastest growing renewable energy sources. Since this inception one problem that has been consistent is corrosion. These platforms serve several functions from providing a safe platform to bolt sections of the tower together while erecting the turbines, to performing routine maintenance inside the towers. The galvanized platforms work well inside these turbine towers since it is not a climate-controlled environment, preventing corrosion in some of the harshest conditions in the offshore turbines.
Other
Some other common environments where hot-dip galvanized steel is considered and can perform well include embedded in concrete and extreme temperatures (-40 F - 392 F). Hot-dip galvanizing is commonly used in contact with treated wood, including wood distribution poles. There are ancillary items and “sleeves” sometimes retro-fitted to poles to protect from damage and deterioration. HDG typically is not recommended in contact with other metals, unless there is isolation between them with non-conductive materials. The exception to this rule is aluminum and stainless steel, except in salt water or high salinity in the air.