Long Lasting Corrosion Protection
Steel is an abundant, efficient building material that provides specifiers design freedom. However, for projects exposed to the atmosphere and other harsh environments, it is critical to coat the steel for corrosion protection. Often large construction projects target a 50-100 year design life, highlighting the need for durable, long lasting corrosion protection. Hot-dip galvanizing (HDG) provides three levels of corrosion resistance to steel: barrier protection, cathodic protection, and the zinc patina.
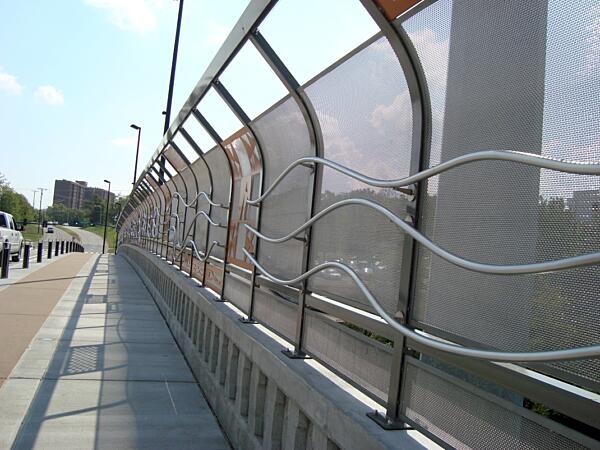
Barrier Protection
Like paints, the hot-dip galvanized coating provides protection by isolating the steel from the environment. As long as the barrier is intact, the steel is protected and corrosion will not occur. However, if the barrier is breached, corrosion will begin. Because a barrier must remain intact to provide corrosion resistance, two important properties of barrier protection are adhesion to the base metal and abrasion resistance.
Coatings such as paint have pinholes susceptible to penetration by elements causing under film corrosion to spread rapidly. On the other hand, hot-dip galvanizing is tightly-bonded to the steel with no bare spots, making its barrier protection quite strong.
Cathodic Protection
In addition to great barrier resistance, hot-dip galvanizing also provides cathodic protection, which means the zinc will preferentially corrode to protect the underlying steel. We know this based on the Galvanic Series of Metals, which lists metals in order of electrochemical activity in seawater (electrolyte). Metals higher on the list are anodic to those below them, which means they will corrode first when the two are connected. Because zinc sits near the top of the list, it will try to protect many other metals (including steel) it comes in contact with.
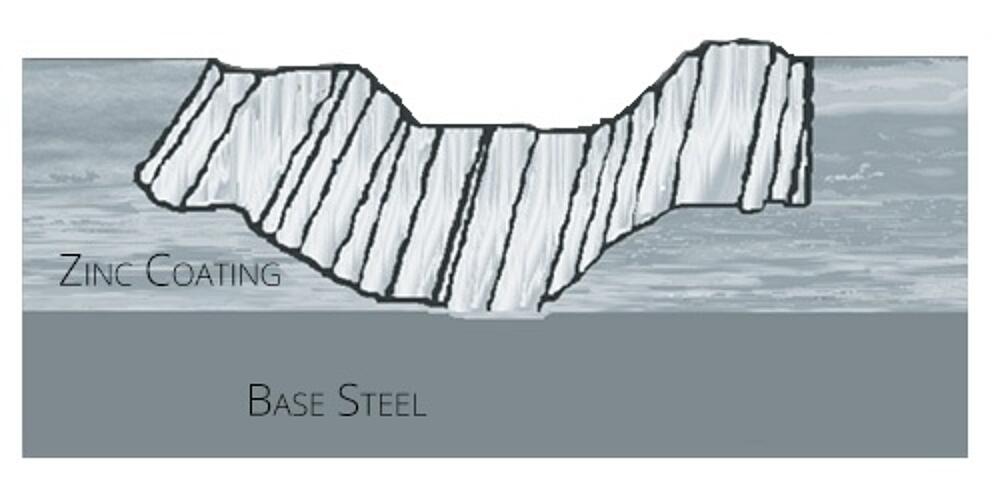
In the case of hot-dip galvanizing, where the zinc coating is in contact with the base steel, the zinc will be slowly consumed while the steel remains protected. The zinc’s sacrificial action will also offer protection where small areas of steel may be exposed due to cut edges, drill holes, scratches or other surface abrasion from rough handling, erection, or exposure to elements. In fact, even if the HDG coating is damaged to the point that bare steel is exposed (up to about ¼ inch in the maximum diameter) no corrosion will begin until all the surrounding zinc is consumed. For instances where a larger area were exposed, the zinc would keep the corrosion isolated to that area, rather than allow spreading across the part.

Zinc Patina
The final key to hot-dip galvanizing’s corrosion protection is the development of the zinc patina. Zinc, like all metals, corrodes when exposed to the atmosphere. During exposure to moisture and free flowing air (natural wet/dry cycles in the environment), a series of zinc corrosion byproducts will form on the coating surface. The formation of these byproducts (zinc oxide, zinc hydroxide, and zinc carbonate) develop into the zinc patina, which acts as an additional passive, non-soluble barrier for the hot-dip galvanized coating. Once developed, the zinc patina will slow the corrosion rate of the zinc to about 1/30th the rate of steel in the same environment. Thus, a relatively thin coating of zinc can last much longer in the environment to protect a much thicker piece of steel.