Economic Benefits
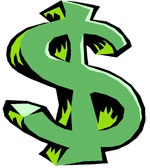
To be sustainable, designers should look to a product with a bottom line that not only suits the needs and abilities of the client, but also keeps an eye to future expenses and effects. This is an area where hot-dip galvanized steel stands a head above the rest.
Specification is often determined by the bottom line. To be sustainable, design must address the needs/abilities of client, while keeping an eye to future expenses. By specifying hot-dip galvanized steel, the client will benefit from a trifecta of savings – economical construction, affordable functionality, and lower life-cycle cost.
Construction Savings
Affordable construction and transportation savings, in addition to savings created by quick turnaround, mean the initial price tag for construction is lower than competing materials.
Prefabrication, including pre-cut mounting holes for utilities standard use, and offsite galvanizing can lead to quick turnaround and installation. The galvanizer can stage delivery of the items in time for installation. As previously noted, the lighter weight of the material can cut down on shipping and installation charges, and steel poles do not require ground wires the length of the pole.
Savings in Use
One of the primary advantages of utilizing hot-dip galvanized steel elements in power infrastructure is the extended time to first maintenance
Even in corrosive, industrial environments, hot-dip galvanizing can last 70+ years without maintenance. In suburban and rural settings that can extend well past 100 years. This is important when planning grid infrastructure in remote areas, where they are not easily accessible or viewed regularly. The longevity without maintenance also means there is less shutdowns for repairs, which are costly and frustrating for consumers.
Life-Cycle Savings
Taking into account construction, transportation, direct, and indirect costs over the life of galvanized power infrastructure leads to what is perhaps the most impacting structural cost analysis – life-cycle cost.
Beyond the cost of repairs and maintenance there is the time value of money, or inflation and interest, to consider. Also, when it comes to utility poles, wood poles often have costly disposal fees because of the treatments used on the poles. In contrast, hot-dip galvanized poles are 100% recyclable, either being recoated and reinstalled or melted down for new material. Both avenues save money, and perhaps even “make” money on steel scrap, rather than costing more at the end-of-life.
Cost Case Study
Tucson Electric, 2009
In addition to all the benefits using hot dip galvanizing has on reliability there can be substantial savings as well. In 2009 Tucson electric power set up a team to study several issues in depth to develop a clear understanding of how steel poles compare to wood. The team included employees from engineering, standards, construction, environmental, safety and purchasing. Out of this came a detailed life cycle cost analysis.
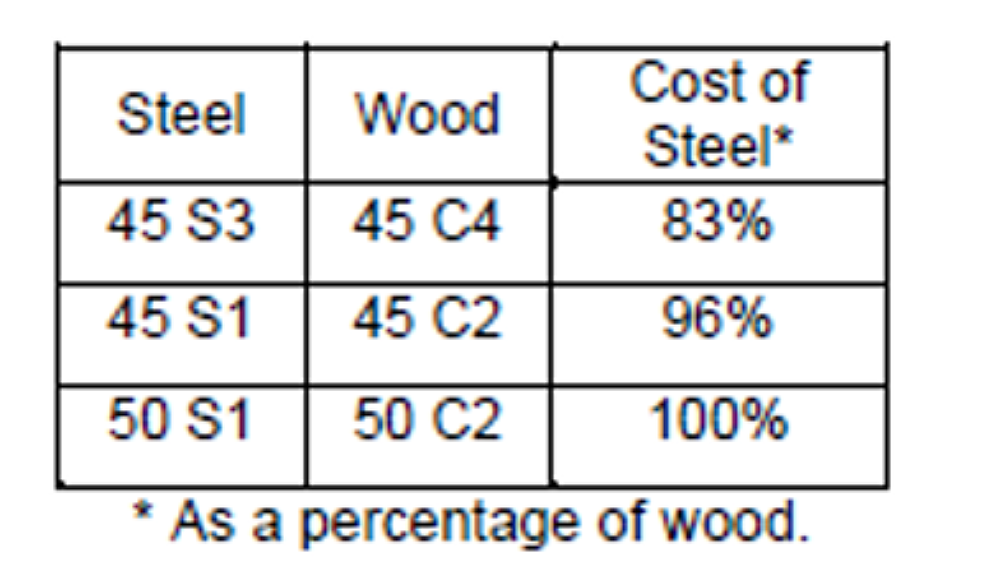
The table above compares the relative life cycle cost of steel vs. wood for three of the most commonly used sizes of distribution pole in TEP’s system. TEP found that even though the initial cost of a steel pole is much higher, a steel pole was actually cheaper or equivalent though its life cycle. This was due a steel pole lasting 60 years in TEP’s environment vs wood’s 30 years, Less maintenance throughout the pole's life, easier installation, and easy recycling at the end of life. TEP’s Senior Distribution Engineer, David Parpart added “the study also found that a steel pole offered better reliability in a consistent engineered product, while costing about the same”
In other parts of the power grid, particularly in generation and transmission, steel is commonly selected, but not always hot-dip galvanized. The following case study compares hot-dip galvanizing to various other corrosion protection coatings. When evaluating the initial and life-cycle costs of HDG, there are a number of parameters to consider.
Steel Coatings Life-Cycle Cost Study Project Parameters
Let's assume we have a project that has 50,000 square feet of steel that needs to be protected from corrosion, is targeting a 70-year design life and is being erected in a moderately industrial (C3) environment. This could easily represent a small generation facility.
In this example, we are evaluating hot-dip galvanizing in comparison to several high-performance paint systems, metallizing, and a duplex system (paint over galvanizing). This analysis used the national average for hot-dip galvanizing ($0.27/lb or $2.16/ft2). All cleaning was done to SP-10 automated, other than the duplex system which was cleaned using SP-16 for HDG surfaces, and metallizing was blasted to a near white metal clean. All coats were applied in the shop, and the structures were all classified as simple for future maintenance costs.
As mentioned before, it is not recommended to analyze only the initial cost for a corrosion protection system. However, if it is the only analysis, galvanizing is still a solid choice, as it is often initially less expensive or very cost competitive with other coating systems. Keep in mind these costs are all coming from the manufacturer (paint manufacturer and/or galvanizer) and do not take into account fabricator markup which may be assigned at varying rates dependent on the material (i.e. galvanizing may be marked up more if the fabricator has his own paint facility).
As a reminder, this example uses a typical mix of structural pieces, which will typically yield an initial galvanizing cost lower than most paint systems, as the galvanizing process efficiently accommodates bundles and groups of steel. However, even if you compare medium or large structural elements, the galvanizing cost is less expensive or within a few cents per square foot of each of these systems as well. The strongly held notion galvanizing is more expensive initially is no longer accurate, as the cost of HDG has remained relatively stable while the cost of paints and other systems have increased significantly over the last 5-10 years.
Note: Average Annual Equivalent Cost (AEAC) is per square foot (total LCC divided over years in service and size of project).
When life-cycle costs are considered, hot-dip galvanizing is the most economical system for corrosion protection. In fact, this analysis does not even include the hidden (or indirect) costs associated with touch-up, maintenance, and full repainting required for paint systems. If deviations from the practical maintenance schedule occur, life-cycle costs could be significantly higher than indicated.
After 70-years of life, the initial cost of the galvanizing is identical to the original cost as no maintenance would be required in this environment. Also, when comparing to the other coating systems, the life-cycle cost savings are significant in comparison. The second best option over the life of the project in this example is actually the duplex system of paint over galvanizing – because as mentioned before, the galvanized “primer” allows less maintenance cycles to the painted system than the same system (with IOZ primer) on bare steel.
Also, of note, often the least expensive systems initially (Epoxy/Polyurethane, Epoxy/Epoxy) are the most expensive in life-cycle cost (because they require more maintenance). Even though the metallizing system requires less maintenance, the cost to metallize (and touch up with metallizing in the field) is much higher than it is to use paint in the field.
It is also important to understand these costs are only the DIRECT costs, and do not account for the indirect costs (such as impact to businesses when a road is closed down, etc.) which are typically 5x-11x the direct costs of repair.