Durability & Longevity
Durability
Another aspect of hot-dip galvanizing is proven durability. Hot-dip galvanized steel has been specified extensively in petro-chemical, industrial, power/utility, and bridge/highway projects because of its unmatched durability in these harsh environments. Hot-dip galvanizing remains durable thanks to its abrasion resistance, uniform protection, and complete coverage.
Abrasion Resistance
A unique characteristic of the hot-dip galvanized coating is the development of metallurgically bonded (~3,600 psi), abrasion resistant intermetallic layers. The photomicrograph (below) is a cross-section of a galvanized steel coating showing the three intermetallic layers (Gamma, Delta, and Zeta) and top layer of pure zinc (Eta). During the galvanizing process, these layers develop naturally during a metallurgical reaction between the iron in the steel and zinc in the kettle. As the photomicrograph also shows the hardness of each of the layers as a Diamond Pyramid Number (DPN), you can see the three intermetallic layers are harder than the base steel, while the eta layer has ductility which makes damaging the HDG coating very difficult.
Hot-dip galvanizing’s abrasion resistance provides unmatched protection against damage caused by rough handling during transport and erection, as well as in service. Other coatings with lower bond strengths (300-600 psi) can be easily damaged during shipment and construction, weakening their effectiveness, as barrier protection is dependent upon the integrity of the coating.
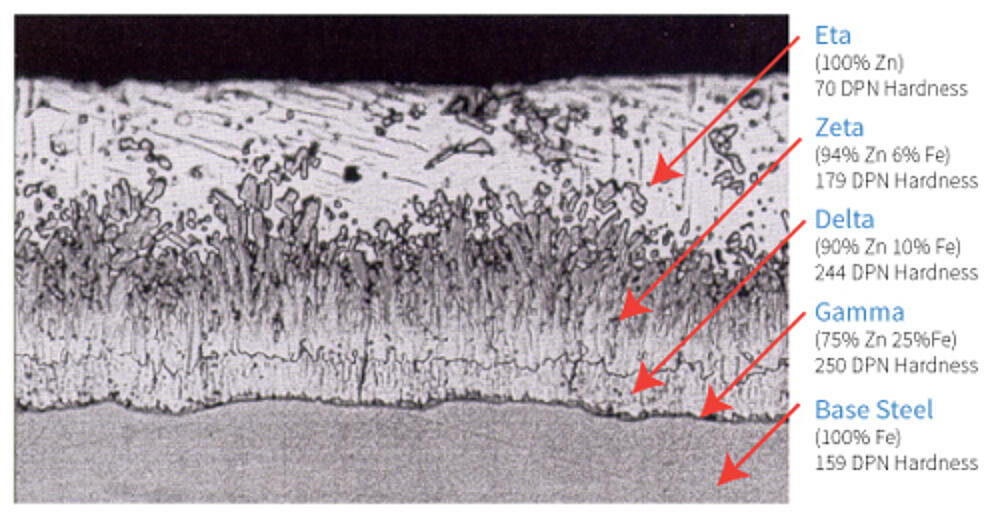
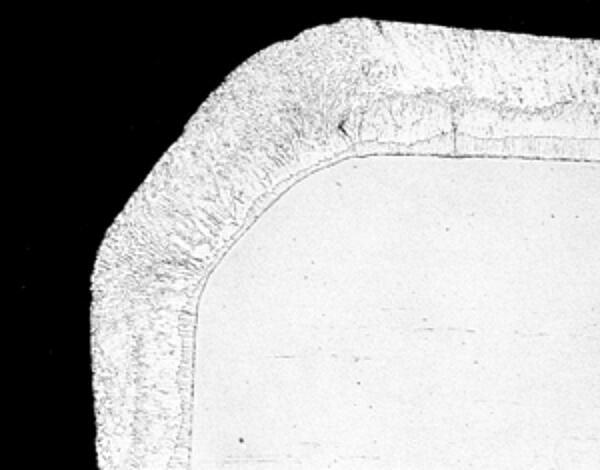
Uniform Protection & Complete Coverage
During the metallurgical diffusion reaction in the galvanizing kettle, the galvanized coating grows perpendicular to all surfaces. Therefore, the coating is naturally as thick on corners and edges as flat surfaces. Since coating damage commonly occurs at edges, added protection at these junctures is important. Brush- or spray-applied coatings have a natural tendency to thin at corners and edges leaving the part prone to attack. The uniform protection of hot-dip galvanized steel leaves no weak points for accelerated corrosion.
Furthermore, hot-dip galvanizing is a total immersion process, meaning the steel is fully submerged into cleaning solutions and the molten zinc, coating all interior and exterior surfaces. This complete coverage ensures even the insides of hollow and tubular structures and the threads of fasteners are coated. As corrosion tends to occur at an increased rate on the inside of hollow structures where humidity and condensation occur, interior coverage is very beneficial. Hollow structures that are painted have no corrosion protection on the inside. Fully coating fasteners is equally important as they are utilized at connection points which are critical to structural integrity.
Longevity in Atmosphere: Time to First Maintenance
Hot-dip galvanized steel is often utilized in some of the harshest environments imaginable, yet it provides maintenance-free longevity for decades. The corrosion resistance of hot-dip galvanizing varies according to its surrounding environments, but generally corrodes at a rate of 1/30 of bare steel in the same environment. Measurements of the actual consumption rate of the coating during the first few years of service provide good data for projecting a conservative estimate for the remaining life to first maintenance, because as zinc corrosion products build on the surface, which in most environments are adherent and fairly insoluble, the corrosion rate often slows as time progresses.
Whether exposed in the atmosphere, subjected to blazing UV rays, snow, and/or other elements, submerged in water, or embedded in soil or concrete, hot-dip galvanized steel can withstand the different corrosive elements and fulfill the intended design life. More information about hot-dip galvanized steel’s longevity can be found in the AGA’s publication Performance of Hot-Dip Galvanized Steel Products.
The most common exposure environment for hot-dip galvanized steel is atmospheric. As hot-dip galvanized steel is exposed to the atmosphere, the zinc interacts with free flowing air and moisture to develop the zinc patina. The zinc patina is critical to the longevity of galvanized steel in the atmosphere; and thus, accelerated, salt-spray tests that do not mimic real world exposure conditions are not an accurate predictor of HDG’s longevity.
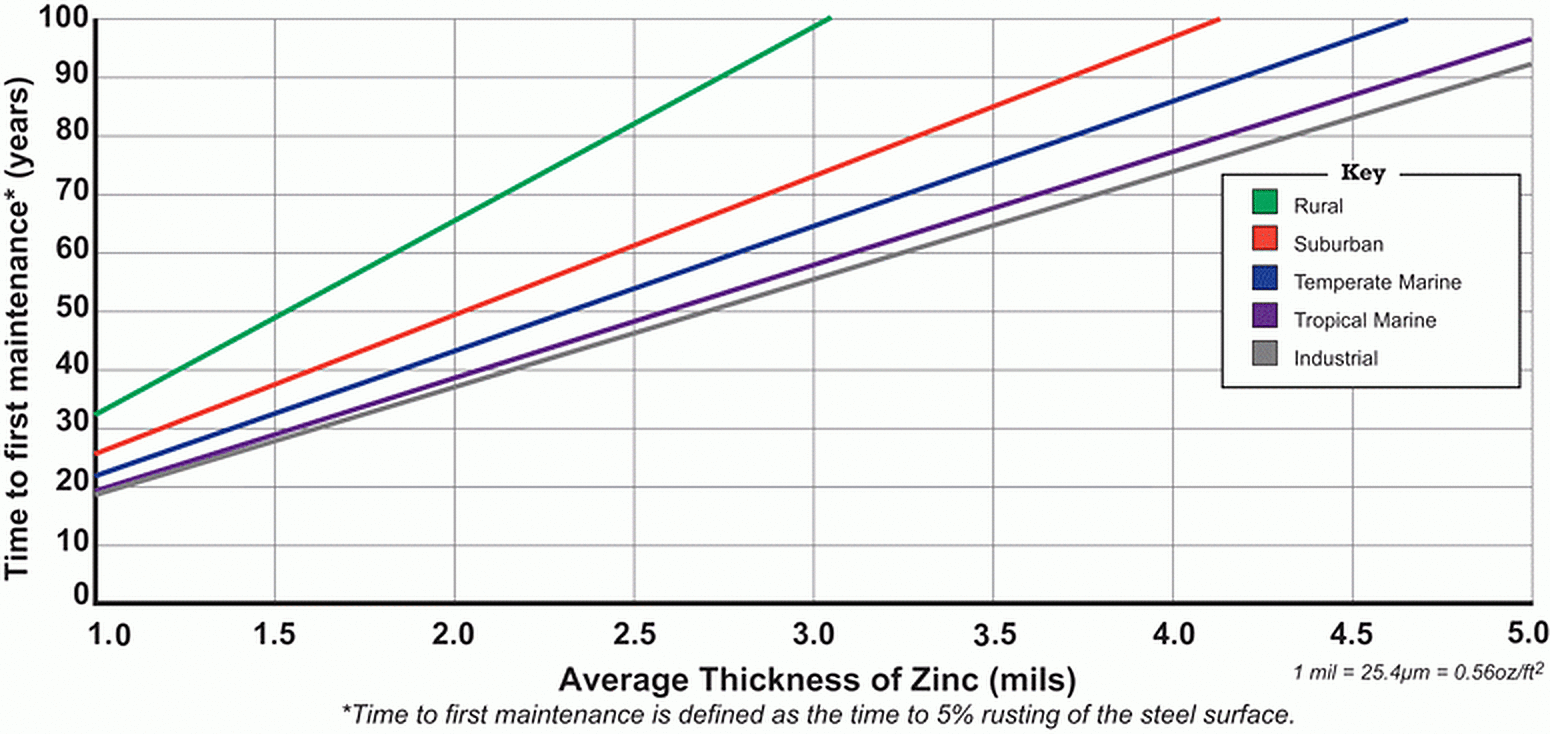
The performance of atmospherically exposed hot-dip galvanized steel depends on five main factors: temperature, humidity, rainfall, sulfur dioxide (pollution) concentration in the air, and air salinity. None of these factors can be singled out as the main contributor to zinc corrosion, but they all play a role in determining the corrosion protection hot-dip galvanized (zinc) coatings can provide in certain atmospheric conditions.
For nearly a century, independent and industry testing of samples in five environments (industrial, rural, suburban, tropical marine, and temperate marine) have yielded real-world performance data for hot-dip galvanized steel. Using this real-world corrosion data, statistical methods, and neural network technology, Dr. Gregory Zhang of Teck Metals Ltd. Developed the Zinc Coating Life Predictor (ZCLP) to estimate the life of hot-dip galvanized coatings in atmospheric conditions. Using the ZCLP, you can input specific parameters for any environment and get an estimated time to first maintenance (TFM) for the galvanized coating
Time to first maintenance is defined as 5% rusting of the base steel surface, which means 95% of the zinc coating is still intact, and an initial maintenance is recommended to extend the life of the structure. According to ASTM A123, the governing specification for hot-dip galvanizing, steel ¼-inch thick or greater must have at least 3.9 mils of zinc on the surface, but more often than not, there will be greater than the minimum requirement. Therefore, using the TFM chart, hot-dip galvanized structural steel (>1/4-inch thick) provides 72-73 years of life to first maintenance even in the most corrosive atmosphere, industrial.
Durability & Longevity Case Study
Bridges of Stark County-Stark County, OH; 1970s
The Bridges of Stark County Ohio are galvanized bridges and have been for 40 years. In the early 1970s, Rich Larocco was a young bridge engineer for Stark County, just out of college. At that time, 110 of Stark Countys bridges were deficient and 50% of the bridge budget was used to repaint bridges. Rich worked with the former owner of the galvanizing facility to change those numbers. Rich decided rather than continue to repaint bridges over and over, he would dismantle the bridge. He had the decks and beams removed. The beams were sandblasted and galvanized. Then the entire recycled bridge was reinstalled. After that they never repainted an old bridge or painted a new bridge even if the long beams or large trusses had to be progressively dipped in the galvanizing plant. There are 442 Bridges in Stark County, 335 of which are maintained by the county. Many are short span low clearance steel bridges over creeks and streams in rural areas, making an ideal environment for hot-dip galvanized bridges.