Why Duplex?
Although aesthetics may be the primary factor, there are a number of other reasons why utilizing a duplex system is advantageous. As more specifiers understand the importance of corrosion protection, galvanized steel used in conjunction with paint/powder coatings has risen.
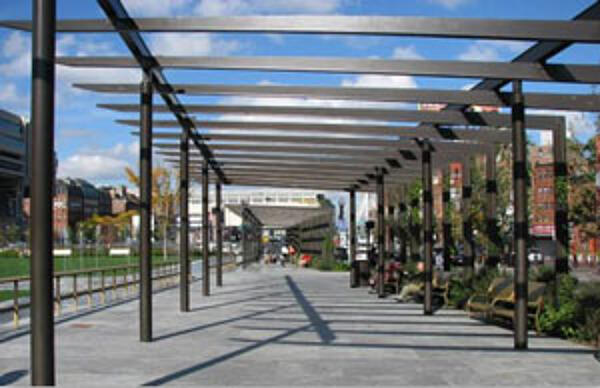
In addition to extended life (synergistic effect), here are some other benefits of specifying a duplex system:
- Aesthetics
- Color Coding/Safety
- Extended Corrosion Resistance
- Ease of Repainting
Aesthetics
Hot-dip galvanized steel provides an attractive, metallic-gray finish many specifiers have come to appreciate. However, when the industrial finish of galvanizing does not suit a particular project, painting or powder coating can offer an aesthetic alternative. Whether the architect prefers a vibrant color, or the owner prefers the project blend with its surrounding environment, painting or powder coating over galvanized steel provides superior corrosion protection along with the color preference. Duplex systems are becoming a common trend in university and professional stadiums as the top coat provides team branding, and the underlying galvanized steel provides the corrosion protection and service life required.
Color Coding/Safety
A duplex system also may be used to conform to safety regulations. Duplexing increases safety in many environments by enabling color-coding of gas, steam, or chemical pipes, identifying hazardous work areas and walkways, and marking high-voltage electrical lines and equipment. For example, the Federal Aviation Administration (FAA) requires structures over 200 feet tall to be painted in the alternating pattern of white and international orange. Duplexing these types of projects ensures the proper color coding is in place without sacrificing corrosion protection on often difficult to maintain structures.
Extended Corrosion Resistance
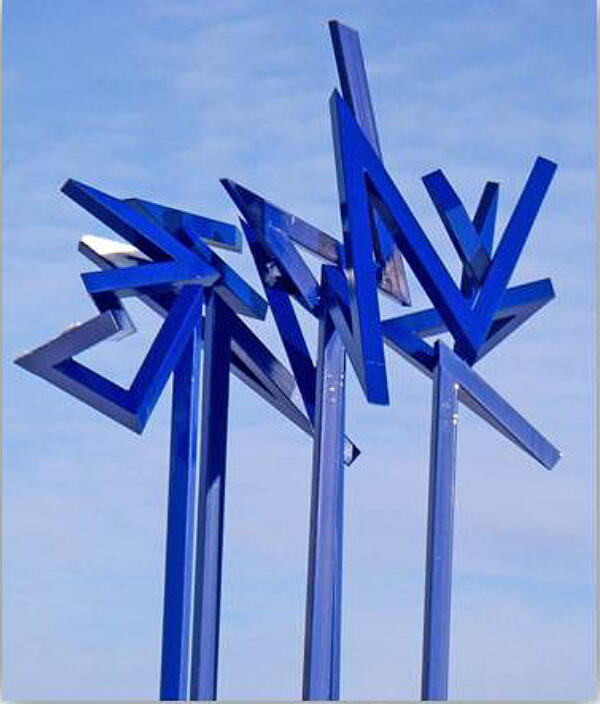
Because of the synergy between paint/powder coatings and galvanizing provide, an obvious and important reason for specifying duplex systems is the added corrosion protection it provides. In harsh environments where galvanizing or paint/powder coatings alone have difficulty protecting steel, utilizing a duplex system can provide the necessary corrosion resistance.
Ease of Repainting
As outlined in the synergistic effect section, an important advantage of painting over galvanizing is the extension of the maintenance cycle. In addition to an extended maintenance-cycle, painting on a galvanized surface also facilitates the maintenance repainting. As the paint film weathers, the zinc in the galvanized coating is present to provide both cathodic and barrier protection until the structure is repainted. The exposed zinc surface then can be repainted with minimal surface preparation.
Ease of Powder Coating/Touch-Up
While the substrate galvanized steel will provide both barrier and cathodic protection for decades, similar to paint, the exterior powder coating may, in time, need to have small nicks or scratches touched up. This can be achieved in the field by using automotive touch-up paint, which is both relatively inexpensive and will provide a durable seal. It can, however, be somewhat difficult to match colors exactly using this method.
To apply touch-up paint, the affected area must be prepared by removing a small amount of powder coating surrounding the breach, roughening the metal and adjacent powder coating with a polymer abrasive pad, then wiping away any sanding by-products with an isopropyl alcohol wipe. Then the touch-up material may be applied with a brush application.
Duplex Systems Case Study
Cape Cod Rail Trail; South Yarmouth, MA 2018
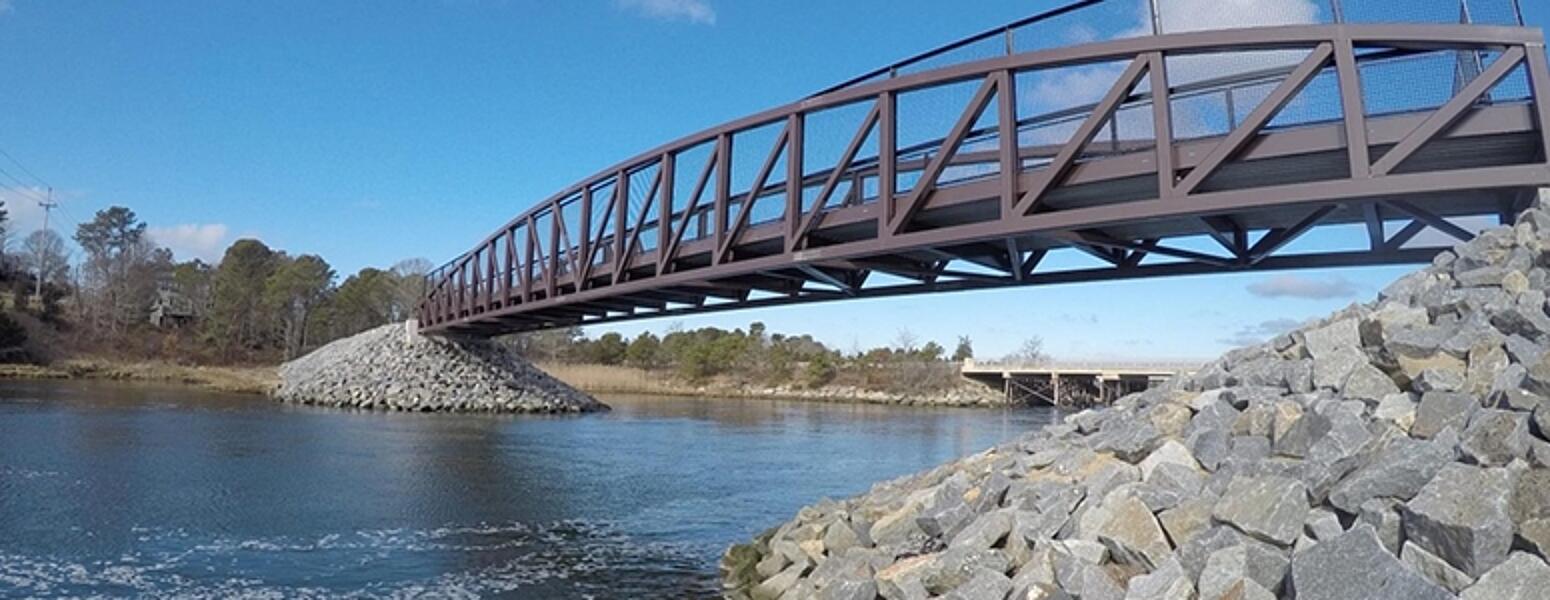
The Cape Cod Rail Trail (CCRT) is a paved bike-way that runs 25 miles from South Dennis to Wellfleet, Massachusetts. The history of the trail stems from the original trail-head in South Dennis, which transported passengers and freight to Cape Cod in the early 1800’s until around 1960. The CCRT today is a safe and enjoyable spot to spend a day in Cape Cod. The trail is smoothly paved making it ideal for cyclists, walkers, inline skaters, and runners to enjoy.
Ultimately, the specifier selected the duplex system, not only for its corrosion protection but also, to maintain that Northeast Trail “feel.”
The Massachusetts Department of Conservation and Recreation (MADCR) manages and maintains the trail, which they have been improving and expanding since 2002. The most recent upgrade increased the existing 60’ wide Bass River Bridge to 165’ providing additional space to view the Bass River and its surroundings. This portion of the project will not only serve as a pedestrian bridge for the CCRT, but has been designed to also be a tidal restoration project. As a result this will improve the ecosystem of the upper Bass River as well as improve navigation by deepening the channel and reducing the velocities under the bridge.
Fortunately, the specifier (MADCR) recognized that galvanizing the pedestrian bridge would protect the steel from rust and corrosion for decades to come. The durability that the galvanized coating offered would be far superior to that of just a regular painted surface and a duplex coating of powder coating over galvanizing would provide an even greater life span. Ultimately, the specifier selected the duplex system, not only for its corrosion protection but also, to maintain that Northeast Trail “feel.”
The hot dip galvanizer used for this project had to meet lifting capacity, kettle size and Massachusetts specification requirements. In addition, the galvanizer that was selected guaranteed they could smooth the galvanized surface to allow a 3-coat paint system to be applied to the bridge members. Now complete, the beautiful 165’ pedestrian bridge stands proud, eloquently placed over the Bass River for all outdoor enthusiasts to enjoy.
Galaxy Wheel at Galveston Island's Pleasure Pier; Galvenston, TX 2012
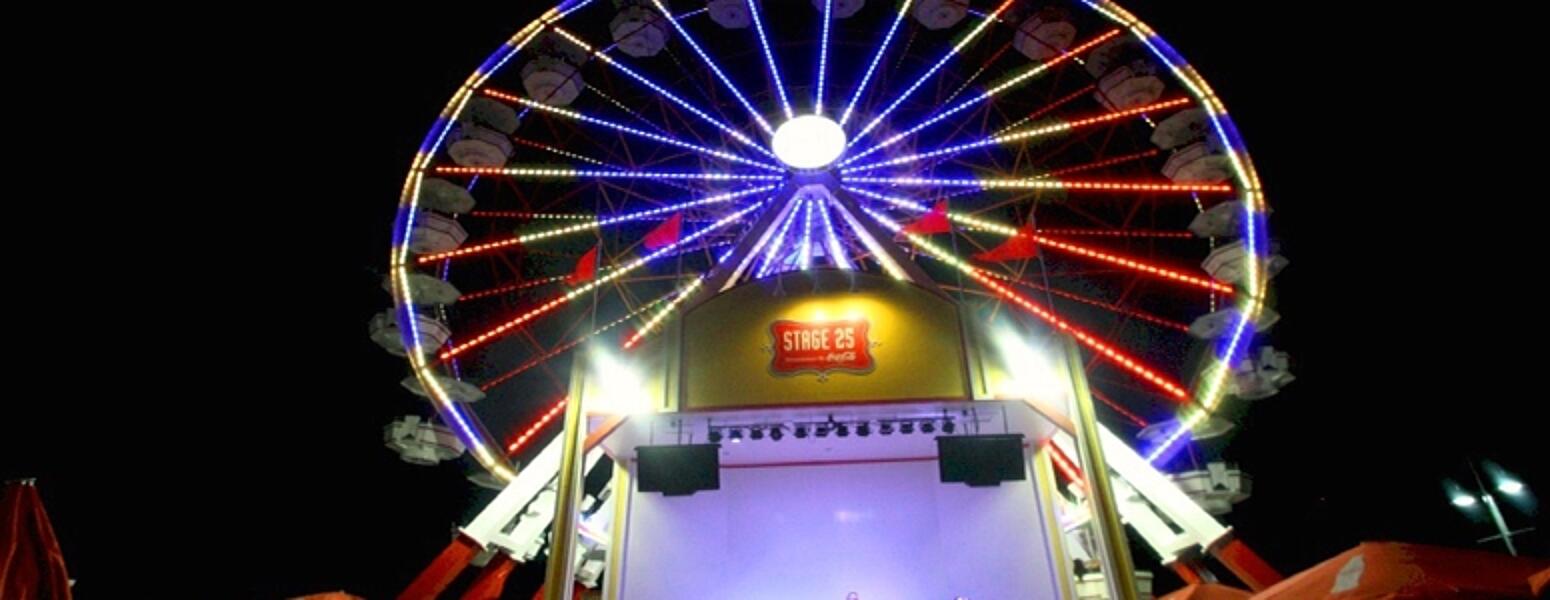
In the year 2000 when Landry’s, Inc. purchased the Pleasure Pier in Galveston, Texas, hurricanes had left the park in shambles. When the time came to begin planning for renovations, the owners and designers were well aware of the harsh conditions the amusement park would encounter during its life-cycle. Among 16 major attractions, the Galaxy Wheel lies at the southern-most end of the pier, overlooking the Gulf of Mexico. The Galaxy Wheel is a 90-foot-high Ferris Wheel that can accommodate up to 160 children at a time.
Because of its location, as well as the obvious concern for rider safety, a duplex coating system was specified to protect the structure from the harsh marine environment and tropical weather of the Gulf Coast Region. If paint alone were used on the Galaxy Wheel, maintenance costs would be much higher, especially considering the rapid rate at which steel corrodes in coastal locations. Repainting the wheel would involve not only the direct labor and material costs, but also high shutdown costs as the ride would be out of commission. The synergistic effect of a duplex coating system will minimize the frequency at which these costs are incurred.
The high level of complexity of the wheel required a reliable and accessible line of communication be established among the designer, fabricator and galvanizer to ensure on-time delivery and high quality. The Galaxy Wheel is a large and complex structure with many parts very similar in design, and every piece of steel on the ride was galvanized. A strict inventory was maintained to ensure the parts were not delivered out of sequence, which would cause delays in painting and construction.
The Galaxy Wheel is a definite eye-catcher for Pleasure Pier, and its final appearance is a key element for the attraction. The utilization of a duplex coating system allowed the designers to choose the desired color scheme to highlight the ride while also benefitting from the protective qualities of the HDG coating. These factors provide a clear competitive edge over a paint-only coating and will result in less down-time due to maintenance requirements, as well as increased rider safety due to the preservation of the structural integrity of the steel components.
The Pleasure Pier was originally built as a recreational facility for the U.S. military during World War II. At that time, it was the largest amusement facility in the nation and was dubbed “The Coney Island of the South.” The pier was all but destroyed over the years by the harsh, salty sea-air and vicious tropical storms. After the purchase by Landry's, the vision has finally come to fruition with the completion of the renovations. The pier is now highlighted by the Galaxy Wheel – a 90-foot Ferris Wheel at the southern end of the pier that ignites the Gulf Coast horizon with over 6,000 multi-colored incandescent lights. Local inhabitants of the Galveston area as well as thousands of tourists will enjoy the ride each year, and HDG played a significant role in making that possible in a safe, cost-effective manner.