Corrosion Protection + Color
Painting or powder coating hot-dip galvanized steel requires careful preparation and a good understanding of both systems. Many products have utilized a duplex system successfully for decades; automobiles and radio towers are two examples. When the galvanized surface is prepared correctly, paint and powder coating adhesion is excellent, and the duplex system becomes a highly successful method of corrosion protection. The use of duplex systems is growing throughout North America and the world because it provides the best of both worlds: corrosion protection + endless color options.
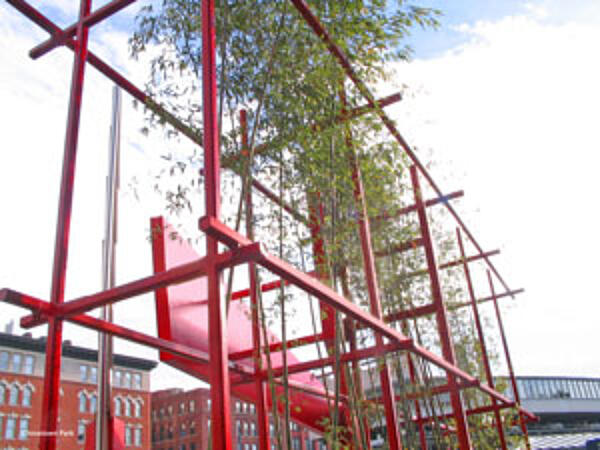
Before deciding how to protect steel from corrosion, it is important to understand how steel corrodes. Rust, iron’s corrosion product, occurs because of differences in electrical potential between small areas on the steel surface involving anodes, cathodes, and an electrolyte (a medium for conducting ions). When an electrolyte, such as water touching the steel surface, connects the anodes to the cathodes, a corrosion cell is created. This results in a loose, flaky iron oxide known as rust.
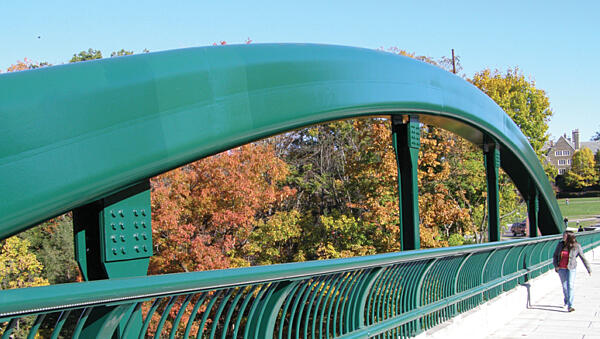
In order to protect steel from corrosion, something must interfere with the corrosion cell, either by blocking the electrolyte or by becoming the anode. Two common methods of corrosion protection are barrier protection (blocking the electrolyte from the steel surface) and cathodic protection (the formation of another anode). Hot-dip galvanizing alone affords both types of protection, but painting or powder coating over hot-dip galvanizing creates an additional barrier layer on top of the zinc coating. The synergy between the two coatings provides a longer service life while providing the aesthetic options often desired by an architect or designer.
Duplex Systems Case Studies
Scott Family Amazeum: Bentonville, AR; 2015
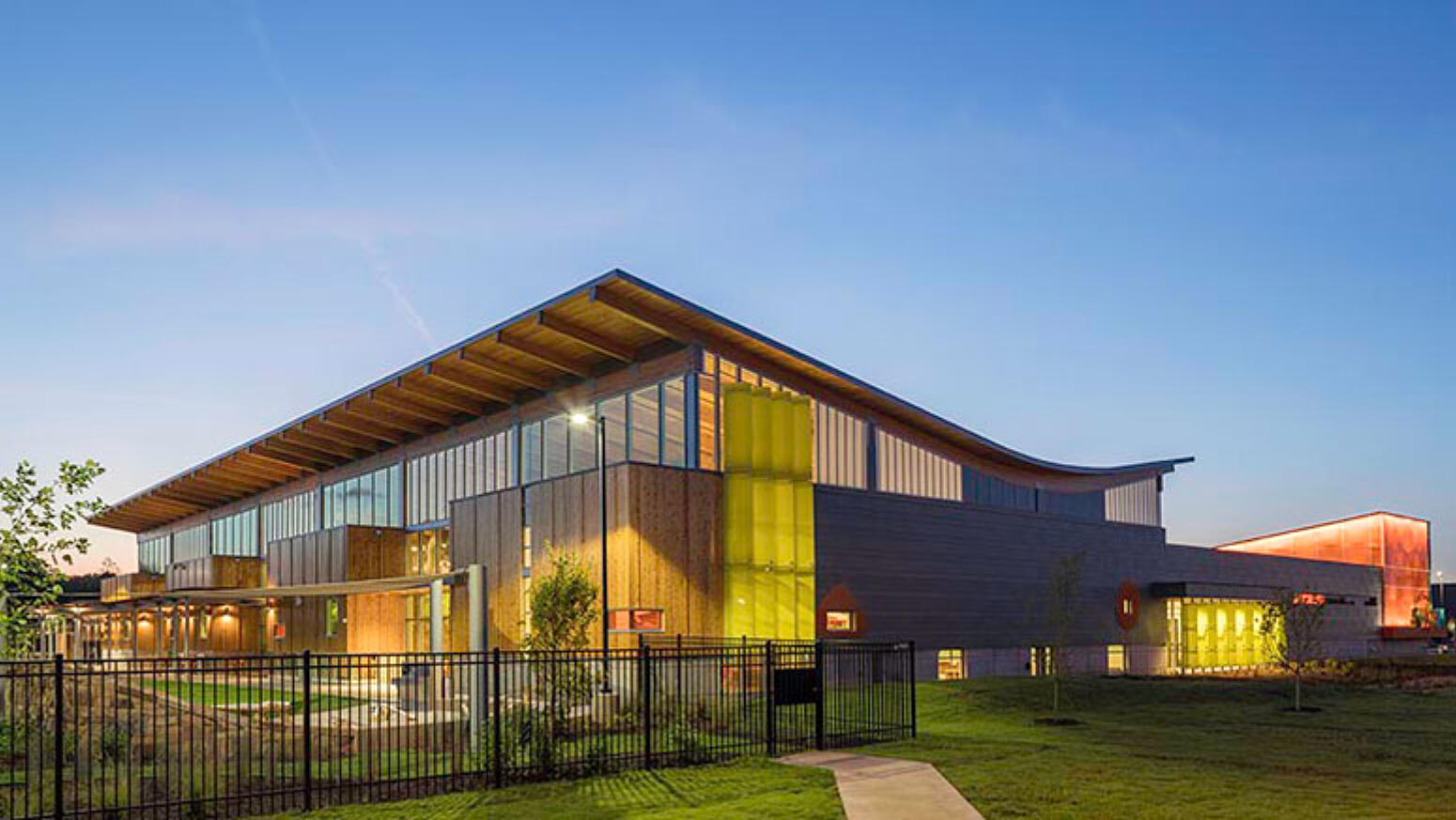
The Scott Family Amazeum Children's Museum was built to combine fun and functionality by executing a design featuring interactive indoor and outdoor learning spaces. The construction project features approximately 50,000 square feet of indoor exhibits and a one-acre outdoor learning space, which has exposed steel throughout. The outdoor playscape offers guests unstructured open-ended play that encourages connections with nature's wonders throughout, including full-body play and physical development.
When designing this space, the Scott family felt it was important to have an eco-friendly, green Amazeum. This environmentally-friendly area includes rain gardens, natural daylighting, bioswales, and geothermal cooling system – all of which utilize hot-dip galvanized (HDG) steel, a sustainable corrosion protection system. Upon the entrance to the museum, there are several large steel pipe support structures, which are not only exposed to the elements but also thousands of young children. The architect knew many children would be touching these pipes and wanted additional durability with little maintenance cost to keep the structure visually appealing for many years. Hot-dip galvanizing these steel structures ensures they will provide the necessary durability with little or no maintenance, and add to the overall sustainability of the project.
Although hot-dip galvanizing can provide unmatched corrosion protection, some areas also had paint applied as an aesthetic finish. With a coating hardness greater than steel alone, hot-dip galvanizing provides a low maintenance, durable and cost-effective product. And the durable, scratch-resistant zinc coating will provide additional protection in the event the paint is scratched. The double layer protection of the duplex system will ensure the Amazeum retains its aesthetics and stays corrosion free.
Point Cadet Pavilion: Biloxi, MS; 2014
Driving over the Biloxi Bay Bridge one will see that a great transformation has taken place upon the completion of the Point Cadet Pavilion. The Point Cadet area is still struggling mightily to recover from the after-effects of Hurricane Katrina. The open-air pavilion is built on the site of a Coast Guard seaplane hanger that was completely destroyed by the storm and is built in a similar shape. The 10,000 square foot structure became very popular immediately and is already booked for months ahead. The pavilion will host family events, symphonies, crawfish boils, and many other special events for the community.
The combination of paint over galvanizing is very popular as architects and engineers look for strength, durability, and aesthetics for a sustainable project life. The duplex coated tubular structure provided all these at a cost-effective price that made the project feasible through the FEMA funds allocated for the project. The initial cost was competitive, the life-cycle cost and knowing the duplex coated steel would extend the life 1.5 times or more made hot-dip galvanizing and paint the logical choice.
The park has green space, a playground, a splash pad, restrooms and a beautiful pavilion all of which means a bright colorful future for Biloxi and Waterfront Park. The end result was a vibrant, aesthetically pleasing pavilion that will revitalize the park for generations.
Little Muncy Creek Bridge: Moreland Township, PA; 2015
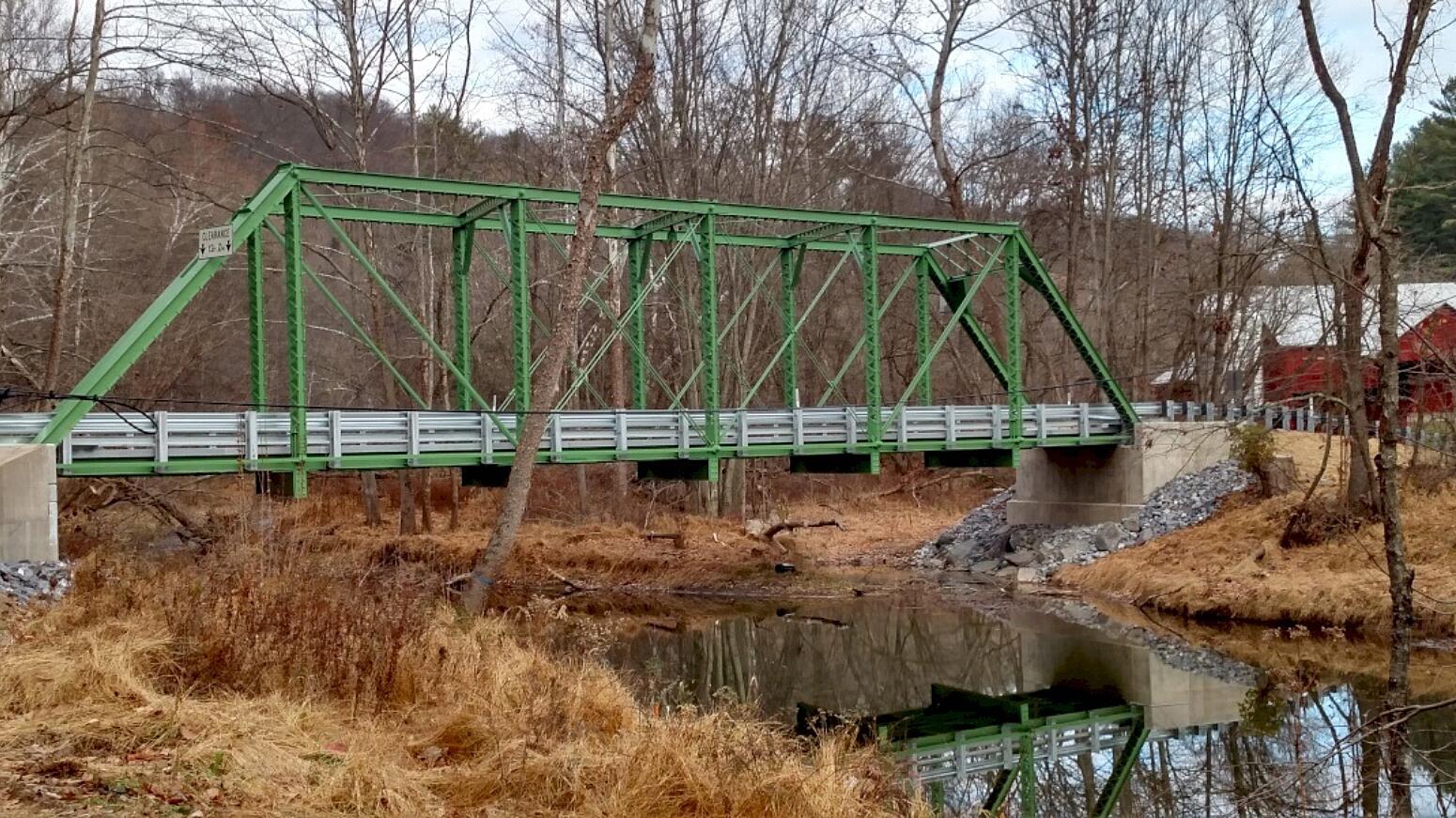
In 2009, Moreland Township, a small rural community in northeastern Pennsylvania, received some disturbing news about one of its most historic bridges, the Little Muncy Creek Bridge. This unique pin-connected truss bridge was originally built in 1904 by the Owego Bridge Company of Owego, New York. For over a century, the pin-connected truss bridge sat over the Little Muncy Creek, creating a path for local farm merchants to deliver fresh produce to town. The bridge received a superstructure condition rating of only a two out of a possible nine and was at that point deemed structurally deficient. As a result, the bridge was downgraded with weight restrictions until a suitable solution was determined.
In 2015, Moreland Township was granted a portion of Pennsylvania's $20 million funds to repair roads and bridges in Lycoming County. This was good news because the community had incurred tremendous cost throughout the years maintaining the original painted structure. They searched for more cost-effective ways to maintain the township's pride and joy (The Little Muncy Creek Bridge) which they felt reflected the personality of the region.
Fortunately, J.D. Eckman, the awarded contractor, knew that galvanizing the bridge would protect the steel from rust and corrosion for years to come and that the durability of hot-dip galvanizing would help solve their ongoing maintenance costs. But the community wanted the original forest green color so a duplex system was specified. Work began in the spring of that year replacing not only the superstructure but the road bridge decking as well. The galvanizer worked closely with the fabricator who had a responsibility to paint the final product. In the fall of 2015, the bridge was once again open for commerce, and the beautiful 113' long truss bridge stood proud, eloquently placed in the landscape of the Little Muncy Creek for decades to come.