Smooth & Clean the Surface
Once the condition of the galvanized surface has been properly identified, the next step is to clean the surface. There are three steps to cleaning the surface:
- Remove bumps, runs, and drips
- Remove organic materials
- Rinse and dry
Remove bumps, runs, and drips
(Responsibility for surface smoothing (galvanizer or paint applicator) to be agreed prior to galvanizing)
The first step requires the removal of any excess zinc produced when withdrawing the steel from the zinc bath. Small bumps and runs can cause concerns if the part is to be painted. As the steel is lifted out of the bath, the liquid zinc drains back into the kettle; however, at times the liquid zinc does not drain quickly enough and freezes to the surface or edge of a part. A run is excess zinc that freezes along the part, and a drip is excess zinc that freezes as it falls off the edge of the part, creating an icicle-like zinc spike.
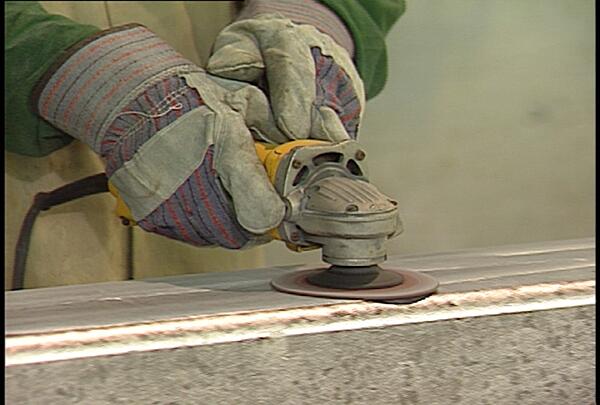
Another surface condition that must be addressed is the removal of dross particles. The zinc-iron intermetallic dross particles float in the zinc bath and can be trapped in the outer layer of the coating. Dross particles are thicker than the coating and cause bumps or pimples on the surface. All bumps, runs, drips, and dross particles must be smoothed so they will not protrude through the paint or powder coating.
The excess zinc areas (runs, drips, or dross particles) cannot be cleaned by chemical steps so they must be removed by mechanical cleaning such as grinding or filing the surface smooth and flat. The most common practice for removal is to use a hand grinder and lightly abrade away the excess zinc. The grinding and filing must be completed before the chemical cleaning of the part, so the dust and powder from mechanical cleaning can be removed by chemical cleaning. Since pure zinc is a soft metal, care must be taken to remove only the excess zinc material and leave a flat surface without removing the underlying zinc coating.
If the grinding process removes too much zinc, the grinder will begin to produce sparks, indicating it has reached the base steel. When sparks fly, the coating must be repaired before powder coating. Zinc coating repair methods are described in the specification ASTM A780 Standard Practice for Repair of Damaged and Uncoated Areas of Hot-Dip Galvanized Coatings, and include spray metallizing, zinc solder or repair stick, and zinc-rich paints.
Remove Organic Contaminents
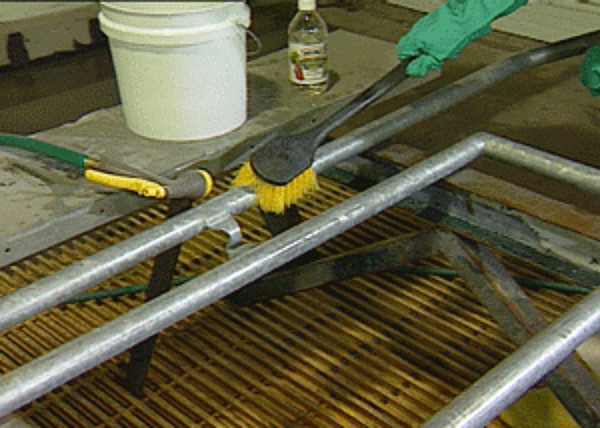
Once the galvanized surface is smooth, the next step for partially weathered galvanized steel involves removing all organic contaminants from its surface. Organic contaminants can be removed with an alkaline solution, acidic solution, or solvent cleaning. A mild alkaline solution, a mixture of ten parts water and one part alkaline cleaner, can remove all organics from the surface without damaging the galvanized coating. The alkaline solution can be brush applied or used with a power washer; however, if power washing the pressure must be held below 1450 psi to ensure the zinc coating is not damaged.
Organic contaminants can also be removed with a mild acidic solution, a mixture of 25 parts water to one part acid. The acidic solution will also slightly etch the zinc coating and leave the surface a dull gray color. Acidic solutions are usually brush applied and should be thoroughly rinsed off the part with fresh water no later than two to three minutes after application. It is good practice to rinse the part twice after using acidic solutions for cleaning.
Finally, solvent cleaning, applying solvents to the surface using a clean cloth, can be used. The cloth will pick up the organics, so it must be changed often to avoid re-depositing them onto he galvanized surface.
Rinse and Dry
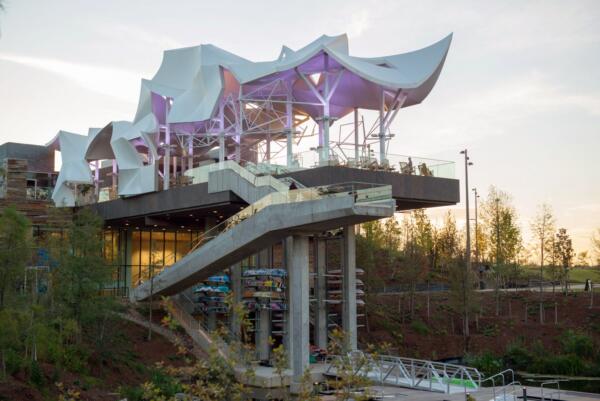
The final cleaning step uses fresh water to rinse the surface of any cleaning solutions. When using acid cleaning solutions, a second fresh water rinse is recommended to remove all traces of the acid cleaner. After the fresh water rinse, the part should be dried before proceeding to the profiling step. It is desirable to use heated drying to accelerate the complete removal of moisture from the surface.
As stated before, each of the surface conditions requires a different combination of these steps. Newly galvanized steel must have all bumps, runs, and drips ground flat, but can skip step two (removal of organic materials), because there is little or no accumulation of organics on newly galvanized surfaces. Upon completion of step one, the surface only requires a rinse and dry. Partially weathered galvanized steel, which is the most common surface condition to powder coat, requires all three steps. Fully weathered galvanized steel skips step one, as grinding the surface at this stage would not be beneficial. The zinc patina is fully formed and tightly adhered to the fully weathered surface, creating a more successful duplex system. Therefore, fully weathered galvanized steel only requires the removal of organic materials and a rinse and dry. If unable to determine the condition, it must be assumed the surface is partially weathered, and all cleaning steps must be followed.