Profile the Surface
Upon completion of cleaning, the galvanized surface must be profiled to provide an anchor for the paint or powder coating. Profiling the surface means to roughen all surfaces to be painted/powder coated to promote better adhesion. There are four potential methods to profile the surface for paint, and three for powder coating.
Sweep Blasting (Paint & Powder Coating)
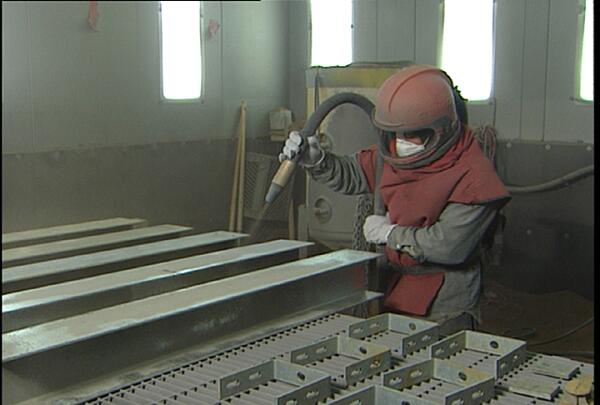
The first method to provide a profile on the surface is to sweep or brush blast the part per SSPC SP16. Sweep blasting is preferred over standard blasting because the zinc surface is relatively soft and a standard blast would remove most of the coating. Sweep blasting is angled onto the surface at 30 to 60 degrees to remove only the zinc compounds and not the zinc metal layer. Avoid standard blasting process because it uses a 90 degree angle to the part and will remove most of the galvanized coating.
The abrasive material must be chosen with care to provide a stripping action without removing excess zinc layers. One material used successfully is aluminum/magnesium silicate. Particle size should be in the range of 200 to 500 micrometers. Other potential materials are soft mineral sands with a Mohs hardness of five or less, or organic media such as corn cobs or walnut shells, or stone materials such as corundum or limestone. Do not use any blasting material with iron in the blast media, as this will cause powder coating adhesion issues and contaminate the galvanized coating.
Sweep blasting of zinc should not be greater than 40 PSI while using these abrasive materials. The substrate should be maintained at a temperature greater than three degrees centigrade above the dew point temperature. If the blasting step removes too much zinc coating, the zinc may be repaired by the process described in ASTM A 780.
Surface Grinding (Paint & Powder Coating)
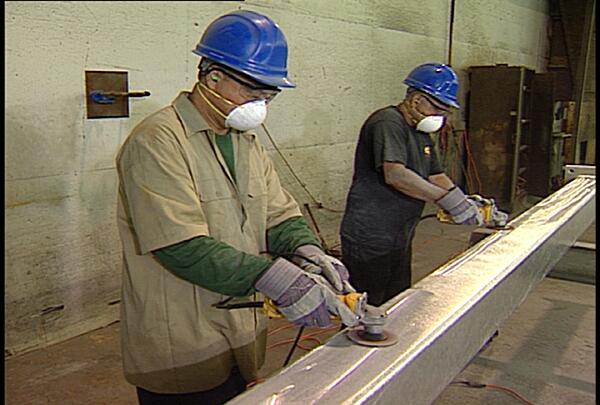
If necessary, power tools such as grinders or sanders can be used to roughen the surface of the galvanized steel to produce a surface profile suitable for paint or powder application and adhesion. A removal of up to 1 mil is acceptable, but the grinder should not be applied with enough force to completely strip the zinc coating. Afterwards, the surface should be blown off with compressed air. In some atmospheric conditions, such as high humidity, temperature, etc., the formation of zinc oxide on the surface will being very quickly, so the paint/powder coating should be applied immediately. Zinc oxide formation is not visible to the unaided eye; therefore, in any atmosphere, painting/powder coating should be started as soon as possible after surface preparation.
Wash Primer (PAINT ONLY)
Profiling the surface can also be done by treating the surface with a wash primer. The process is based on three primary components: a resin, a pigment, and an acid. These three components react with the zinc surface to form a thin film no more than 13 microns thick. The wash primer may be applied successfully using spray, and can also be applied by using a brush or roller. The drying time for this system before painting depends on the particular product and the manufacturers recommendation.
Acrylic Pretreatment (PAINT ONLY)
The third method of profiling the galvanized surface for painting is an acrylic passivation pretreatment. This system has an acidic element that etches and roughens the galvanized coating and then deposits an acrylic layer to facilitate paint adhesion. The application methods for these water-based treatments are: dipping, flow coating, spraying, or other appropriate means. Following application, the acrylic passivation coating is dried in an oven or by air before painting.
Zinc Phosphate Solution (POWDER ONLY)
Another method of profiling the galvanized surface is to passivate the surface with a zinc phosphate solution. The zinc phosphate reacts with the zinc metal on the surface of the part to form a layer of zinc compounds that are tightly bonded to the surface. This layer protects the surface from oxidation and gives a rough profile for good powder coating adherence. Zinc phosphate is applied by dipping the part in a tank of zinc phosphate solution. The part is then rinsed with fresh water and allowed to dry before the powder coating process begins. It is desirable to use heated drying to accelerate the complete removal of water from the surface.