More with Less
At every stage of construction, a hot-dip galvanized steel parking garage gives the consumer more - more design flexibility, more parking spaces, more options for future expansion, and more corrosion protection. In the initial design phase, clients must examine which type of structures grant the most options to get the job done efficiently and economically. Utilizing a steel framing system, specifiers can choose the most advantageous decking system from any of the three major categories: precast systems, cast-in-place floor slabs, or cast-in-place post-tensioned floor slabs. Other framing systems will limit the choice of decking.
More Design Flexibility
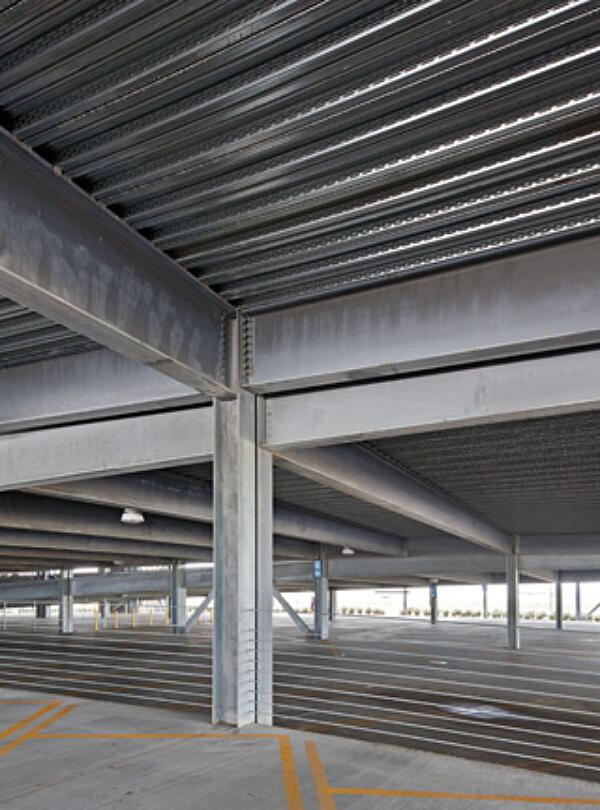
A steel core structure allows the designer more flexibility to adapt the structure to the site. By using techniques such as welding, bolting and splicing of existing columns, a steel framing system is easily adaptable to non-rectangular configurations that can be difficult to address with cast-in-place or precast concrete framing systems. With fewer, lighter pieces required and assembly techniques that can solve problems onsite, steel gives the designer more flexibility to negotiate problem areas and develop efficient solutions to challenging locations.
More Parking Spaces
The interior layout of the structure can also take advantage of the lightweight flexibility of exposed hot-dip galvanized steel beams. With slender beams carrying the weight of the garage on fewer, narrower columns, the designer will be able to fit more parking spaces into the same ground footprint. Steel columns require 80% less floor space than equivalent concrete columns1, increasing the usable floor area of the garage and decreasing the average cost-per-space of the design.
More Strength, Less Material
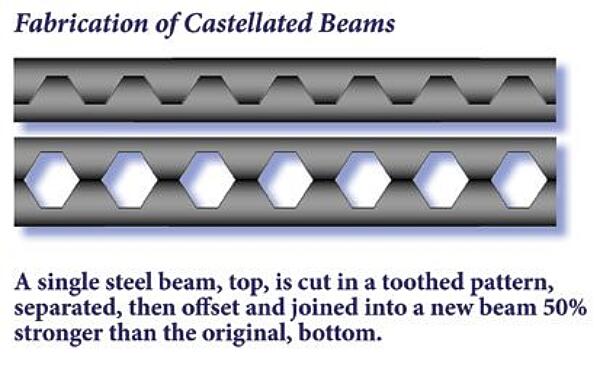
In addition to utilizing traditional steel members, one of the most efficient ways to capitalize on materials and space is by working with castellated beams. As seen in Figure 4, one steel beam is cut in either a toothed or circular pattern lengthwise, separated, offset, then rejoined into one cohesive piece.
The resulting beam is not only lighter but also 50% stronger than the original beam, maximizing the potential of a single piece of steel. Generally, the weight savings when castellated beams are utilized in a complete structure is 20 - 50%.2
There are many implications for such a weight-bearing, lightweight structural element. The increased strength of the castellated supports will allow for the possibility of more vertical stories and greater weight capacity per floor - meaning greater vehicle capacity for the garage.
Case Study:
Ayrsley Parking Deck, Charlotte, NC, 2007
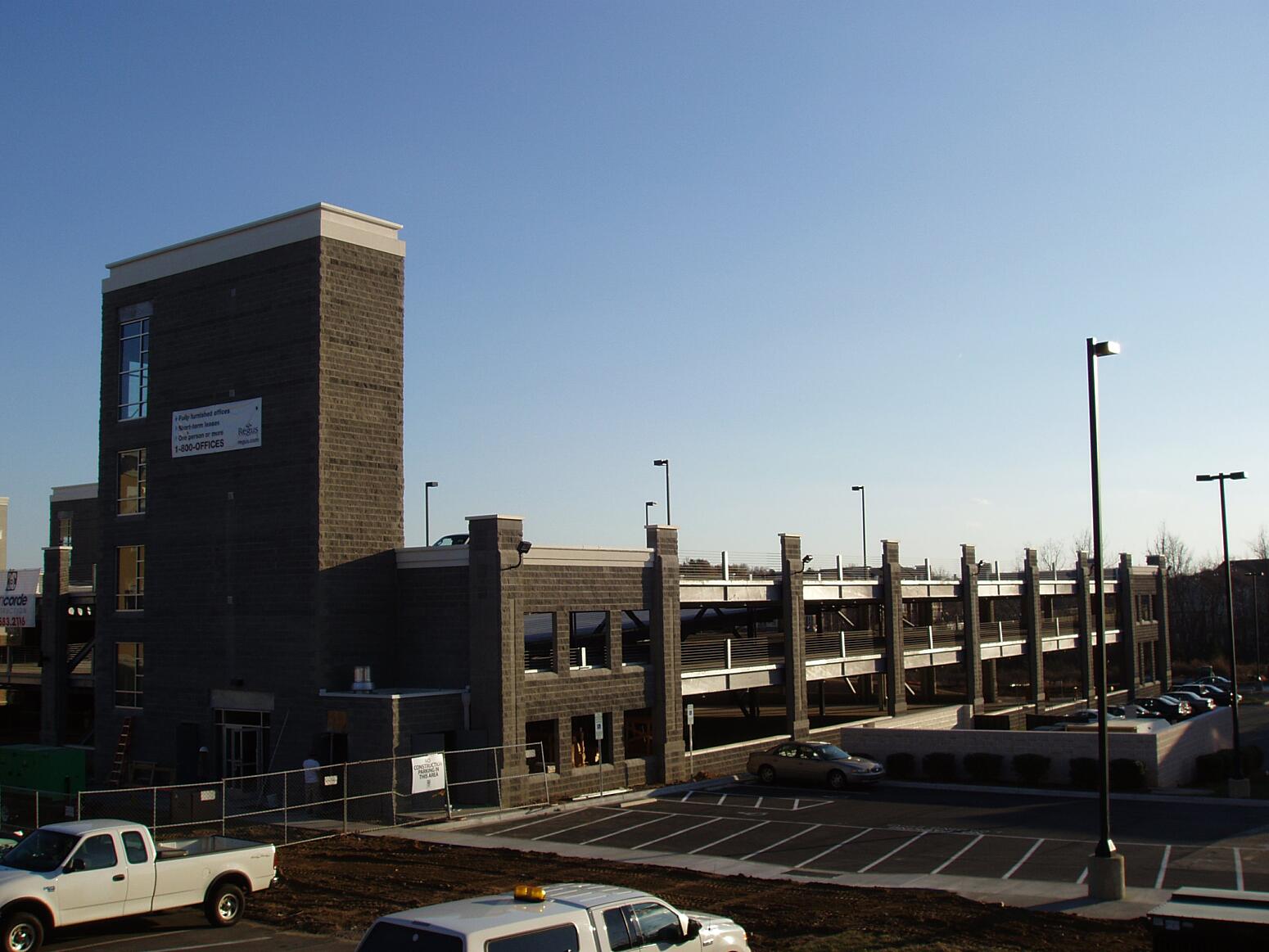
Arysley, located in the uptown area of southwest Charlotte, North Carolina, is sandwiched in the middle of the second largest job center in the region. The highly developed area of residential space, businesses, and mixed-use retail offers its residents services and the advantage of living near downtown in a pedestrian-friendly location.
To address a lack of parking space, city officials gathered with architects and engineers to construct a parking structure in the commercial portion of the development. Requiring a quick turnaround time and a need for economical material, the steel fabricator suggested using galvanized steel for aesthetics, sustainability, and corrosion protection. Unlike many galvanized parking decks covered with a precast concrete exterior, this parking deck has exposed galvanized steel as a design feature, making it an attractive addition to the mixed-use community.
The fabricator favored the use of hot-dip galvanizing due to previous success with the product and its advantages over using painted steel. All beams, columns, angle braces, plates and connection details were coated, as well as post-tensioned cables used for safety railing between floors and outer perimeters of the structure. 350 tons of steel received HDG, and the steel structure was constructed the record time of three weeks. These benefits made galvanizing the best choice, and will keep the parking deck looking the attractive for many years to come.
1 American Institute of Steel Construction (AISC). Innovative Solutions in Steel: Open-Deck Parking Structures.2003.
2 CMC Steel Group d/b/a CMC Steel Products, AISC. Long Span Steel Solutions. 2006.